Normy usług spawalniczych w produkcji komponentów mechanicznych – Know-How z SIM Gdynia
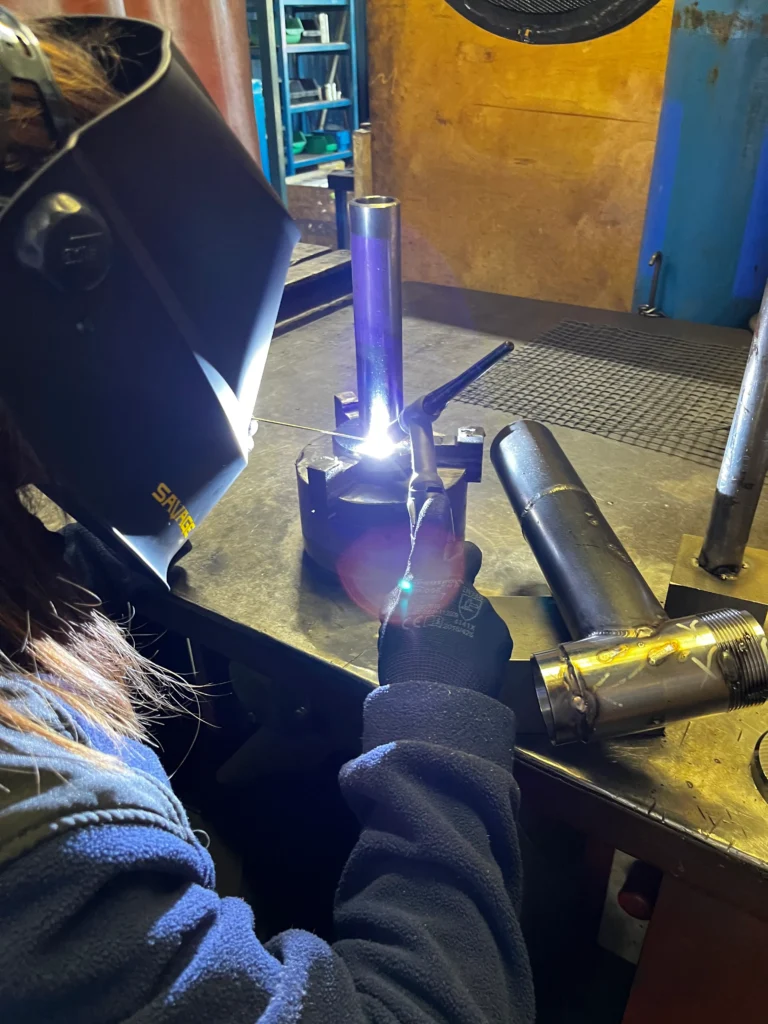
Wysoka jakość połączeń spawalniczych to kluczowy element w produkcji komponentów mechanicznych wykorzystywanych w różnych gałęziach przemysłu – od maszynowego i energetycznego, przez obronny, aż po motoryzacyjny, budowlany i wiele innych. Trwałość i wytrzymałość gotowych elementów zależą nie tylko od zastosowanych technologii, ale również od zgodności procesu spawalniczego z rygorystycznymi normami. W SIM Gdynia stosujemy sprawdzone procedury, które pozwalają na uzyskanie powtarzalnych i trwałych połączeń, spełniających najwyższe wymagania branżowe – niezależnie od sektora, w którym są wykorzystywane. Normy regulujące procesy spawalnicze Aby procesy spawalnicze były zgodne z wymaganiami technicznymi i spełniały określone kryteria wytrzymałościowe, konieczne jest stosowanie norm regulujących technologię łączenia metali, kwalifikacje spawaczy oraz metody kontroli jakości. W produkcji komponentów mechanicznych szczególne znaczenie mają: W SIM Gdynia przykładamy dużą wagę do przestrzegania powyższych norm, co pozwala na dostarczanie komponentów mechanicznych o wysokiej trwałości i zgodności z wymaganiami klientów. Nasze procesy są nadzorowane przez certyfikowanych specjalistów oraz podlegają systematycznej weryfikacji, aby każda spoina spełniała rygorystyczne standardy jakości. Technologie spawalnicze stosowane w produkcji komponentów mechanicznych Spawanie TIG (141) – precyzja i kontrola ciepła Spawanie metodą TIG (141) pozwala na uzyskanie spoin o wysokiej jakości i precyzji. Dzięki zastosowaniu elektrody wolframowej oraz gazu osłonowego proces ten minimalizuje wpływ ciepła na strukturę materiału. Technologia ta umożliwia uzyskanie czystych i estetycznych spoin, co jest kluczowe w przypadku elementów o podwyższonych wymaganiach antykorozyjnych. Spawanie MIG/MAG (135/136) – trwałość i wydajność Spawanie metodą MIG/MAG (135/136) znajduje zastosowanie w łączeniu stali niskostopowej, gdzie kluczowa jest wytrzymałość połączenia oraz odporność na obciążenia dynamiczne. Proces ten umożliwia uzyskanie trwałych spoin przy jednoczesnym zachowaniu wysokiej efektywności produkcji. Materiały stosowane w procesie spawania W produkcji komponentów mechanicznych kluczowe jest zastosowanie odpowiednich materiałów, które muszą spełniać wymagania dotyczące wytrzymałości mechanicznej, odporności na czynniki zewnętrzne oraz zgodności z dokumentacją techniczną.W SIM Gdynia spawamy zarówno stal nierdzewną, wymagającą precyzyjnej kontroli parametrów cieplnych, aby uniknąć przegrzania i zmian strukturalnych, jak i stal niskostopową, stosowaną w konstrukcjach maszynowych i elementach poddawanych intensywnym obciążeniom mechanicznym. Podsumowanie Profesjonalne usługi spawalnicze w produkcji komponentów mechanicznych muszą spełniać rygorystyczne wymagania norm EN ISO 15614-1, ISO 9606-1 oraz EN ISO 9712, aby zapewnić trwałość i precyzję wykonania połączeń. W SIM Gdynia dbamy o to, aby każdy proces był realizowany zgodnie z najwyższymi standardami, co pozwala nam na dostarczanie komponentów spełniających oczekiwania klientów z wielu sektorów przemysłu. Dzięki zastosowaniu certyfikowanych procedur jesteśmy w stanie realizować zarówno pojedyncze projekty, jak i większe serie. Stała kontrola jakości oraz nadzór doświadczonego zespołu gwarantują, że każda spoina jest wykonana z najwyższą precyzją i zgodnie z dokumentacją techniczną.
