Relacja SIM Gdynii z udziału w MSPO 2024 – prezentacja możliwości produkcji komponentów mechanicznych dla sektora obronnego
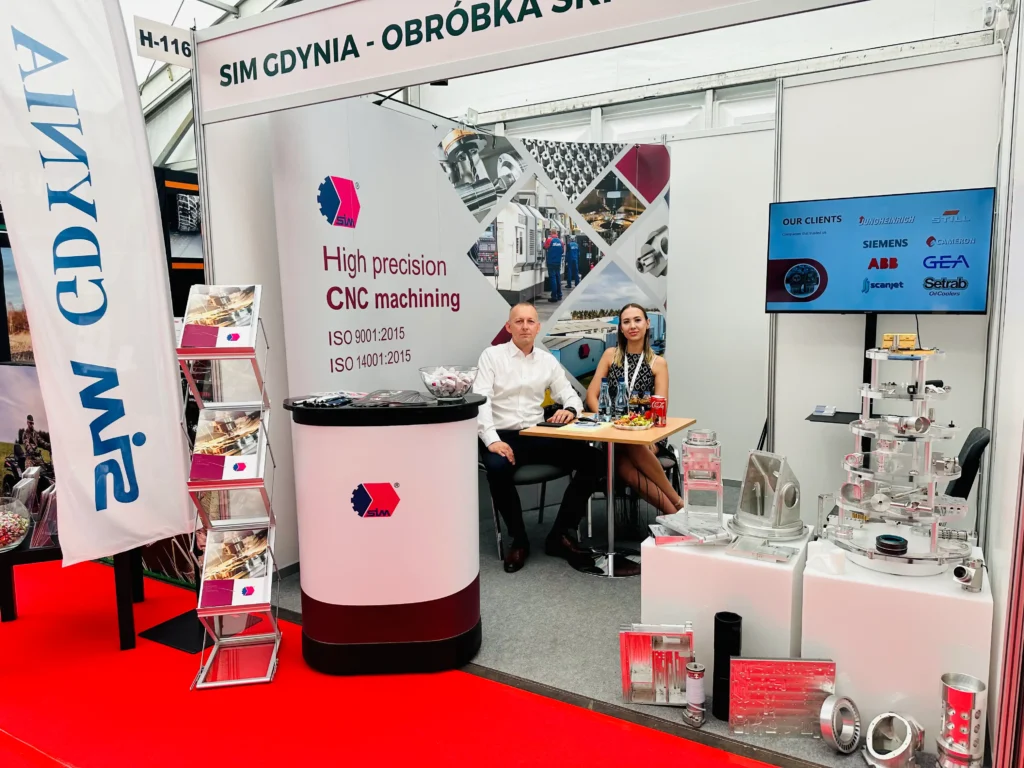
Udział SIM Gdynia na MSPO 2024 Uczestnictwo w Targach Międzynarodowego Salonu Przemysłu Obronnego (MSPO) 2024 umożliwiło nam zaprezentowanie możliwości technologicznych naszej produkcji CNC w środowisku skupiającym czołowych producentów zbrojeniowych, ekspertów oraz przedstawicieli administracji. Podczas targów prowadziliśmy rozmowy na temat zastosowania naszych technologii w krytycznych projektach obronnych oraz omówiliśmy potencjalne kierunki współpracy, w których możemy pełnić funkcję strategicznego dostawcy wysokoprecyzyjnych komponentów mechanicznych. Skrawanie CNC dla sektora obronnego – możliwości SIM Gdynia Nasze technologie CNC są zoptymalizowane pod kątem produkcji elementów o wysokiej dokładności oraz powtarzalności, co jest niezbędne w projektach obronnych. Zastosowanie pięcioosiowych centrów obróbczych oraz tokarek wielowrzecionowych pozwala nam na precyzyjne formowanie złożonych geometrii komponentów z materiałów o wysokiej wytrzymałości, takich jak stopy tytanu, aluminium lotnicze czy stale specjalne. Technologie te są stosowane w produkcji krytycznych elementów mechanicznych i optoelektronicznych, wykorzystywanych m.in. w broni, pojazdach wojskowych oraz systemach obrony przeciwrakietowej. Rekordowa frekwencja i kluczowe wydarzenia na MSPO 2024 MSPO 2024 zgromadziło rekordową liczbę uczestników – ponad 28 tysięcy osób z całego świata odwiedziło targi, aby zapoznać się z ofertą 769 firm, w tym 416 polskich. Wśród kluczowych wydarzeń, które miały miejsce podczas tegorocznej edycji, znalazły się podpisania kontraktów o łącznej wartości przekraczającej 2 miliardy złotych, w tym umowy z międzynarodowymi partnerami na dostawy nowoczesnych systemów obronnych. Równie istotne były spotkania przedstawicieli rządów oraz przemysłu obronnego, którzy wspólnie omawiali kwestie związane z bezpieczeństwem narodowym i technologicznym wsparciem dla wojska. Nowe projekty i rozbudowanie naszej współpraca z branżą obronną Podczas MSPO 2024 nawiązaliśmy liczne kontakty biznesowe, które mogą zaowocować nowymi projektami w zakresie produkcji komponentów dla systemów uzbrojenia oraz pojazdów wojskowych. Nasze kompetencje w dziedzinie obróbki CNC umożliwiają nam realizację projektów wymagających najwyższej precyzji i rozbudowanych rozwiązań technologicznych. Jako dostawca, jesteśmy w stanie sprostać wymaganiom stawianym przez aktualne i przyszłe systemy obronne, oferując zarówno produkcję jednostkową, jak i seryjną. Podsumowanie targów MSPO 2024 Nasze uczestnictwo w MSPO 2024 stanowiło ważny krok w dalszym rozwoju SIM Gdyni na rynku technologii dla sektora obronnego. Targi zgromadziły imponującą liczbę wystawców oraz odwiedzających, co stworzyło wyjątkowe warunki do nawiązywania kontaktów i prezentacji naszych rozwiązań w zakresie obróbki CNC. Dziękujemy wszystkim, którzy odwiedzili nasze stoisko i mieli okazję zapoznać się z naszą ofertą, obejmującą m.in. produkcję na wieloosiowych centrach obróbczych oraz systemy do precyzyjnej produkcji komponentów krytycznych dla systemów uzbrojenia.
SIM Gdynia wyróżniona w prestiżowym rankingu Forbes Forum Firm Rodzinnych 2024
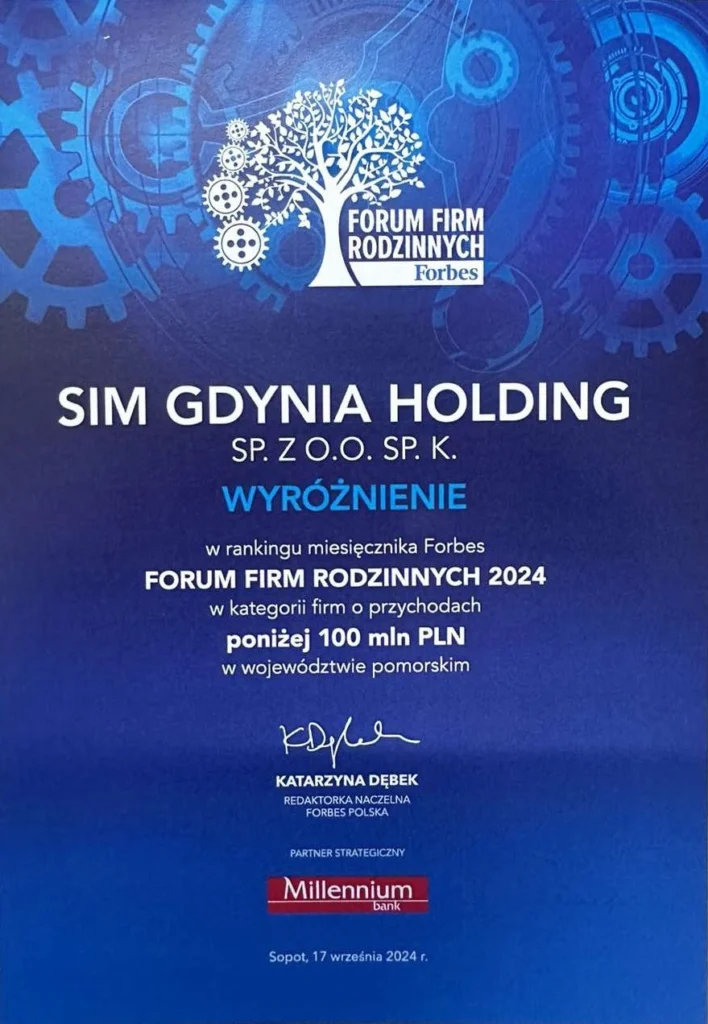
Ogłoszenie wyróżnienia Forbes dla SIM Gdynia Z radością informujemy, że SIM Gdynia znalazła się w gronie laureatów prestiżowego rankingu Forbes Forum Firm Rodzinnych 2024. W ramach klasyfikacji firm o przychodach poniżej 100 mln zł, nasze przedsiębiorstwo zostało wyróżnione za stabilną działalność oraz wyjątkowy wkład w rozwój regionalny. Nagroda ta jest nie tylko świadectwem naszej innowacyjności, ale również potwierdzeniem, że SIM Gdynia utrzymuje czołową pozycję w branży, zachowując najwyższe standardy operacyjne i technologiczne. Otrzymanie wyróżnienia Forbes to ogromne uznanie dla wieloletniego zaangażowania całego zespołu SIM Gdynia. Każdy pracownik, partner biznesowy oraz klient miał wkład w ten sukces, który jest wynikiem nieustannego doskonalenia procesów produkcyjnych oraz adaptacji do zmieniających się warunków rynkowych. Wyróżnienie to motywuje nas do dalszego rozwoju i poszukiwania nowych możliwości wdrażania zaawansowanych technologii w produkcji komponentów mechanicznych. Jesteśmy dumni z tego, że nasza firma może służyć jako przykład solidności i niezawodności na rynku krajowym i międzynarodowym. Forbes i jego znaczenie na rynku biznesowym Forbes to jedno z najbardziej renomowanych czasopism biznesowych na świecie, cenione za swoje analizy finansowe i rankingi, które wyznaczają standardy w ocenie kondycji firm. Publikacje Forbes, takie jak Diamenty Forbesa czy Global 2000, od lat są wyznacznikiem dla firm, które chcą potwierdzić swoją pozycję w światowej gospodarce. Ranking Forbes to nie tylko prestiż, ale również potwierdzenie wiarygodności finansowej oraz transparentności działań. Obecność w zestawieniu Forbes stanowi potwierdzenie najwyższych standardów zarządzania oraz silnej pozycji rynkowej przedsiębiorstw. Nagroda Forbes Forum Firm Rodzinnych: Kryteria i kategoria Ranking Forbes Forum Firm Rodzinnych to szczególne zestawienie, które wyróżnia przedsiębiorstwa o wyjątkowej reputacji, stabilności finansowej oraz dynamicznym rozwoju. VII edycja rankingu, opracowana przez magazyn Forbes we współpracy z firmą Dun & Bradstreet, bazuje na rygorystycznych kryteriach, obejmujących między innymi wieloletnią historię działalności, nieprzerwaną przez co najmniej pięć lat. W rankingu brane są pod uwagę wyniki finansowe za lata 2018-2022, a także wartość aktywów przedsiębiorstwa, wycenianych według szwajcarskiej metody, która dokładnie analizuje zarówno wartość dochodową, jak i majątek firmy. Przedsiębiorstwa są oceniane na podstawie ich rocznych przychodów i klasyfikowane w dwóch kategoriach: firmy z przychodami poniżej 100 mln zł oraz powyżej tej kwoty. To prestiżowe wyróżnienie dedykowane jest firmom, które wykazują się dodatnim wynikiem finansowym, transparentnością oraz istotnym wpływem na rozwój lokalnej społeczności. W tegorocznej edycji szczególny nacisk położono na ocenę firm rodzinnych, które dynamicznie rozwijają swoją działalność na rynkach krajowych i międzynarodowych. Podsumowanie i podziękowania dla zespołu oraz partnerów Nagroda Forbes to rezultat nie tylko stabilnego zarządzania, ale również współpracy całego zespołu SIM Gdynia. Dziękujemy naszym pracownikom, partnerom biznesowym oraz klientom za ich zaangażowanie, bez którego ten sukces nie byłby możliwy. Wierzymy, że to wyróżnienie otworzy przed nami nowe możliwości, umacniając naszą pozycję lidera w produkcji zaawansowanych komponentów mechanicznych. Przyszłość SIM Gdynia rysuje się w jasnych barwach, a dalsze inwestycje w nowoczesne technologie oraz innowacyjne rozwiązania pozwolą nam kontynuować dynamiczny rozwój na najwyższym poziomie.
Produkcja komponentów mechanicznych na obrabiarce CNC Miyano BNJ 42 w SIM Gdynia
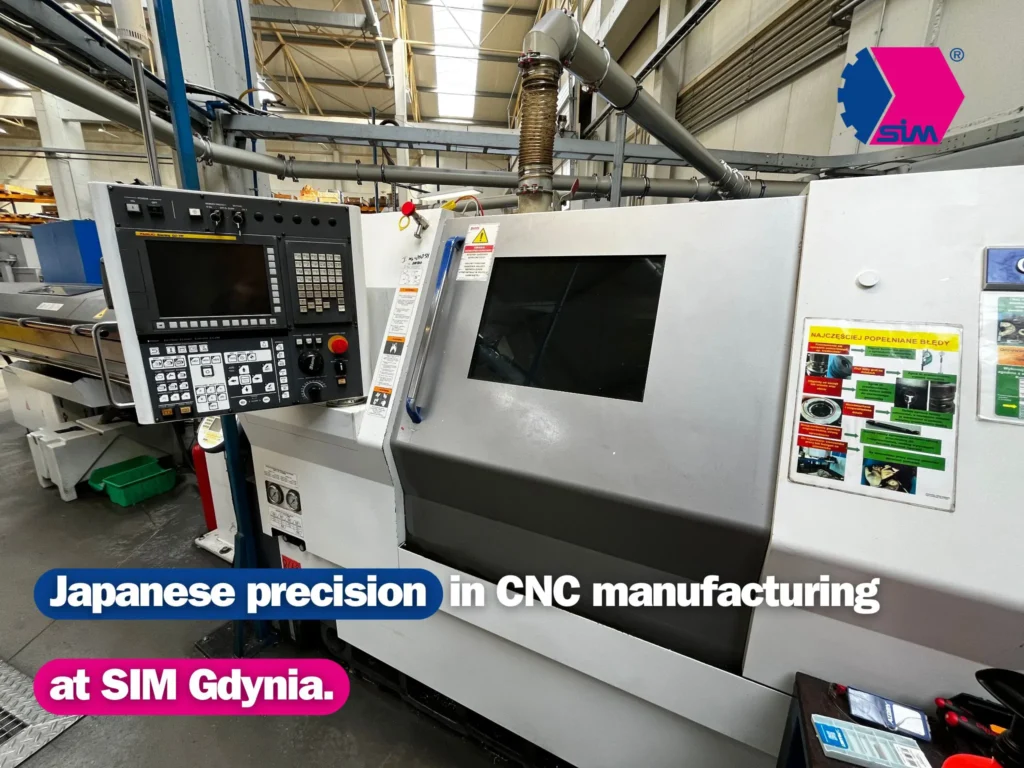
Wstęp Obrabiarki CNC Miyano BNJ 42 stanowią kluczowe narzędzia w parku maszynowym SIM Gdynia, umożliwiając efektywną produkcję skomplikowanych geometrycznie komponentów z zachowaniem najwyższych standardów jakości. Dzięki zastosowaniu automatycznych podajników oraz systemu chłodzenia olejem proces produkcji jest szybszy i bardziej ekonomiczny. Historia Miyano – producent obrabiarek CNC BNJ 42 Firma Miyano, założona w Japonii, zyskała uznanie na globalnym rynku dzięki swoim innowacyjnym i niezawodnym maszynom CNC. Od momentu powstania w pierwszej połowie XX wieku, Miyano skupiło się na rozwoju technologii obróbczych, które zmieniły branżę obróbki metali. Wprowadzenie modelu BNJ 42 było odpowiedzią na rosnące zapotrzebowanie przemysłu na obrabiarki umożliwiające szybką i precyzyjną produkcję przy jednoczesnym zmniejszeniu kosztów operacyjnych. Opis obrabiarek CNC Miyano BNJ 42 Obrabiarki CNC Miyano BNJ 42 wyposażone w dwie głowice obróbcze, umożliwiają jednoczesne przetwarzanie detali z dwóch stron. Proces obróbczy rozpoczyna się na jednej głowicy, gdzie realizowane są główne operacje, a po odcięciu detalu od materiału, druga głowica dokonuje dalszych precyzyjnych obróbek, które są niemożliwe do wykonania na pierwszej stronie. System chłodzenia olejem zastosowany w obrabiarce CNC BNJ 42 zapewnia optymalne warunki pracy narzędzi skrawających. W porównaniu do tradycyjnych chłodziw olej chłodzący lepiej radzi sobie z odprowadzaniem ciepła, co przekłada się na dłuższą żywotność narzędzi oraz lepszą jakość powierzchni obrabianych komponentów. Dodatkowym atutem jest zintegrowany system automatycznego podawania prętów, który umożliwia ciągłą i nieprzerwaną pracę maszyny, eliminując potrzebę ręcznego załadunku materiału. Warto podkreślić, że maksymalna średnica materiału, jaki jest w stanie obrabiać ten model obrabiarek to 42 mm. CNC w SIM Gdynia – zastosowanie BNJ 42 w produkcji W SIM Gdynia obrabiarki CNC Miyano BNJ 42 pełnią kluczową funkcję w naszym parku maszynowym, umożliwiając realizację skomplikowanych detali o średnicy do 42 mm. Dzięki zastosowaniu tych maszyn jesteśmy w stanie efektywnie wytwarzać duże serie komponentów, przy zachowaniu konkurencyjnego czasu realizacji zleceń i niskich kosztów produkcji w porównaniu do tradycyjnych rozwiązań. Automatyczne podajniki prętów w obrabiarkach BNJ 42 wyeliminowały ryzyko błędów związanych z czynnikiem ludzkim. Dodatkowo nasza produkcja może odbywać się bez przerw. Zastosowanie obrabiarek CNC Miyano BNJ 42 pozwoliło nam osiągnąć wysoki poziom powtarzalności w produkcji, przekładając się na naszą przewagę konkurencyjną.