SIM Gdynia laureatem OTIF95 Supplier Performance Award od KION Group
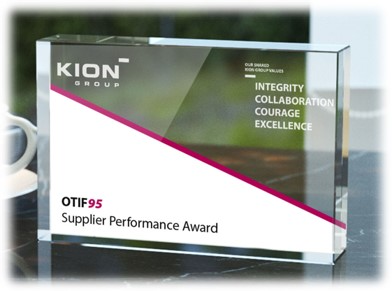
Z dumą informujemy, że SIM Gdynia została laureatem nagrody OTIF95 SupplierPerformance Award, przyznawanej przez KION Group za terminowość i kompletnośćdostaw w 2024 roku.Nagroda OTIF95 jest przyznawana dostawcom, którzy konsekwentnie realizują zamówieniazgodnie z ustalonym harmonogramem i w pełnym zakresie ilościowym. Uzyskanie tegotytułu jest wynikiem naszej skutecznej organizacji procesów produkcyjnych,precyzyjnego planowania logistyki oraz zaangażowania zespołu SIM Gdynia wutrzymanie najwyższej jakości usług. Współpraca SIM Gdynia z KION Group KION Group to światowy lider w dziedzinie automatyzacji logistyki, integrujący nowoczesnesystemy transportowe, magazynowe oraz oprogramowanie sterujące przepływem towarów.W ramach naszej współpracy dostarczamy wysokiej jakości komponenty mechaniczne,które stanowią kluczowy element systemów wykorzystywanych w nowoczesnych centrachdystrybucyjnych. Precyzja wykonania, terminowość oraz elastyczność w realizacjizamówień sprawiają, że nasze rozwiązania w pełni odpowiadają na wymagania branżyintralogistycznej.Uzyskanie statusu top performer w programie OTIF95 potwierdza, że nasze procesyspełniają najwyższe standardy w zakresie niezawodności dostaw, co przekłada się nastabilność łańcucha dostaw KION Group oraz ich klientów na całym świecie. Podziękowania i zobowiązanie na przyszłość Dziękujemy zespołowi KION Group za wyróżnienie oraz naszym pracownikom za ichzaangażowanie i konsekwencję w dążeniu do doskonałości operacyjnej. To właśnie dziękiwspólnemu wysiłkowi SIM Gdynia znalazło się w gronie najlepszych dostawców KION. Nagroda OTIF95 to dla nas nie tylko powód do dumy, ale także zobowiązanie do dalszegodoskonalenia procesów, aby utrzymać najwyższy poziom usług i spełniać oczekiwanianaszych partnerów. Nie zwalniamy tempa – kontynuujemy pracę nad utrzymaniem idalszym podnoszeniem standardów dostaw.
Obróbka CNC obręczy, kół zębatych i innych wielkogabarytowych oraz skomplikowanych detali.
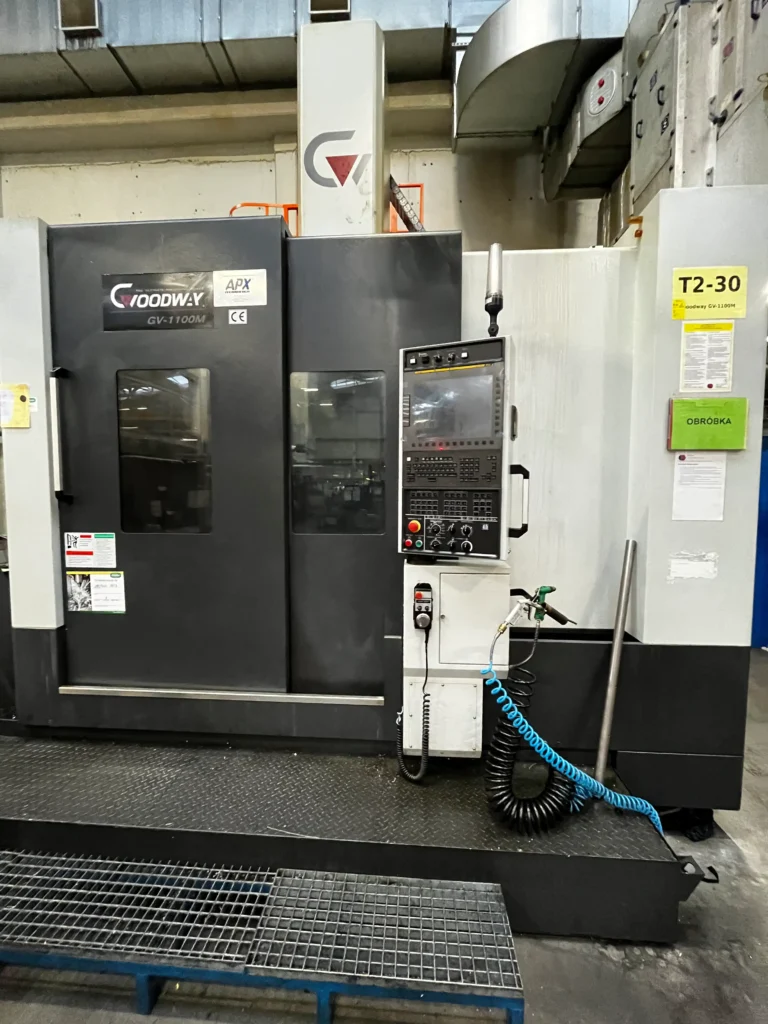
Wielkogabarytowe elementy, takie jak duże obręcze, tarcze czy koła zębate, stawiają przed technologami oraz operatorami maszyn szczególne wymagania. Skrawanie dużych powierzchni o stosunkowo niewielkiej szerokości bywa problematyczne ze względu na naprężenia, które mogą prowadzić do niepożądanych odkształceń i trudności w osiągnięciu stabilności detalu. Odpowiednia obróbka cnc z zastosowaniem właściwej obrabiarki pozwala jednak zoptymalizować ten proces, zagwarantować wysoką powtarzalność wymiarową i zminimalizować ryzyko błędów. Wyzwania przy skrawaniu CNC elementów wielkogabarytowych. Obręcze o dużej średnicy, a zarazem małej szerokości, wymagają precyzyjnego mocowania oraz wyważenia, aby uniknąć drgań podczas pracy. Obróbka skrawaniem przy pomocy odpowiednich tokarek CNC pozwala realizować te zadania efektywnie, a jednocześnie utrzymywać stabilne parametry w toku kolejnych serii produkcyjnych. Tokarka CNC do wielkogabarytowych detali – geneza inwestycji SIM Gdynia. W 2021 roku podjęliśmy decyzję o rozszerzeniu możliwości technologicznych naszego przedsiębiorstwa poprzez zakup tokarki CNC, która sprosta wymaganiom obróbki dużych formatów. Obrabiarka miała umożliwić skrawanie elementów o średnicy przekraczającej 1 metr o wadze kilku ton. Takie parametry okazały się niezbędne w produkcji wielkogabarytowych elementów stosowanych w branżach hydraulicznych, wydobywczych oraz innych z obszaru przemysłu ciężkiego. Charakterystyka i specyfikacja obrabiarki CNC GV-1100. Zakupiona tokarka model GV-1100 została wyposażona w stół o średnicy 900 mm, co pozwala na obróbkę elementów o max. średnicy do 1,100 mm. Obrabiarka jest w stanie obsłużyć detale o masie do 4,000kg co w zupełności wystarcza do obróbki elementów o znacznych gabarytach. Sercem urządzenia jest wrzeciono z dwiema przekładniami, oferujące prędkość w zakresie od 1 do 500 obr./min i moment obrotowy do 10,170 Nm. Napęd główny o mocy 37 kW (kontynuacja) / 45 kW (30 min) gwarantuje płynną pracę, nawet podczas intensywnego usuwania naddatków materiałowych. Dodatkową zaletą jest obecność osi C (motor output 3 kW), z którą można wykonywać bardziej złożone operacje, na przykład frezowanie zarysów na obrabianym przedmiocie. Tokarka dysponuje osią X pozwalającą na przesuw do 1,300 mm (w zakresie -100 ~ 1,200 mm) oraz osią Z o skoku 900 mm. W zależności od potrzeb możliwe jest także wykorzystanie osi W, która dysponuje skokiem do 600 mm. Silniki serwo o mocach 7 kW (oś X) i 9 kW (oś Z) zapewniają odpowiednią dynamikę i precyzję ruchów, a prędkość posuwów dochodzi do 12 m/min w osi X oraz 10 m/min w osi Z. Urządzenie wyposażono w magazyn narzędzi o pojemności 12 sztuk (taper BT-50), co ułatwia przeprowadzanie procesów obróbki bez konieczności częstych ręcznych zmian narzędzi. Maksymalny ciężar narzędzia sięga 50 kg, co pozwala stosować solidne głowice do skrawania. Całość jest sterowana układem FANUC Oi-TF Plus, zapewniającym wysoką powtarzalność i dokładność pozycjonowania, które w przypadku osi X i Z wynoszą ±0,007 mm na 500 mm. Proces obróbki – etapy działania. Przygotowanie detalu do obróbki cnc wymaga w pierwszej kolejności odpowiedniego zamocowania oraz ustalenia bazy. Następnie operator dobiera optymalne parametry skrawania, biorąc pod uwagę wymiary, kształt i materiał elementu oraz planowaną liczbę cykli. Ze względu na duże rozmiary przedmiotu konieczne bywa stopniowe zwiększanie prędkości wrzeciona czy posuwu, tak aby zredukować ryzyko wibracji. Na ostatnim etapie przeprowadza się kontrolę jakości, obejmującą weryfikację wymiarów, tolerancji kształtu i oceny powierzchni. Podsumowanie. Skrawanie wielkogabarytowych elementów wymaga specjalistycznych maszyn zapewniających moc, stabilność i odpowiedni zakres pracy. Tokarka GV-1100 kupiona w 2021 roku umożliwia obróbkę elementów o średnicy do 1,100 mm i udźwigu do 4,000 kg, co znacznie poszerzyło możliwości skrawania w SIM Gdynia.