Roboty załadunkowe wspierające produkcję CNC w SIM Gdynia – Fanuc M-710iC/45M
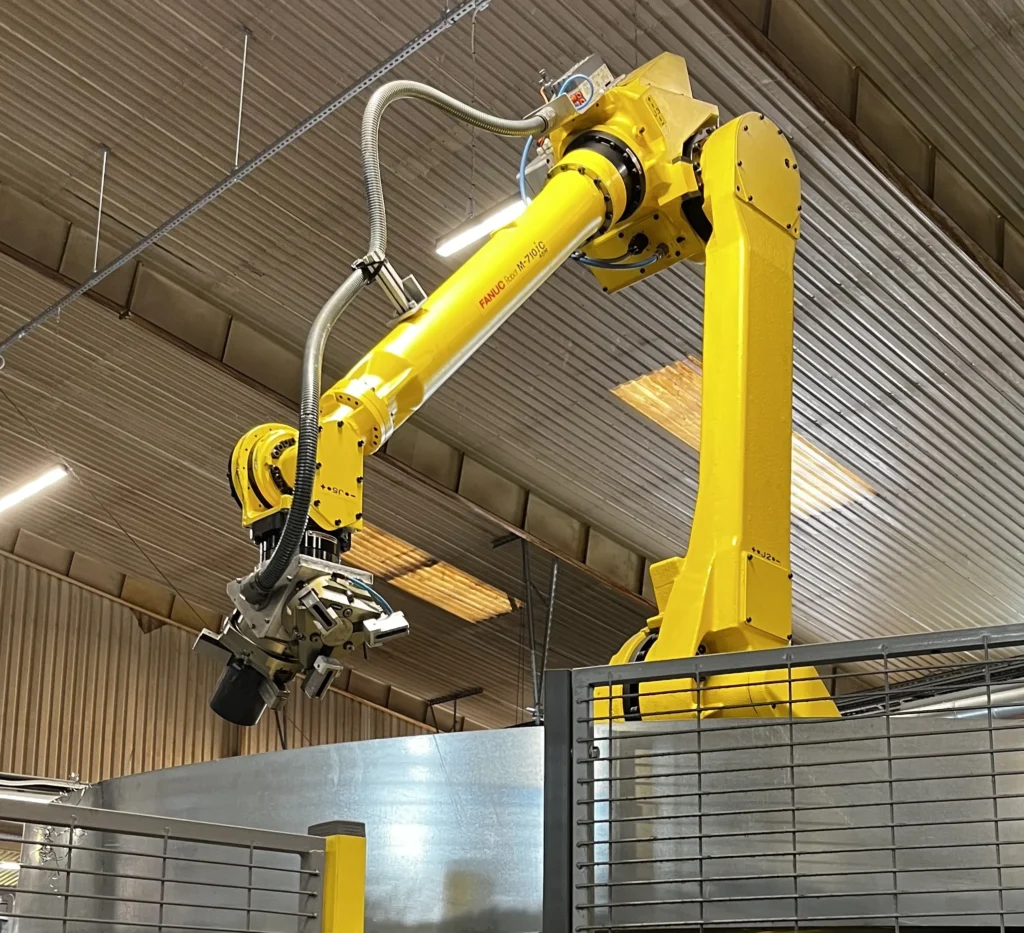
Wstęp Współczesna produkcja przemysłowa nieustannie zmierza w kierunku automatyzacji, aby sprostać rosnącym wymaganiom rynku oraz zwiększyć efektywność operacyjną. W SIM Gdynia procesy produkcyjne są wspierane przez nowoczesne roboty załadunkowe, które stanowią integralną część linii technologicznych. Wykorzystanie robotów takich jak Fanuc M-710iC/45M przyczynia się do zwiększenia wydajności oraz jakości wytwarzanych komponentów, co z kolei poprawia konkurencyjność firmy na globalnym rynku Automatyzacja w produkcji komponentów mechanicznych W obliczu rosnących oczekiwań dotyczących szybkości i precyzji produkcji, automatyzacja procesów staje się niezbędnym elementem współczesnych zakładów przemysłowych. Wysoka produkcja seryjna, szczególnie w branży CNC, wymaga zastosowania technologii, które umożliwiają nieprzerwaną pracę i minimalizację błędów ludzkich. Roboty załadunkowe, takie jak Fanuc M-710iC/45M, są kluczowym narzędziem w tym procesie, pozwalając na efektywne zarządzanie przepływem materiałów i optymalizację cyklu produkcyjnego. Roboty wielozadaniowe Fanuc M-710iC/45M Robot Fanuc M-710iC/45M to wszechstronne urządzenie zaprojektowane z myślą o szerokim zakresie zastosowań przemysłowych. Charakteryzuje się on kompaktową konstrukcją, która pozwala na instalację w miejscach o ograniczonej przestrzeni. Robot ten posiada sześć osi ruchu, z zasięgiem do 2606 mm, umożliwiając mu efektywne manewrowanie w dużej przestrzeni roboczej. Dzięki udźwigowi do 45 kg oraz prędkości operacyjnej 360 stopni na sekundę Fanuc M-710iC/45M jest idealny do szybkiego przenoszenia części i obsługi palet. Dodatkowym atutem jest jego pełna ochrona klasy IP67, co gwarantuje niezawodność działania w trudnych warunkach środowiskowych. Case study SIM Gdynia W SIM Gdynia roboty Fanuc M-710iC/45M zostały zintegrowane z liniami produkcyjnymi w celu obsługi naszych dwóch obrabiarek CNC jednocześnie. Przy każdej maszynie znajduje się stół z poruszającymi się paletami, na których roboty umieszczają detale. Proces rozpoczyna się od pobrania nieobrobionego detalu, po czym robot, w odpowiedzi na sygnał z maszyny, umieszcza go w odpowiedniej pozycji do obróbki. Po zakończeniu procesu detal jest odkładany na paletę, a stół przemieszcza się, przygotowując miejsce na kolejny element. Dzięki nim w SIM Gdynia realizujemy duże partie produkcyjne z zachowaniem najwyższych standardów jakości. Podsumowanie Automatyzacja procesów produkcyjnych w SIM Gdynia, z wykorzystaniem robotów załadunkowych Fanuc M-710iC/45M, stanowi doskonały przykład nowoczesnego podejścia do zarządzania produkcją w przemyśle CNC. Inwestycja w technologie wspomagające działanie linii produkcyjnych pozwalają nie tylko na zwiększenie efektywności, ale również na dostosowanie się do dynamicznie zmieniających się potrzeb rynku.
Systemy gaszenia obrabiarek skrawających AFFS-CNC – zalety, sposób działania i rodzaje środków gaśniczych
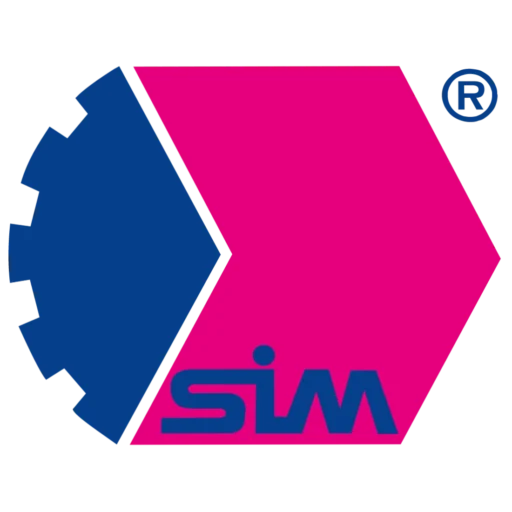
Wprowadzenie do Systemów Gaszenia AFFS-CNC Systemy gaszenia obrabiarek skrawających AFFS-CNC są kluczowym elementem zabezpieczeń przeciwpożarowych w nowoczesnych zakładach produkcyjnych. Pozwalają na skuteczne zapobieganie poważnym stratom materialnym i zapewniają bezpieczeństwo pracownikom podczas awarii maszyn. Rodzaje środków gaśniczych Systemy AFFS-CNC wykorzystują trzy różne środki gaśnicze, takie jak NOVEC 1230 (FK-5-1-12), proszek gaśniczy oraz dwutlenek węgla (CO2). NOVEC 1230 jest środkiem ekologicznym, niepozostawiającym osadów. Jest szczególnie bezpieczny dla delikatnych komponentów elektronicznych i mechanicznych. Proszek gaśniczy wykazuje wysoką skuteczność w gaszeniu pożarów wywołanych przez substancje łatwopalne. Dwutlenek węgla (CO2) idealnie nadaje się do gaszenia pożarów w miejscach, gdzie użycie wody lub innych substancji mogłoby uszkodzić sprzęt, dzięki zdolności do wypierania tlenu i skutecznego tłumienia ognia. Zalety systemów AFFS-CNC Systemy gaszenia AFFS-CNC charakteryzują się niezależnością od zewnętrznego zasilania elektrycznego, działając na bazie ciśnieniowej linii sterującej. Zapewnia to ich niezawodność nawet w przypadku awarii zasilania. W sytuacjach wymagających natychmiastowego wyłączenia obrabiarki, systemy te mogą być sterowane za pomocą czujników ciśnienia lub modułu sterowania AFFS-CNC/GSM. Dodatkowo moduł sterowania z funkcją GSM umożliwia szybkie powiadamianie o zagrożeniach. Zastosowanie i typy systemów gaszenia opartych na CO2 Systemy gaszenia z użyciem dwutlenku węgla (CO2) są szczególnie polecane do ochrony maszyn CNC. CO2 jest skutecznym środkiem gaśniczym, który nie przewodzi elektryczności, co czyni go bezpiecznym do użycia w środowiskach z dużą ilością sprzętu elektrycznego. Istnieją dwa główne typy systemów CO2: systemy całkowitego zatopienia, stosowane w zamkniętych przestrzeniach, gdzie CO2 może być skoncentrowany na stłumienie pożaru, oraz systemy lokalnego zastosowania, skierowane bezpośrednio na obszar zagrożony. Systemy gaszenia AFFS-CNC w SIM Gdynia W SIM Gdynia stosujemy system przeciwpożarowy oparty o dwutlenek węgla (CO2) na czterech maszynach Miyano, które są chłodzone olejem. System ten automatycznie wykrywa ogień wewnątrz maszyny i natychmiast uwalnia CO2, co prowadzi do szybkiego ugaszenia pożaru. Teoretycznie, po ugaszeniu pożaru i sprawdzeniu maszyny, produkcja może być natychmiast wznowiona. W praktyce nie mieliśmy okazji przetestować systemu gaszenia AFFS-CNC, ze względu na rzadkość awarii w naszym zakładzie. Jednak dokładamy wszelkich starań, aby zapewnić bezpieczeństwo naszych pracowników i ciągłość produkcji w razie wystąpienia pożaru. Konserwacja i bezpieczeństwo Regularna konserwacja systemów gaszenia jest kluczowa dla utrzymania ich wysokiej skuteczności. Konserwacja obejmuje kontrolę butli z CO2, dysz oraz czujników. Szkolenie personelu w zakresie obsługi systemu jest niezbędne do zapewnienia prawidłowej reakcji w przypadku pożaru. Wszelkie operacje z użyciem CO2 wymagają ścisłego przestrzegania norm bezpieczeństwa ze względu na potencjalne zagrożenie dla ludzi przy wysokim stężeniu tego gazu. Podsumowanie Systemy gaszenia AFFS-CNC oferują niezawodność, wysoką skuteczność oraz elastyczność w dostosowywaniu do specyficznych potrzeb klienta. Dzięki nim możliwe jest zapewnienie maksymalnego bezpieczeństwa i ochrony inwestycji w sprzęt.
Jak powstało CNC? – historia obróbki skrawaniem CNC
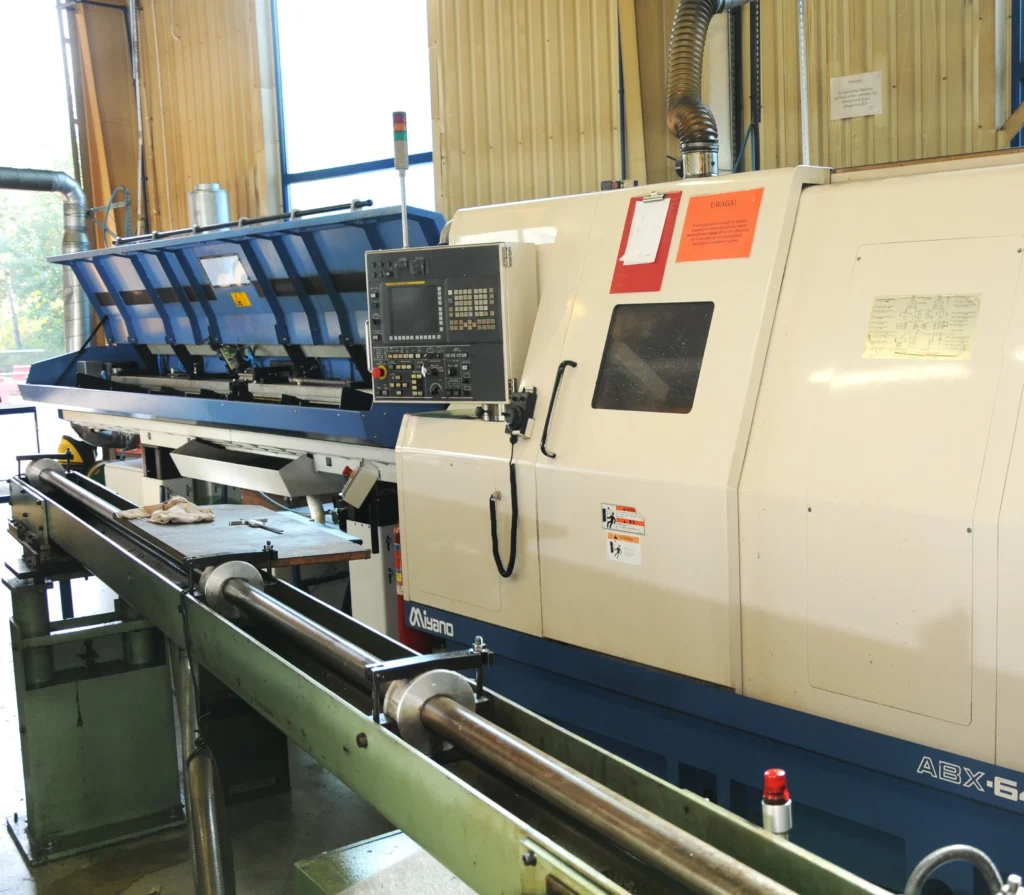
Wprowadzenie CNC, czyli Computer Numerical Control, to technologia, która zrewolucjonizowała przemysł produkcyjny. Dzięki zastosowaniu komputerowego sterowania urządzeniami, takimi jak frezarki, tokarki i elektrodrążarki, CNC umożliwiło szybkie, precyzyjne i powtarzalne wykonywanie złożonych geometrycznie kształtów komponentów mechanicznych. Początki technologii NC Technologia CNC wywodzi się bezpośrednio z technologii NC (Numerical Control), która pojawiła się na początku lat 40. XX wieku. NC, czyli sterowanie numeryczne, polegało na programowaniu maszyn za pomocą taśm dziurkowanych, które zawierały instrukcje dotyczące ruchów maszyny. John T. Parsons, w kooperacji z Massachusetts Institute of Technology (MIT), nie tylko opracował te maszyny, ale także jako pierwszy wykorzystał metody komputerowe do rozwiązywania problemów obróbki, w tym precyzyjnej interpolacji krzywych opisujących łopaty wirników helikopterów. Kiedy technologia NC wyewoluowała w CNC? Przejście od technologii NC do CNC nastąpiło w latach 50. XX wieku. W 1952 roku zespół badaczy z MIT opracował pierwszą maszynę CNC, która wykorzystywała komputer do sterowania ruchami maszyny. Pierwsze komercyjne maszyny CNC zostały wprowadzone na rynek dzięki współpracy MIT z firmą Cincinnati Milacron. Te maszyny zrewolucjonizowały przemysł produkcyjny, pozwalając w pewnym stopniu na programowanie trajektorii narzędzi. Ewolucja technologii CNC w latach 60. i 70. W latach 60. i 70. technologia CNC zaczęła zyskiwać na popularności. Choć pierwsze wersje oprogramowania CAD (Computer Aided Design) pojawiły się w późniejszym okresie, to w tych dekadach rozpoczęto rozwój wstępnych systemów, które były prekursorami dla pełnoprawnych rozwiązań CAD. Te wczesne systemy umożliwiały tworzenie prostszych modeli, które stanowiły podstawę do generowania kodów G, używanych do sterowania maszynami CNC. Dodatkowo w latach 70. rozpoczęto eksperymentowanie z pierwszymi konfiguracjami maszyn wieloosiowych, co stanowiło znaczący krok naprzód w obróbce skomplikowanych geometrii. Te wczesne maszyny wieloosiowe pozwalały na obróbkę detalu z różnych kątów w jednym ustawieniu. Jak wyglądał rozwój CNC w latach 80.? Lata 80. przyniosły znaczne innowacje w technologii CNC, zasadniczo zmieniając przemysł obróbki. Rozwój oprogramowania CAD/CAM umożliwił projektantom i inżynierom bardziej efektywne projektowanie komponentów, które mogły być bezpośrednio przesyłane do maszyn CNC. Wprowadzenie bardziej intuicyjnych interfejsów i systemów sterowania zwiększyło produktywność i ułatwiło obsługę obecnych wtedy maszyn. Rozwój technologii CNC w latach 90. i na początku XXI wieku W latach 90., znaczące postępy w technologii CNC objawiły się poprzez wprowadzenie wielofunkcyjnych maszyn, które połączyły różne operacje obróbkowe w jednej stacji, znacznie usprawniając procesy produkcyjne. Wprowadzenie systemów ERP (Enterprise Resource Planning), pozwoliło na lepsze zarządzanie zasobami produkcyjnymi i usprawniło planowanie produkcji. Na początku nowego tysiąclecia, rozwój maszyn 5-osiowych i sieci przemysłowych, takich jak Ethernet, pozwolił na zdalne sterowanie i monitorowanie procesów. Wzrost automatyzacji i robotyzacji przyczynił się do zwiększenia wydajności operacji oraz zmniejszenia interwencji operatora. CNC w dzisiejszych czasach – case study z SIM Gdynia Dzięki licznych usprawnieniom w funkcji skrawania oraz nowym generacjom obrabiarek CNC nasz park maszynowy w SIM Gdynia osiągnął znacznie wyższą efektywność produkcji. Nasze 5-osiowe centra obróbcze są w stanie obrabiać złożone geometrie w jednym ustawieniu, eliminując konieczność ręcznego przestawiania detalu. Nasze zintegrowane systemy automatycznego podawania materiałów oraz roboty przemysłowe współdziałają z urządzeniami CNC, w załadunku i rozładunku, zapewniając ciągłość produkcji i optymalny czas cyklu. Podsumowanie Obecnie technologia CNC jest integralną częścią nowoczesnego przemysłu, umożliwiając realizację najbardziej skomplikowanych projektów i otwierając nowe możliwości dla firm na całym świecie. Dzięki ciągłemu rozwojowi technologii i integracji z nowymi systemami CNC pozostaje na czele innowacji przemysłowych, napędzając cyfrową transformację i tworząc przyszłość produkcji.