Obróbka CNC wałków i detali – rola szlifierek w osiąganiu idealnej współosiowości.
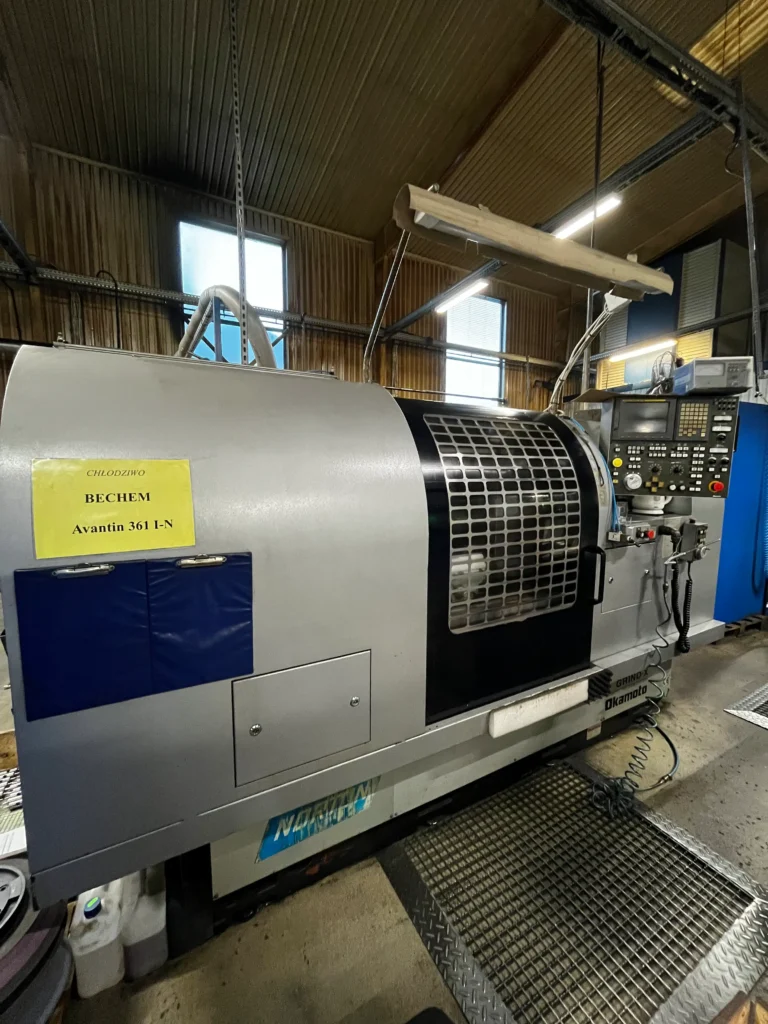
Obróbka CNC wałków i detali wymaga zachowania wysokiej dokładności wymiarowej oraz odpowiednich tolerancji geometrycznych. Szczególnie ważna jest współosiowość, od której zależy płynna i bezawaryjna praca elementów obrotowych. W osiąganiu pożądanych efektów kluczową rolę odgrywa szlifowanie metali, dzięki któremu można uzyskać idealnie gładkie powierzchnie oraz ograniczyć bicie promieniowe i całkowite. Znaczenie współosiowości w obróbce CNC. Współosiowość to parametr określający, czy oś obrotu detalu pokrywa się z osią układu odniesienia na całej długości. Nawet nieznaczne odchylenia mogą prowadzić do zwiększonych drgań, szybszego zużycia łożysk, kłopotów w trakcie montażu czy zakłóceń w pracy całego układu. W przypadku wałków służących do przenoszenia mocy albo pełniących funkcję elementów łożyskowanych istotne jest, by bicie promieniowe i bicie całkowite utrzymywać w ściśle określonych granicach. Precyzyjne szlifowanie metalu pozwala na kontrolowanie tego aspektu z dokładnością nawet do setnych czy tysięcznych części milimetra. Rola szlifowania metalu w uzyskaniu idealnych tolerancji. Szlifowanie metali w procesie obróbki CNC pełni funkcję wykończeniową, zapewniając odpowiednie właściwości powierzchni oraz kształtu. Dzięki temu zmniejsza się chropowatość, a sama obróbka trwa krócej w porównaniu z tradycyjnymi metodami, gdyż sterowanie numeryczne umożliwia powtarzalne, ściśle kontrolowane ruchy narzędzia. Szlifierka Okamoto serii 300 (model 350) – charakterystyka naszej obrabiarki CNC. Jako przykład urządzenia sprawdzającego się w precyzyjnej obróbce można przytoczyć szlifierkę Okamoto z serii 300 w modelu 350, która umożliwia obróbkę detali o średnicy sięgającej 350 mm. Konstrukcja maszyny pozwala na utrzymanie detalu o długości do około 1300 mm między kłami, co daje szeroki zakres zastosowań. Dzięki wrzecionu o zakresie prędkości od 10 do 500 obr./min możliwe jest dostosowanie parametrów pracy do rodzaju materiału i założonego celu obróbki — od precyzyjnego wykończenia po sprawne usuwanie naddatków. Minimalny zadawany posuw rzędu 0,001 mm zapewnia wysoką kontrolę nad chropowatością i zachowaniem wymaganych tolerancji. Solidna konstrukcja ogranicza drgania, przekładając się na lepszą stabilność procesu. Wpływa to również na zmniejszenie bicia promieniowego i bicia całkowitego oraz umożliwia uzyskanie idealnej współosiowości. Wydajne układy chłodzenia i separacji zanieczyszczeń pozwalają podtrzymywać niezmienne warunki podczas obróbki, dzięki czemu rezultaty pozostają powtarzalne. Podsumowanie. W obróbce CNC wałków i innych elementów obrotowych istotne jest dążenie do zachowania ścisłych tolerancji oraz współosiowości. Szlifowanie metalu, zwłaszcza szlifowanie powierzchni metalowych z użyciem maszyn sterowanych numerycznie, gwarantuje precyzję kluczową w branżach, w których nawet mikrometrowe odstępstwa mogą nieść poważne konsekwencje. Szlifierki takie jak Okamoto 350 umożliwiają pracę z szerokim zakresem detali, zapewniając przy tym wysoki poziom kontroli nad procesem, stabilność warunków i niewielką chropowatość powierzchni. W efekcie gotowe produkty charakteryzują się znakomitymi walorami użytkowymi: są odporne na drgania, wolniej się zużywają i rzadziej wymagają ingerencji serwisowej. W SIM Gdynia wyżej omówione podejście wpływa na zadowolenie naszych klientów oraz długoterminową współpracę opartą na jakości i zaufaniu. Jeżeli szukają Państwo zaufanego wykonawcy komponentów mechanicznych, zapraszamy serdecznie do wypełnienia naszego formularza kontaktowego: https://www.simgdynia.eu/kontakt/
Życzenia świąteczne i podsumowanie roku 2024
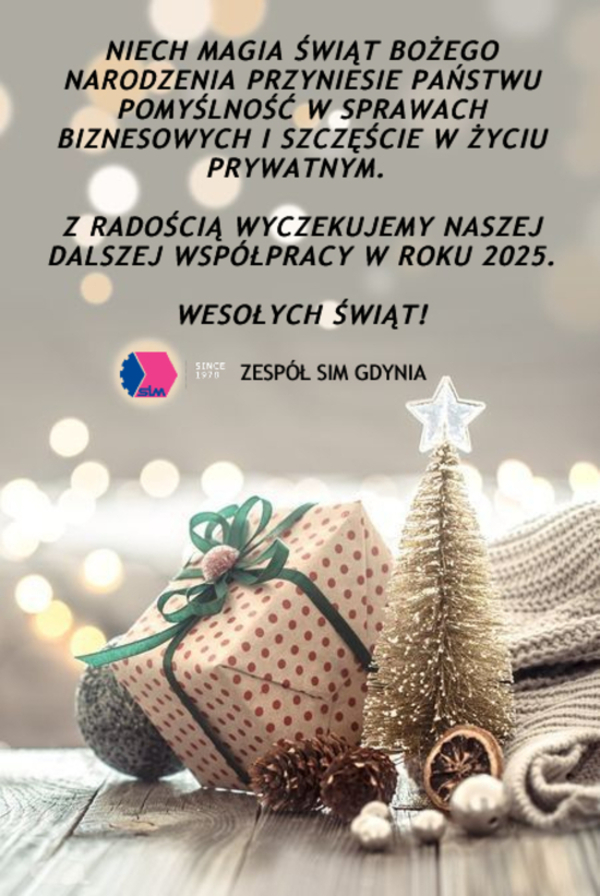