Czym jest Mikroobróbka CNC? – omówienie technologii obróbki
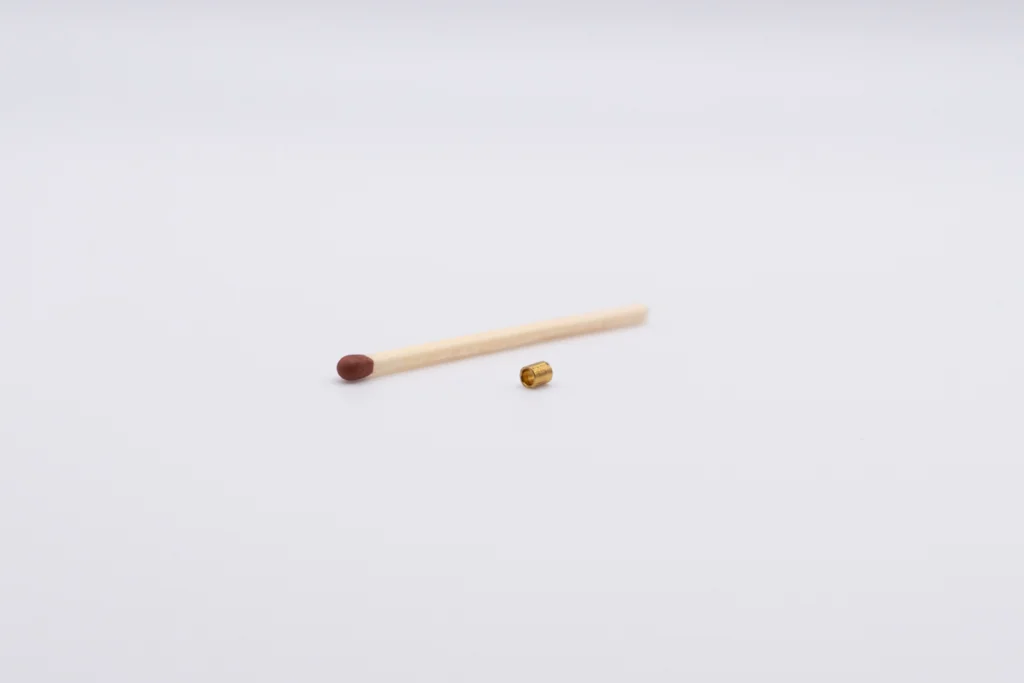
Wprowadzenie Mikroobróbka to procesy, takie jak mikrofrezowanie i mikrowiercenie, które umożliwiają produkcję komponentów o ekstremalnie małych rozmiarach i wysokiej precyzji. Techniki te wykorzystują maszyny CNC (Computer Numerical Control), zdolne do wykonywania skomplikowanych operacji na bardzo małych powierzchniach. Dzięki mikroobróbce możliwe jest tworzenie detali spełniających rygorystyczne wymagania branż takich jak militarna, medyczna i lotnictwo. Czym jest mikrofrezowanie i mikrowiercenie? Mikrofrezowanie to proces usuwania materiału przy użyciu mikrofrezów, które są znacznie mniejsze od standardowych frezów. Pozwala ono na precyzyjne kształtowanie i wykańczanie powierzchni detali o mikroskopijnych wymiarach, co jest kluczowe w produkcji komponentów o wysokiej precyzji. Typowe mikrofrezarki mogą osiągać tolerancje rzędu kilku mikrometrów, co jest niezbędne w aplikacjach wymagających dużej dokładności. Mikrowiercenie polega na tworzeniu otworów za pomocą mikrowierteł o bardzo małej średnicy, często poniżej 0,1 mm. Proces ten jest niezbędny w aplikacjach wymagających ekstremalnej precyzji, takich jak wytwarzanie otworów w układach mikroelektronicznych czy medycznych implantach. Oba te procesy są częścią szerszej kategorii mikroobróbki, która obejmuje wszelkie operacje skrawania i kształtowania materiałów na mikroskopijną skalę. Mikroobróbka umożliwia osiągnięcie niespotykanej dotąd precyzji i jakości wykończenia powierzchni. Jakie narzędzia skrawające wykorzystuje się w mikroobróbce? – przykłady Węgliki spiekane Węgliki spiekane to materiały kompozytowe, które charakteryzują się wyjątkową twardością i odpornością na zużycie. Są one wykonane z połączenia węglika wolframu (WC) i metalicznego kobaltu (Co), co daje im doskonałe właściwości mechaniczne i trwałość. Twardość węglików spiekanych wynosi zwykle około 1500–2000 HV (Vickersa), co pozwala im na skuteczną obróbkę nawet bardzo twardych materiałów. Węgliki spiekane charakteryzują się również wysoką odpornością na ściskanie, osiągając wytrzymałość do 5000 MPa, oraz niską przewodnością cieplną, co pozwala na zachowanie ostrości krawędzi tnącej nawet przy wysokich temperaturach. Zastosowanie w produkcji mikrofrezów i mikrowierteł Węgliki spiekane są powszechnie stosowane do produkcji mikrofrezów i mikrowierteł ze względu na ich wytrzymałość i zdolność do utrzymania ostrej krawędzi tnącej. Dzięki nim możliwe jest precyzyjne wykonywanie mikrootworów i mikrokanalików w twardych materiałach, takich jak stal nierdzewna czy stopy tytanu. Węgliki spiekane są również odporne na korozję, co jest istotne w obróbce materiałów o agresywnych właściwościach chemicznych. Diamenty syntetyczne (PCD – Polycrystalline Diamond) Diamenty syntetyczne, znane również jako PCD (Polycrystalline Diamond), to materiały składające się z wielu małych kryształków diamentu połączonych w jeden. Charakteryzują się one ekstremalną twardością, wynoszącą około 8000 HV (Vickersa), oraz wysoką odpornością na zużycie. PCD charakteryzuje się również wysoką przewodnością cieplną, wynoszącą około 1000 W/mK, co pozwala na skuteczne odprowadzanie ciepła generowanego podczas obróbki. Dzięki temu narzędzia PCD zachowują swoje właściwości tnące przez dłuższy czas. Zastosowanie w mikroobróbce Dzięki swojej odporności na ścieranie, narzędzia PCD zapewniają dłuższą żywotność i możliwość utrzymania wysokiej jakości wykończenia powierzchni. Wykorzystanie PCD w mikroobróbce umożliwia osiągnięcie nieosiągalnej wcześniej precyzji. Narzędzia wykonane z PCD są szczególnie efektywne przy obróbce materiałów kompozytowych oraz ceramiki, co czyni je niezastąpionymi w wielu zaawansowanych zastosowaniach technologicznych. PCD jest również odporne na chemiczne oddziaływanie wielu materiałów, co pozwala na ich zastosowanie w szerokim zakresie środowisk pracy. Maszyny CNC w mikroobróbce – co jest istotne? Maszyny wieloosiowe (5-osiowe CNC) Maszyny 5-osiowe CNC umożliwiają ruch narzędzia w pięciu różnych osiach jednocześnie. Oprócz standardowych trzech osi liniowych (X, Y, Z), posiadają dwie dodatkowe osie obrotowe, które pozwalają na skomplikowaną obróbkę przestrzenną. Dzięki temu możliwe jest wykonywanie precyzyjnych operacji na złożonych powierzchniach bez konieczności wielokrotnego przestawiania detalu. Eliminując w taki sposób błąd ”ludzki”. Maszyny o wysokiej sztywności i tłumieniu wibracji Znaczenie minimalizowania wibracji Wibracje mogą prowadzić do pogorszenia jakości powierzchni, skrócenia żywotności narzędzi oraz zmniejszenia precyzji obróbki. Są one niepożądanym efektem, który może wynikać z nieodpowiedniej sztywności maszyny, niewłaściwego mocowania detalu lub nieoptymalnych parametrów skrawania. Maszyny o wysokiej sztywności konstrukcyjnej i efektywnym tłumieniu wibracji zapewniają stabilność procesu obróbki, co przekłada się na wyższą jakość i powtarzalność wyników. Przykłady maszyn o wysokiej sztywności Przykładami maszyn o wysokiej sztywności i zdolności do tłumienia wibracji są zaawansowane centra obróbcze od takich producentów jak Makino, Okuma czy Mori Seiki. Maszyny te są zaprojektowane z myślą o maksymalnej stabilności i precyzji obróbki, wykorzystując materiały i konstrukcje o dużej masie i sztywności. Dodatkowo wyposażone są w zaawansowane systemy tłumienia wibracji, które aktywnie monitorują i kompensują drgania podczas procesu skrawania. Na przykład, centra obróbcze Makino T-Series, znane z precyzji i