Z okazji zbliżających się Świąt Bożego Narodzenia oraz Nowego Roku pragniemy serdecznie podziękować naszym pracownikom, partnerom biznesowym, współpracownikom i klientom za wsparcie, zaufanie oraz owocną współpracę w mijającym roku. 2024 był dla SIM Gdynia okresem intensywnego rozwoju, szczególnie w obszarze sektora obronnego, gdzie nie tylko rozszerzyliśmy naszą działalność, ale również nawiązaliśmy kluczowe, strategiczne partnerstwa. Najważniejsze wydarzenia w SIM Gdynia w 2024 roku MSPO 2024 Nasza obecność na Międzynarodowym Salonie Przemysłu Obronnego (MSPO) 2024 była jednym z najważniejszych wydarzeń w tym roku. Targi te stanowiły doskonałą okazję, by zaprezentować nasze możliwości w produkcji precyzyjnych komponentów mechanicznych dla sektora obronnego. Dzięki licznym spotkaniom i rozmowom mieliśmy szansę nawiązać nowe kontakty biznesowe oraz rozważyć potencjalne projekty z wykorzystaniem naszych technologii w zaawansowanych systemach obronnych. Enforce Tac 2024 Enforce Tac 2024 to kolejne istotne wydarzenie w naszym kalendarzu. Targi zgromadziły ponad 12 tysięcy ekspertów z całego świata, co stworzyło wyjątkową platformę do wymiany wiedzy i doświadczeń. Zaprezentowano tam najnowsze technologie związane z obronnością, w tym systemy wizyjne, autonomiczne pojazdy oraz rozwiązania z zakresu uzbrojenia. Udział SIM Gdynia pozwolił nam lepiej zrozumieć przyszłe potrzeby branży, a także zaprezentować nasze rozwiązania w obszarach takich jak produkcja komponentów do dronów, systemów uzbrojenia oraz osłon i obudów do urządzeń elektronicznych. Wyróżnienie Forbes Forum Firm Rodzinnych W 2024 roku mieliśmy zaszczyt znaleźć się w prestiżowym rankingu Forbes Forum Firm Rodzinnych 2024. To wyróżnienie jest dla nas niezwykle cenne, ponieważ podkreśla naszą stabilność finansową, konsekwentny rozwój oraz wkład w gospodarkę regionalną. To osiągnięcie nie byłoby możliwe bez zaangażowania naszego zespołu oraz zaufania, którym obdarzają nas partnerzy i klienci. Nagroda stanowi dla nas motywację do dalszego udoskonalania procesów oraz wprowadzania nowych technologii, by umacniać pozycję firmy na rynkach krajowych i zagranicznych. Podziękowania i życzenia od zespołu SIM Gdynia Z okazji Świąt Bożego Narodzenia życzymy Państwu wielu radosnych chwil w gronie najbliższych, przepełnionych spokojem i ciepłem. Niech Nowy Rok 2025 przyniesie zdrowie, sukcesy oraz realizację zawodowych i osobistych marzeń. Dziękujemy za dotychczasowe zaufanie i współpracę. Z nadzieją patrzymy na kolejny rok, licząc na kontynuację wspólnych projektów oraz dalszy rozwój naszych relacji. Wesołych Świąt i pomyślności w Nowym Roku życzy zespół SIM Gdynia!
Jak mierzyć detale w obróbce CNC? Metody pomiaru i ich zastosowanie
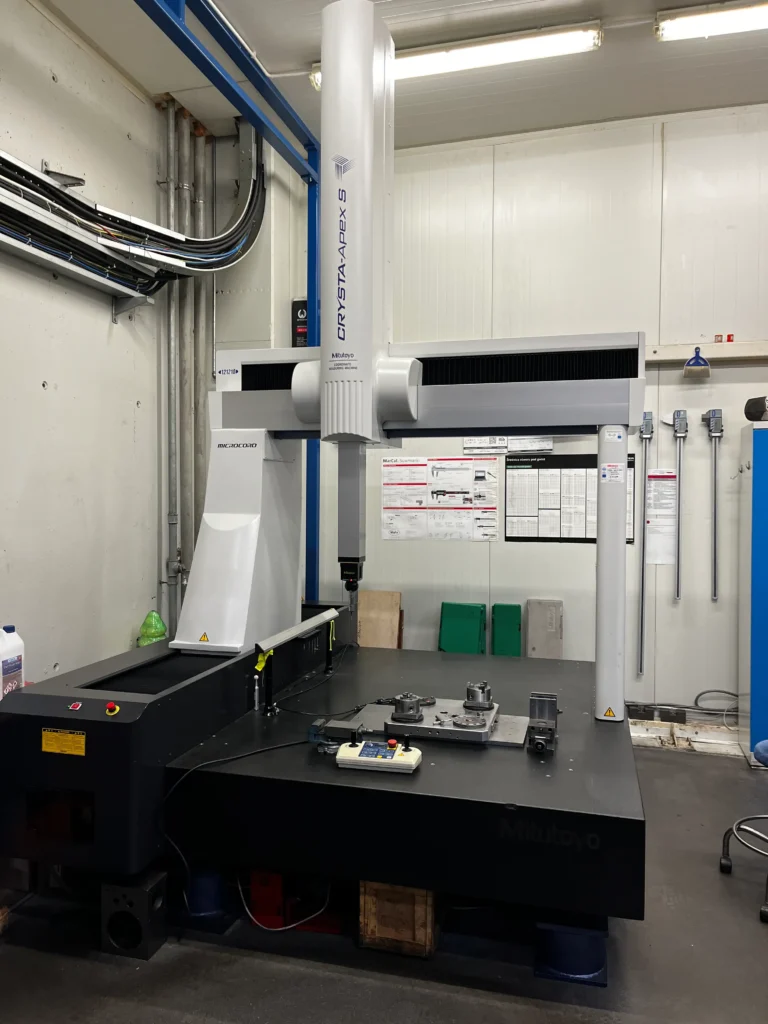
Precyzyjne pomiary odgrywają kluczową rolę w procesach obróbki CNC, takich jak frezowanie, toczenie czy wiercenie. Głównym celem jest zapewnienie zgodności wymiarów detali z wymaganiami technicznymi oraz utrzymanie wysokiej jakości produkcji. Dokładność wymiarowa bezpośrednio wpływa na funkcjonalność i trwałość końcowych produktów, dlatego niezbędna jest ciągła kontrola parametrów obróbki, szczególnie w seryjnej produkcji, gdzie powtarzalność jest priorytetem. Pomiary umożliwiają także szybkie wykrywanie i korektę odchyłek, co minimalizuje straty materiałowe. W zaawansowanych procesach produkcyjnych, takich jak te stosowane w SIM Gdynia, pomiary stanowią integralną część zapewnienia jakości. Tradycyjne metody pomiarowe Tradycyjne narzędzia pomiarowe, takie jak suwmiarki i mikrometry, od dziesięcioleci są podstawą kontroli wymiarów w obróbce CNC. Suwmiarki umożliwiają pomiar długości, średnic i głębokości z dokładnością wynoszącą około 0,02 mm, co czyni je wszechstronnymi narzędziami. Mikrometry z kolei oferują dokładność do 0.001 mm, dzięki czemu nadają się do pomiarów detali wymagających większej precyzji, takich jak wałki czy tuleje. Pomimo swojej uniwersalności, tradycyjne narzędzia mają ograniczenia. Pomiary skomplikowanych kształtów lub detali o złożonej geometrii mogą być czasochłonne i obarczone większym ryzykiem błędów. W takich przypadkach konieczne staje się wykorzystanie bardziej zaawansowanych technologii, które pozwalają na automatyzację procesu pomiarowego i uzyskanie większej dokładności. Nowoczesne rozwiązania – współrzędnościowe maszyny pomiarowe Współrzędnościowe maszyny pomiarowe (CMM) reprezentują najnowocześniejsze podejście do kontroli wymiarowej w obróbce CNC. Umożliwiają one precyzyjne pomiary detali w trzech osiach (X, Y, Z) za pomocą sond stykowych lub bezstykowych. Maszyny pomiarowe takie jak Mitutoyo, oferują możliwość pomiaru skomplikowanych geometrii z dokładnością sięgającą mikronów. Maszyna działa na zasadzie zbierania punktów z powierzchni detalu, przesuwając się wzdłuż wcześniej zaprogramowanych trajektorii. Program pomiarowy dla każdego detalu tworzony jest jednorazowo, co gwarantuje powtarzalność i standaryzację procesu przy późniejszych pomiarach. W SIM Gdynia korzystamy z takich rozwiązań w celu uzyskania szczegółowej analizy wymiarowej elementów o złożonych kształtach, co pozwala nam utrzymać wysokie standardy jakości. Konstrukcja maszyny pomiarowej umożliwia pomiar detali o dużych gabarytach, takich jak części maszynowe czy elementy stosowane w lotnictwie. Dzięki automatyzacji procesu pomiarowego można zminimalizować wpływ błędu ludzkiego oraz zwiększyć szybkość analizy wymiarowej. Skanery 3D i czujniki laserowe w pomiarach CNC Obecnie przemysł coraz częściej korzysta z technologii bezkontaktowych, takich jak skanery 3D czy czujniki laserowe. Skanery pozwalają na kompleksowe odwzorowanie geometrii detalu, co jest szczególnie przydatne w przypadku elementów o nieregularnych kształtach. Technologia ta umożliwia tworzenie modeli 3D, które mogą być wykorzystane do porównania z danymi CAD oraz do dalszej analizy. Czujniki optyczne i laserowe oferują precyzję i szybkość, co czyni je idealnymi do pomiarów w czasie rzeczywistym, szczególnie w seryjnej produkcji. Ich zastosowanie minimalizuje ryzyko uszkodzenia detalu, co jest istotne w przypadku materiałów delikatnych lub podatnych na deformacje. Jak dobierać odpowiednie metody pomiarowe? Wybór odpowiedniego narzędzia pomiarowego zależy od kilku czynników, takich jak tolerancje wymiarowe, geometria detalu oraz wymagania dotyczące jakości powierzchni. W przypadku prostych detali o mniej rygorystycznych tolerancjach tradycyjne narzędzia, takie jak suwmiarki czy mikrometry, mogą być wystarczające. Natomiast dla bardziej skomplikowanych detali, które wymagają analizy w wielu płaszczyznach, najlepszym rozwiązaniem są współrzędnościowe maszyny pomiarowe lub skanery 3D. W SIM Gdynia stosujemy zróżnicowane podejście do pomiarów, dostosowując metody do specyfiki projektu. Dzięki temu jesteśmy w stanie zapewnić precyzję zarówno w produkcji jednostkowej, jak i seryjnej. Podsumowanie Pomiary w obróbce CNC to fundament precyzyjnej i efektywnej produkcji. Od tradycyjnych narzędzi, takich jak suwmiarki i mikrometry, po zaawansowane maszyny współrzędnościowe i skanery 3D – każda technologia ma swoje miejsce w zależności od specyfiki projektu. W SIM Gdynia nieustannie rozwijamy nasze możliwości pomiarowe, korzystając z najnowszych technologii, aby dostarczać produkty spełniające najbardziej rygorystyczne normy techniczne. Dzięki temu możemy oferować naszym klientom niezawodność, powtarzalność i najwyższą jakość na każdym etapie realizacji zamówienia.
Szlifierki bezkłowe – klucz do precyzyjnego szlifowania w nowoczesnym przemyśle
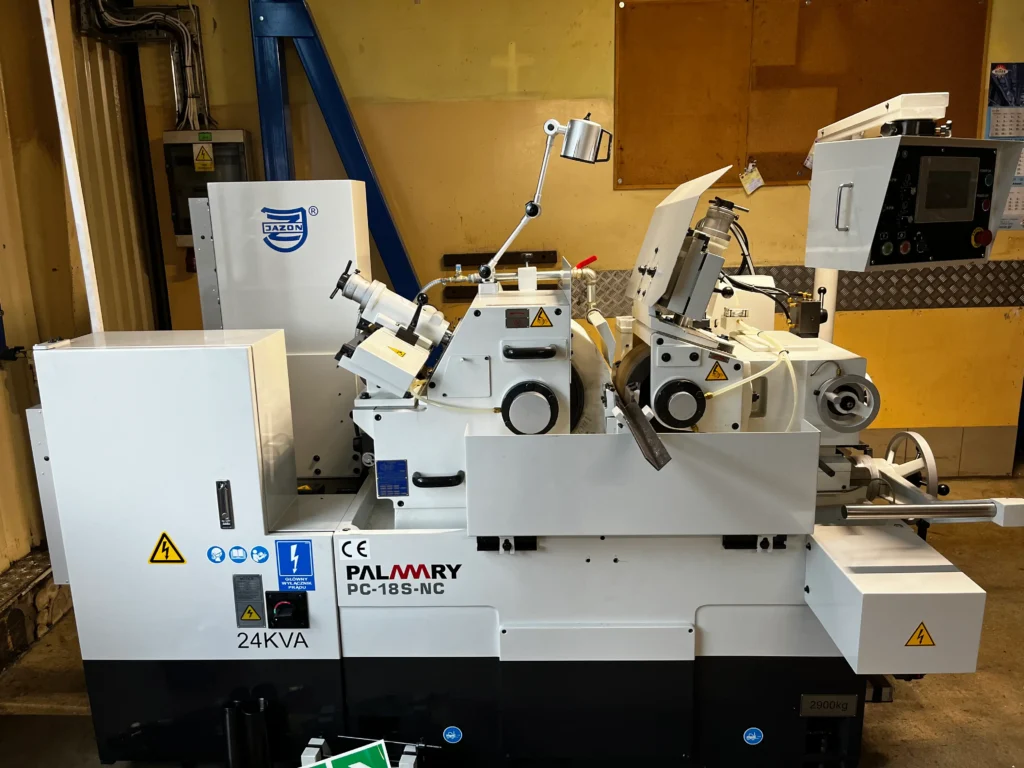
Czym są szlifierki bezkłowe i dlaczego są istotne? Szlifierki bezkłowe to specjalistyczne maszyny przeznaczone do precyzyjnego szlifowania elementów o prostych kształtach, takich jak wałki czy tuleje. Unikalną cechą tych urządzeń jest brak klasycznego podparcia obrabianego przedmiotu, co oznacza, że materiał nie jest zamocowany w jednym punkcie, jak ma to miejsce w tradycyjnych szlifierkach. Element obrabiany porusza się swobodnie wzdłuż tarczy ściernej, która jednocześnie obraca się w przeciwnym kierunku. Takie rozwiązanie pozwala wyeliminować tzw. „kłówki” – nierówności powierzchniowe, które są częstym problemem w tradycyjnych procesach szlifowania. Dzięki tej technologii możliwe jest osiągnięcie wysokiej jakości powierzchni, co ma kluczowe znaczenie w przypadku detali wymagających wyjątkowej dokładności wymiarowej oraz odpowiednich parametrów wykończeniowych. Zasada działania szlifierek bezkłowych W procesie szlifowania bezkłowego kluczową rolę odgrywa kontrola parametrów takich jak prędkość obrotowa, siła nacisku oraz szybkość przesuwu detalu. Element obrabiany jest swobodnie podtrzymywany między dwiema tarczami: jedną obracającą się z wysoką prędkością a drugą odpowiedzialną za stabilne przesuwanie. Taki układ eliminuje konieczność stosowania punktów podparcia, co redukuje ryzyko powstawania uszkodzeń powierzchniowych. Aby zachować wysoką jakość procesu, stosuje się również systemy chłodzenia, które redukują tarcie i minimalizują ryzyko przegrzewania się materiału. Dzięki temu elementy zachowują stabilność wymiarową i odpowiednie parametry techniczne, nawet przy obróbce detali wymagających ścisłych tolerancji. Rodzaje szlifierek bezkłowych i ich