stabilności, oferują systemy tłumienia wibracji Vibration Control System (VCS), które automatycznie dostosowują parametry obróbki w czasie rzeczywistym, aby zapewnić optymalne warunki pracy. Czym są cyfrowe bliźniaki i jaki wpływ mają na dokładność mikroobróbki CNC? Cyfrowe bliźniaki to wirtualne modele fizycznych maszyn i procesów produkcyjnych. Dzięki zaawansowanym technologiom cyfrowym, takim jak IoT (Internet of Things), sztuczna inteligencja (AI) oraz analityka danych, cyfrowe bliźniaki umożliwiają symulację, monitorowanie i analizę rzeczywistych procesów w czasie rzeczywistym. Te wirtualne reprezentacje mogą dokładnie odwzorowywać zachowanie rzeczywistych systemów, pozwalając na przewidywanie ich reakcji na różne warunki operacyjne. Cyfrowe bliźniaki wykorzystują dane zbierane z czujników zamontowanych na rzeczywistych maszynach, które są następnie przetwarzane i analizowane w celu stworzenia dokładnego modelu wirtualnego. Dzięki temu możliwe jest monitorowanie stanu maszyn, wykrywanie anomalii oraz przewidywanie potencjalnych awarii przed ich wystąpieniem. Cyfrowe bliźniaki mogą również służyć do optymalizacji procesów produkcyjnych poprzez symulację różnych scenariuszy operacyjnych i wybór najbardziej efektywnego z nich. Chłodziwa i smarowanie w mikroobróbce Minimal Quantity Lubrication (MQL) Minimal Quantity Lubrication (MQL) to technika smarowania, która polega na zastosowaniu minimalnych ilości chłodziwa bezpośrednio na narzędzie i miejsce skrawania. W przeciwieństwie do tradycyjnych metod chłodzenia, które wymagają dużej ilości cieczy, MQL wykorzystuje zaledwie kilka mililitrów na godzinę. Smarowanie odbywa się za pomocą mgły olejowej, która skutecznie zmniejsza tarcie i temperaturę, jednocześnie minimalizując zużycie chłodziwa. Korzyści ekologiczne i ekonomiczne MQL Technika MQL oferuje liczne korzyści ekologiczne i ekonomiczne. Redukcja zużycia chłodziwa przekłada się na mniejsze obciążenie środowiska, zmniejszając ilość odpadów i zużycie zasobów naturalnych. Ponadto mniejsze zużycie chłodziwa oznacza niższe koszty eksploatacyjne i konserwacyjne, co jest korzystne dla przedsiębiorstw. Dodatkowo MQL poprawia warunki pracy, zmniejszając ryzyko związane z wyciekami chłodziwa i zanieczyszczeniami. Zastosowanie MQL eliminuje konieczność utylizacji dużych ilości chłodziw. Podsumowanie Technologie mikroobróbki CNC umożliwiają realizację skomplikowanych komponentów o wysokiej precyzji, które znajdują zastosowanie w sektorze lotniczym, medycznym i wojskowym. Omawiane narzędzia, takie jak węgliki spiekane i diamenty syntetyczne (PCD), oraz zalety maszyn 5-osiowych CNC rewolucjonizują dzisiejszy rynek produkcji komponentów mechanicznych.
Metody magazynowania w nowoczesnych magazynach przemysłowych
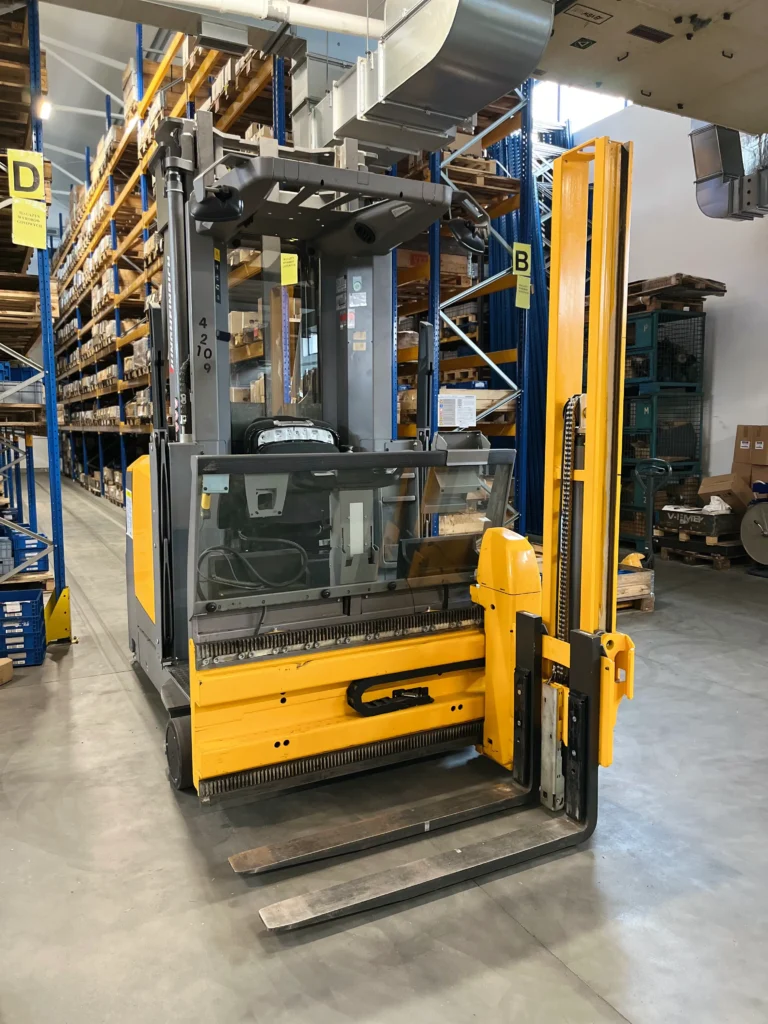
Wprowadzenie Tradycyjne metody magazynowania, takie jak magazyny paletowe, które polegają na przechowywaniu towarów na standardowych paletach w regałach statycznych, są coraz częściej zastępowane przez nowoczesne rozwiązania. Pozwalają one na lepsze wykorzystanie dostępnej przestrzeni, zwiększają efektywność operacyjną i poprawiają bezpieczeństwo w magazynach. Systemy regałów wysokiego składowania Systemy regałów wysokiego składowania umożliwiają przechowywanie towarów na wysokościach sięgających nawet 18 metrów, co pozwala na maksymalne wykorzystanie pionowej przestrzeni magazynowej. Systemy te, często wspierane przez wózki widłowe o specjalnych konstrukcjach, zapewniają szybki i efektywny dostęp do składowanych towarów. Wózki takie jak EKX serii 4 i 5, wyposażone w obrotową karetkę wideł oraz bezobsługowe synchroniczne silniki reluktancyjne, umożliwiają operowanie na dużych wysokościach z wysoką efektywnością energetyczną i precyzją. Automatyczne systemy składowania i pobierania (AS/RS) Automatyczne Systemy Składowania i Pobierania (AS/RS) to rozwiązania technologiczne, które składają się z regałów obsługiwanych przez zautomatyzowane wózki lub roboty. Te systemy, zaprojektowane do efektywnego składowania i pobierania towarów, mogą znacznie zwiększyć efektywność operacyjną magazynu, minimalizując czas potrzebny na te operacje oraz redukując ryzyko błędów ludzkich. AS/RS wykorzystują precyzyjne algorytmy oraz zaawansowane czujniki do zarządzania towarami, a ich integracja z systemami zarządzania magazynem (WMS) pozwala na pełną automatyzację i optymalizację procesów magazynowych. Magazyny automatyzowane (Smart Warehouses) Magazyny automatyzowane, znane również jako smart warehouses, wykorzystują zaawansowane technologie takie jak sztuczna inteligencja (AI), Internet Rzeczy (IoT) oraz robotyka do optymalizacji operacji magazynowych. Systemy AGV (Automated Guided Vehicles) są używane do transportu towarów, podczas gdy drony wykonują inwentaryzację i monitorowanie stanu magazynowego. AI i IoT pozwalają na zbieranie, analizowanie i przetwarzanie danych w czasie rzeczywistym, co prowadzi do pełnej automatyzacji procesów, znacząco poprawiając efektywność i redukując koszty operacyjne. Systemy zarządzania magazynem (WMS) Systemy Zarządzania Magazynem (WMS) to oprogramowanie pozwalające na efektywne zarządzanie operacjami magazynowymi. WMS umożliwiają śledzenie i zarządzanie wszystkimi operacjami magazynowymi w czasie rzeczywistym, od przyjęcia towaru do jego wysyłki. Funkcje WMS obejmują zarządzanie zapasami, optymalizację składowania, planowanie pracy personelu oraz integrację z systemami ERP (Enterprise Resource Planning). Dzięki WMS możliwe jest zwiększenie dokładności operacji magazynowych, redukcja