zastosowanie Szlifierki bezkłowe można podzielić na kilka typów w zależności od ich zastosowania i konstrukcji: Jak szlifierki bezkłowe wspierają produkcję w SIM Gdynia? W SIM Gdynia wdrożyliśmy technologię szlifowania bezkłowego, aby sprostać wymaganiom produkcji elementów o wysokiej precyzji. Dzięki zastosowaniu tych maszyn znacząco poprawiliśmy efektywność procesów obróbczych, co pozwala nam realizować zlecenia w krótszym czasie przy zachowaniu najwyższej jakości. Jednym z głównych efektów jest uzyskanie gładkości powierzchni, co jest kluczowe w przypadku elementów stosowanych w dynamicznych układach, takich jak pierścienie uszczelniające czy komponenty maszyn. Ponadto, skrócenie cyklu obróbki oraz redukcja strat materiałowych przekładają się na optymalizację kosztów produkcji. Dzięki szlifierkom bezkłowym jesteśmy w stanie oferować naszym klientom produkty spełniające najbardziej rygorystyczne normy techniczne. Podsumowanie Szlifierki bezkłowe stanowią istotny element nowoczesnej obróbki skrawaniem, umożliwiając precyzyjną i efektywną produkcję elementów cylindrycznych oraz detali o nieregularnych kształtach. Ich zastosowanie pozwala osiągnąć wysoką jakość wykończenia powierzchni, eliminując problemy związane z tradycyjnymi metodami szlifowania. W SIM Gdynia wykorzystujemy tę technologię, aby realizować zlecenia na najwyższym poziomie technicznym, przy jednoczesnej optymalizacji czasu i kosztów produkcji. Dzięki temu możemy skutecznie wspierać naszych klientów w realizacji ich celów przemysłowych.
Frezarka obwiedniowa CNC – klucz do precyzyjnego nacinania kół zębatych
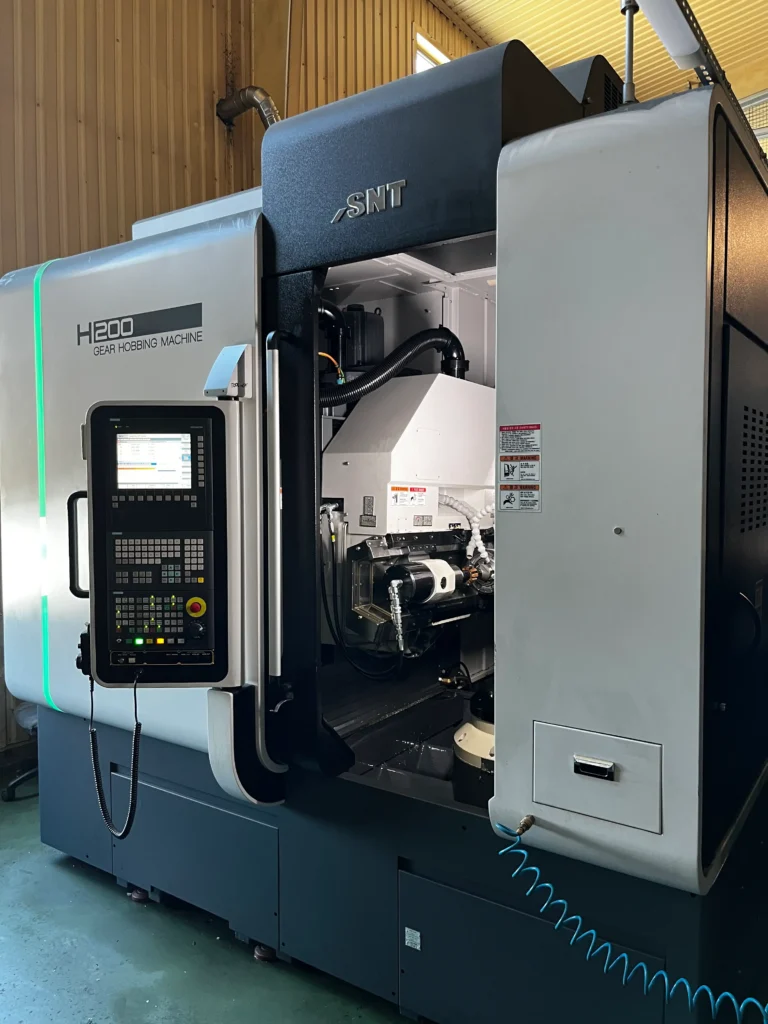
Czym są frezarki obwiedniowe CNC? Frezarki obwiedniowe CNC to maszyny specjalistyczne, wykorzystywane w obróbce skrawaniem, przeznaczone do produkcji kół zębatych o obwiedniowym profilu zębów. Dzięki zastosowaniu technologii sterowania numerycznego umożliwiają precyzyjne odwzorowanie kształtu zębów zgodnie z rygorystycznymi normami wymiarowymi. Urządzenia te znajdują zastosowanie w produkcji komponentów wymagających wysokiej dokładności, takich jak elementy układów napędowych stosowane w motoryzacji, lotnictwie czy przemyśle maszynowym. Jak działają frezarki obwiedniowe CNC? Frezarka obwiedniowa CNC umożliwia obróbkę kół zębatych poprzez precyzyjne sterowanie trajektorią narzędzia skrawającego, co pozwala na dokładne odwzorowanie kształtu zębów. Proces ten odbywa się na kilku osiach roboczych, które działają jednocześnie, umożliwiając wielokierunkowe ruchy narzędzia. Dzięki programowaniu w systemie CNC możliwe jest zaplanowanie każdego kroku obróbki z dużą dokładnością. Taka organizacja pracy minimalizuje ryzyko błędów oraz zapewnia powtarzalność produkcji. W efekcie można uzyskać koła zębate spełniające wymagania norm jakościowych. Wyzwania w procesie nacinania kół zębatych Proces nacinania kół zębatych wiąże się z koniecznością zachowania bardzo ścisłych tolerancji wymiarowych. Nawet niewielkie odchylenia w kształcie lub wymiarach zębów mogą wpłynąć na funkcjonowanie mechanizmu, w którym są one wykorzystywane. Istotnym elementem procesu jest geometria narzędzia skrawającego – freza obwiedniowego – oraz jego odpowiednie ustawienie. Precyzyjne dostosowanie parametrów takich jak prędkość obrotowa, prędkość posuwu czy kąt ustawienia narzędzia jest kluczowe dla uzyskania wysokiej jakości wyrobu. Frezarka obwiedniowa S&T Dynamics H200 w SIM Gdynia W 2022 roku rozszerzyliśmy nasz park maszynowy o frezarkę obwiedniową CNC S&T Dynamics H200. Urządzenie pozwala nam na obróbkę komponentów o średnicy do 200 mm, co znacznie zwiększa nasze możliwości produkcyjne w zakresie kół zębatych. Maszyna wyposażona jest w bezpośredni napęd silnika momentu obrotowego, który eliminuje luzy mechaniczne i umożliwia osiągnięcie wysokiej precyzji podczas obróbki. Proces nacinania zębów na niektórych elementach trwa zaledwie 4 minuty, co znacząco skraca czas realizacji zleceń w porównaniu z tradycyjnymi metodami. Frezarka S&T Dynamics H200 pracuje z prędkością obrotową stołu roboczego do 230 obr./min i osiąga szybkość posuwu na osiach X i Z wynoszącą 12 m/min. Te parametry techniczne pozwalają nam realizować obróbkę o wysokich wymaganiach w zakresie dokładności i wydajności. Technologia półsuchej obróbki w naszym procesie skrawania W naszej pracy wykorzystujemy system MQL (Minimal Quantity Lubrication), który pozwala na redukcję zużycia środków smarujących. Technologia półsuchej obróbki stosowana we frezarce H200 nie tylko obniża koszty produkcji, ale również zmniejsza wpływ procesu na środowisko. Dzięki zastosowaniu MQL proces obróbki jest bardziej efektywny, a narzędzia skrawające charakteryzują się wydłużoną żywotnością. To podejście pozwala nam optymalizować produkcję bez kompromisów w zakresie jakości wykonania. Podsumowanie Frezarki obwiedniowe CNC stanowią podstawę procesu produkcji kół zębatych o wysokiej precyzji. Wprowadzenie frezarki S&T Dynamics H200 do naszego parku maszynowego umożliwiło zwiększenie efektywności realizowanych zleceń, a także zagwarantowanie jakości wymaganej w nowoczesnych aplikacjach technicznych. Dzięki ciągłemu rozwijaniu naszych możliwości produkcyjnych jesteśmy gotowi sprostać wymaganiom najbardziej wymagających branż, takich jak motoryzacja, lotnictwo czy przemysł maszynowy.
Robodrill α-D21LiB5 Plus – precyzyjna obróbka CNC dla wymagających zleceń produkcyjnych
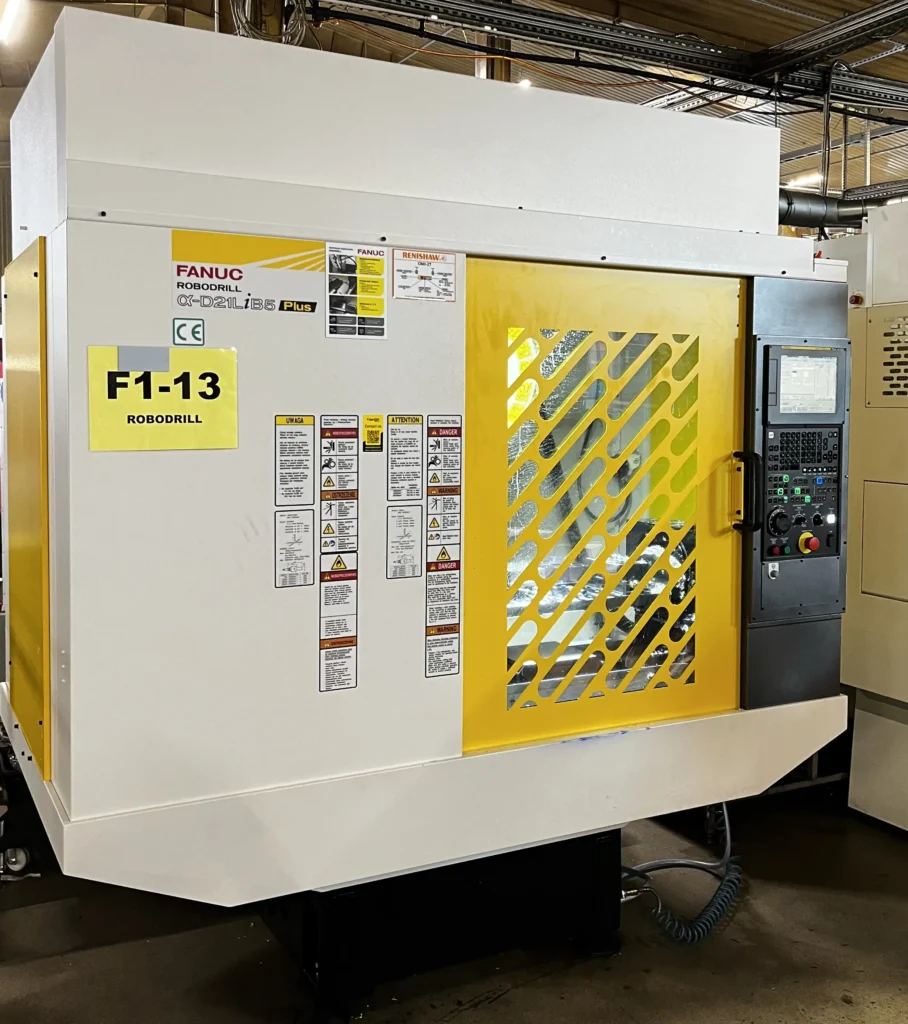
Od ponad 45 lat w SIM Gdynia rozwijamy nasz park maszynowy, aby oferować obróbkę CNC zgodną z najwyższymi wymaganiami technicznymi. Dzięki nowej maszynie Robodrill α-D21LiB5 Plus możemy jeszcze skuteczniej podnosić jakość, stabilność procesów i efektywność pracy. Wprowadzenie tej jednostki pozwala nam na zachowanie wysokiej precyzji i powtarzalności obróbki detali przy większych wolumenach produkcyjnych. Konstrukcja i możliwości techniczne Robodrill α-D21LiB5 Plus Robodrill α-D21LiB5 Plus wyposażono w mechanizm ruchu liniowego dla osi X, Y i Z, oferujący zakres pracy 700 x 400 x 330 mm oraz dużą powierzchnię roboczą o wymiarach 850 x 410 mm. Maszyna obsługuje maksymalne obciążenie stołu wynoszące 300 kg. Dzięki precyzyjnym prowadnicom liniowym oraz solidnej konstrukcji ramy maszyna zachowuje stałą sztywność, co jest kluczowe dla uzyskania powtarzalności wymiarowej. Ta funkcjonalność sprawdza się szczególnie przy produkcji komponentów dla sektora obronnego, gdzie kluczowe są kryteria jakościowe i wytrzymałościowe. Wydajne wrzeciono do wszechstronnej obróbki metali Wrzeciono Robodrill α-D21LiB5 Plus osiąga prędkość 24 000 obr./min, co umożliwia dynamiczną obróbkę różnych materiałów – od lekkich stopów po wytrzymałe metale. W niższych prędkościach maszyna oferuje stabilność pracy przy materiałach o większej gęstości, natomiast przy maksymalnych obrotach zapewnia doskonałe cięcie lekkich stopów. Automatyzacja i szybka wymiana narzędzi Robodrill α-D21LiB5 Plus został wyposażony w system magazynowania na 21 narzędzi, z czasem wymiany wynoszącym zaledwie 1,6 sekundy. Krótszy czas wymiany narzędzi minimalizuje przestoje i zwiększa efektywność przy produkcji seryjnej, co pozwala na płynne i ciągłe realizowanie zleceń. Prędkość i precyzja – klucz do realizacji wymagających projektów Robodrill α-D21LiB5 Plus osiąga maksymalną prędkość przejazdową 54 m/min, a posuw roboczy do 24 000 mm/min, umożliwiając przeprowadzanie szybkich operacji przy zachowaniu wysokiej dokładności. Dwukierunkowa dokładność pozycjonowania wynosząca poniżej 0,006 mm oraz powtarzalność na poziomie 0,004 mm zapewniają zachowanie stabilności wymiarowej w całym procesie produkcyjnym. Rozbudowa możliwości produkcyjnych SIM Gdynia dzięki Robodrill α-D21LiB5 Plus Rosnące zapotrzebowanie na komponenty o wysokiej precyzji w sektorze obronnym oraz innych branżach wymagających najwyższych standardów jakości zmotywowało nas do inwestycji w maszynę, która sprosta tym wyzwaniom. Robodrill α-D21LiB5 Plus umożliwia realizację zleceń o wyższych wymaganiach technicznych, zapewniając jednocześnie powtarzalność i skrócony czas realizacji. Dzięki tej maszynie możemy sprawniej zarządzać zasobami oraz terminami, co stanowi istotną wartość dodaną dla naszych partnerów biznesowych. Podsumowanie Inwestycja w Robodrill α-D21LiB5 Plus otworzyła przed nami nowe możliwości w zakresie precyzyjnej obróbki skrawaniem, które spełniają najwyższe wymagania techniczne naszych klientów. Wysokie parametry maszyny umożliwiają precyzyjne utrzymanie tolerancji, szybki czas wymiany narzędzi oraz minimalizację przestojów. Dzięki temu SIM Gdynia wzmacnia swoją pozycję jako niezawodny partner dla firm, które oczekują stabilnych procesów produkcyjnych, dokładności wymiarowej i krótkich terminów realizacji.