kosztów i poprawa ogólnej efektywności. Technologie RFID i IoT RFID (Radio-Frequency Identification) RFID, czyli Radio-Frequency Identification, to technologia umożliwiająca automatyczne identyfikowanie i śledzenie towarów za pomocą fal radiowych. System RFID składa się z tagów (etykiet) wyposażonych w chipy i anteny oraz czytników, które wysyłają sygnały radiowe do tagów. Dzięki temu możliwe jest zdalne odczytywanie informacji zapisanych na tagach, co znacząco zwiększa dokładność i efektywność operacji magazynowych, eliminując potrzebę ręcznego skanowania kodów kreskowych. Internet Rzeczy (IoT) Internet Rzeczy (IoT) to sieć połączonych urządzeń i czujników, które zbierają i wymieniają dane w czasie rzeczywistym. W kontekście magazynowania IoT pozwala na monitorowanie i zarządzanie różnymi aspektami operacji magazynowych, takimi jak stan zapasów, warunki środowiskowe (np. temperatura i wilgotność) oraz lokalizacja towarów. Integracja IoT z systemami WMS umożliwia lepsze zarządzanie zapasami i optymalizację procesów logistycznych, dzięki czemu magazyny stają się bardziej responsywne i efektywne. Magazynowanie w chmurze (Cloud Storage Management) Magazynowanie w chmurze, czyli zarządzanie magazynem poprzez systemy oparte na chmurze, staje się coraz bardziej popularne w nowoczesnych magazynach. Systemy te umożliwiają dostęp do danych magazynowych z dowolnego miejsca i o każdej porze, co zwiększa elastyczność i skalowalność operacji magazynowych. Zarządzanie w chmurze oferuje również analizy danych, które pomagają w optymalizacji procesów magazynowych oraz przewidywaniu przyszłych potrzeb. Dzięki chmurowym systemom zarządzania możliwe jest także łatwe integrowanie z innymi systemami ERP i WMS, co poprawia współpracę i koordynację działań w całym łańcuchu dostaw. Magazynowanie w SIM Gdynia W SIM Gdynia oferujemy kompleksowe usługi magazynowania, które wykorzystują najnowocześniejsze rozwiązania technologiczne, aby zapewnić maksymalną efektywność i bezpieczeństwo. Nasz wózek widłowy EKX 410 serii 4, wyposażony w obrotową karetkę wideł oraz bezobsługowe synchroniczne silniki reluktancyjne, operuje na wysokościach do 11.5m, pozwalając efektywniej wykorzystać przestrzeń magazynową. Oferujemy także kompleksowe zarządzanie towarami, od ich przyjęcia, poprzez składowanie, aż po kompletację i wysyłkę. Podsumowanie Nowoczesne metody magazynowania, które obejmują systemy regałów wysokiego składowania, automatyczne systemy składowania i pobierania (AS/RS), magazyny zautomatyzowane, systemy zarządzania magazynem (WMS), technologie RFID i IoT oraz magazynowanie w chmurze, znacząco zwiększają efektywność, bezpieczeństwo i elastyczność operacji magazynowych. Te rozwiązania pozwalają na lepsze wykorzystanie dostępnej przestrzeni, redukcję kosztów operacyjnych i poprawę ogólnej wydajności magazynów.
Tokarka pionowa EMAG VL2 – charakterystyka techniczna, sposób działania oraz case study SIM Gdynia
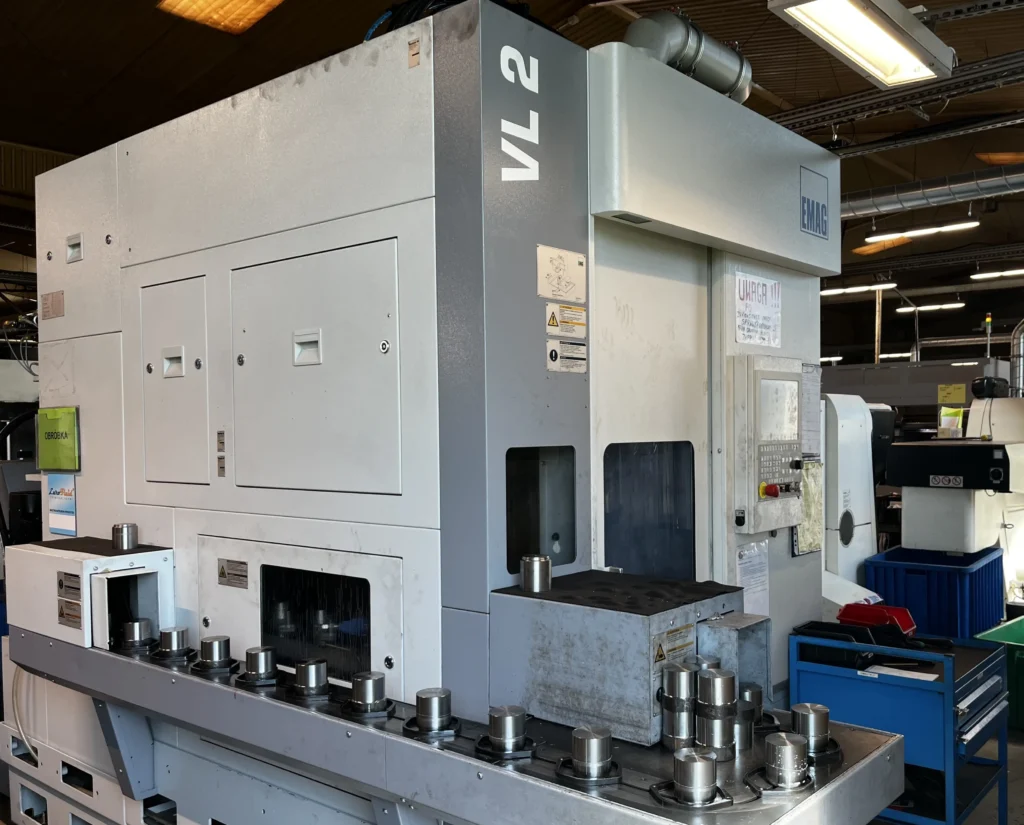
Czym jest EMAG VL2? EMAG VL2 to 3-osiowa pionowa tokarka CNC, która dzięki kompaktowej konstrukcji integruje najnowocześniejsze rozwiązania automatyzacyjne. Zaprojektowana z myślą o spełnieniu wysokich standardów produkcji precyzyjnych elementów mechanicznych, takich jak koła zębate, tuleje czy części pomp, tokarka EMAG VL2 stanowi odpowiedź na rosnące wymagania branży mechanicznej dotyczące precyzji i efektywności. Dzięki zastosowaniu najnowszych technologii i solidnej konstrukcji maszyna ta pozwala na obróbkę komponentów o maksymalnej średnicy do 100 mm i długości do 150 mm. Obrabiarka wyposażona jest w trzy osie przestrzenne oraz rewolwer na dwanaście miejsc narzędziowych z możliwością napędu narzędzi, co umożliwia wykonanie wielu rodzajów operacji obróbkowych bez konieczności ręcznej zmiany ustawienia detalu. Dodatkowa opcja osi Y zwiększa funkcjonalność obrabiarki, pozwalając na realizację bardziej skomplikowanych zadań obróbczych z zachowaniem wysokiej precyzji. Funkcjonowanie tokarki EMAG VL2 System automatycznego załadunku i rozładunku komponentów, działający na zasadzie „pick-up”, znacząco skraca czas cyklu obróbkowego, co jest kluczowe w kontekście produkcji masowej. Maszyna posiada konstrukcję z polimerobetonu MINERALIT®, która zapewnia wysoką stabilność oraz doskonałe właściwości tłumiące. Te cechy są fundamentalne dla zapewnienia najwyższej jakości obrabianych powierzchni oraz precyzji wykonania, stosowanie tej technologii przekłada się na dużą powtarzalność wytwarzanych detali. Korzyści z zastosowania EMAG VL2 w produkcji komponentów mechanicznych – studium przypadku SIM Gdynia Implementacja obrabiarki CNC EMAG VL2 w SIM Gdynia przyniosła znaczące korzyści dla procesów produkcyjnych, w tym zwiększenie precyzji obróbki i skrócenie czasów cykli produkcyjnych. Dzięki wydajnej automatyzacji oraz modularnej konstrukcji maszyna jest w stanie realizować produkcję dużych serii z cyklem obróbkowym trwającym zaledwie około jednej minuty. Pozwala to na wyprodukowanie znacznej ilości detali w ciągu trzech zmian pracy. Automatyzacja i modularność tokarki znacząco redukują również czas potrzebny na przestawienia i przygotowania jej do pracy. Podsumowanie Wyżej opisane technologie i materiał polimerobeton MINERALIT®, sprawiają, że EMAG VL2 jest niezbędnym narzędziem dla zakładów produkcyjnych o wysokich wymaganiach precyzyjności i szybkości działania, takich jak SIM Gdynia. Maszyna ta wprowadza znaczące usprawnienia w optymalizacji procesów produkcyjnych, czyniąc je szybszymi, tańszymi i bardziej precyzyjnymi.