Inwestycja SIM Gdynia w piłę tarczową CMB-100CNC Amada
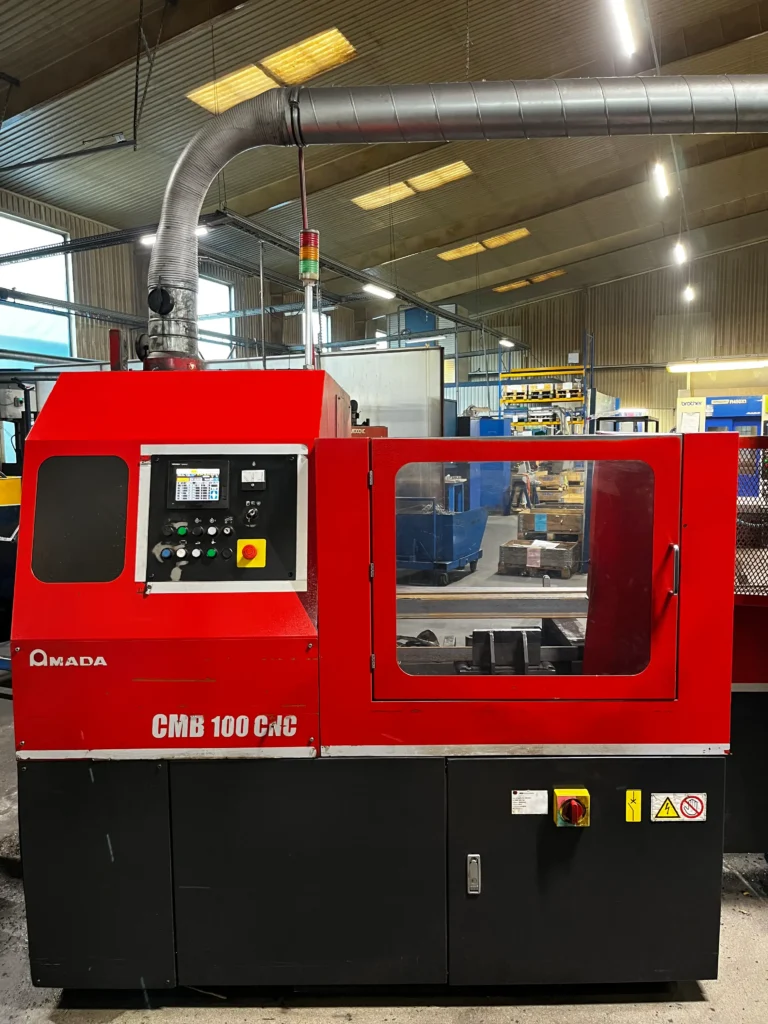
W SIM Gdynia rozwijamy nasze możliwości produkcyjne, wprowadzając do parku maszynowego piłę tarczową CNC CMB-100CNC marki Amada. To nowoczesne narzędzie pozwala nam na jeszcze precyzyjniejsze i szybsze cięcie materiałów, takich jak stal konstrukcyjna, aluminium, mosiądz czy brąz. Dzięki tej inwestycji nie tylko skracamy czas realizacji zamówień, ale także podnosimy jakość i zakres oferowanych komponentów. Nowa piła wspiera nas w realizacji bardziej wymagających projektów, odpowiadając na rosnące potrzeby naszych klientów. Technologia CNC w piłach tarczowych – zasada działania i kluczowe funkcje Technologia CNC (Computer Numerical Control) w piłach tarczowych umożliwia pełne zautomatyzowanie procesu cięcia, co znacząco podnosi dokładność oraz powtarzalność obróbki. Dzięki precyzyjnemu systemowi sterowania komputerowego operator może wprowadzać ustawienia cięcia, takie jak kąt, głębokość oraz prędkość, które następnie są realizowane przez urządzenie bez konieczności dodatkowych korekt. Technologia CNC w piłach pozwala na dynamiczne dostosowanie parametrów cięcia w czasie rzeczywistym, co jest szczególnie ważne przy obróbce materiałów o różnych właściwościach fizycznych. Dzięki funkcjom takim jak automatyczny podajnik oraz system monitorowania zużycia ostrza, piły tarczowe CNC mogą pracować bez przerw i minimalizować ryzyko błędów ludzkich, co przyspiesza realizację dużych zleceń. Specyfikacja techniczna piły tarczowej CMB-100CNC CMB-100CNC to wszechstronne urządzenie przeznaczone do cięcia komponentów o różnych wymiarach: obsługuje materiały o średnicy od 25 do 100 mm dla elementów okrągłych oraz od 25 x 25 mm do 75 x 75 mm dla elementów prostokątnych. Główne parametry techniczne: Wpływ piły CMB-100CNC na procesy produkcyjne SIM Gdynia Wdrożenie piły tarczowej CMB-100CNC znacząco poprawiło efektywność naszych procesów produkcyjnych. Precyzja cięcia oraz możliwość regulacji parametrów, takich jak prędkość ostrza i liczba zębów, pozwalają na dostosowanie pracy urządzenia do specyficznych wymagań materiału, co zwiększa płynność produkcji seryjnej. Dzięki automatycznemu podajnikowi i możliwości pracy z dużymi partiami produkcyjnymi lepiej zarządzamy zasobami i terminowo dostarczamy produkty naszym klientom. CMB-100CNC, dzięki swojej mocy i automatyzacji, stała się kluczowym elementem naszej linii produkcyjnej, co pozwala sprostać rosnącym wymaganiom rynku oraz utrzymać najwyższą jakość produkcji.