Czyszczenie komponentów mechanicznych – Na czym polega czyszczenie ultradźwiękami w branży CNC?
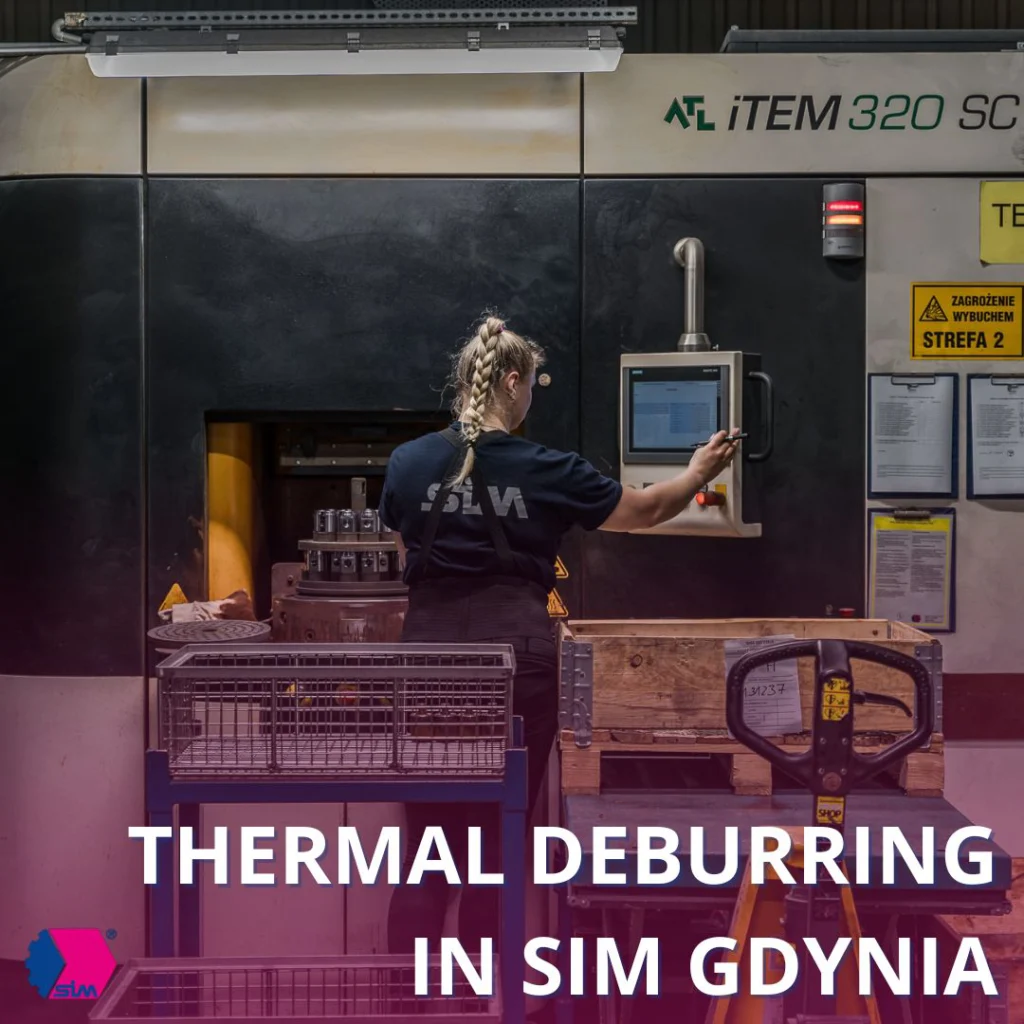
Czym jest mycie ultradźwiękowe? Mycie ultradźwiękowe to proces wykorzystujący fale akustyczne w zakresie ultradźwięków (20–40 kHz) do usuwania zanieczyszczeń z powierzchni metali i innych materiałów przemysłowych. Technika ta jest szczególnie ceniona w branży obróbki CNC (Computer Numerical Control), gdzie dokładność i czystość komponentów mają bezpośredni wpływ na jakość i tolerancje wymiarowe wyprodukowanych części. Jak przebiega proces mycia ultradźwiękowego? Proces mycia rozpoczyna się od zanurzenia czyszczonych elementów w zbiorniku z roztworem czyszczącym. Generowane fale ultradźwiękowe indukują zjawisko kawitacji, czyli tworzenie i implodowanie mikroskopijnych bąbelków w roztworze. Implodujące bąbelki generują fale uderzeniowe o wysokiej energii, które skutecznie usuwają nagromadzone zanieczyszczenia takie jak oleje, pasty, woski, osady i inne niepożądane elementy, docierając nawet do mikroskopijnych szczelin i zagięć. Jakie roztwory czyszczące stosuje się w myciu ultradźwiękowym? Roztwory stosowane w tej technologii zazwyczaj składają się z wody demineralizowanej, detergentów, środków chelatujących (np. EDTA) oraz inhibitorów korozji, które zapobiegają powstawaniu rdzy i korozji na metalowych powierzchniach podczas czyszczenia. Skład chemiczny roztworów jest precyzyjnie dobierany w zależności od rodzaju i natury czyszczonych materiałów. Zalety mycia ultradźwiękowego oraz jego efekty Mycie ultradźwiękowe oferuje precyzyjne usuwanie zanieczyszczeń z komponentów ze złożoną geometrią. Metoda ta jest bezpieczna dla czyszczonych materiałów, minimalizując ryzyko uszkodzeń mechanicznych i chemicznych, co jest istotne przy obróbce kosztownych lub delikatnych komponentów. Dodatkowo mycie ultradźwiękowe przyczynia się do redukcji odpadów chemicznych i zużycia wody, wspierając zrównoważone praktyki produkcyjne poprzez możliwość recyklingu i wielokrotnego użycia roztworów czyszczących. Case Study z SIM Gdynia: Jak ultradźwiękowe mycie komponentów mechanicznych wpłynęło na naszą produkcję W SIM Gdynia zastosowanie technologii ultradźwiękowego czyszczenia komponentów CNC pozwoliło nam osiągnąć znaczącą poprawę w standardach czystości i efektywności produkcyjnej. Dzięki tej metodzie, znacząco zredukowaliśmy liczbę odrzutów produkcyjnych i zwiększyliśmy ogólną satysfakcję klientów. Podsumowanie Mycie ultradźwiękowe to metoda wpływająca na poprawę efektywności operacyjnej i ekologicznej. W SIM Gdynia, technologia ta znacząco przyczyniła się do podniesienia jakości procesów produkcyjnych oraz do ochrony środowiska poprzez minimalizację odpadów chemicznych.