What is the difference between turning and milling? – Key differences in CNC machining
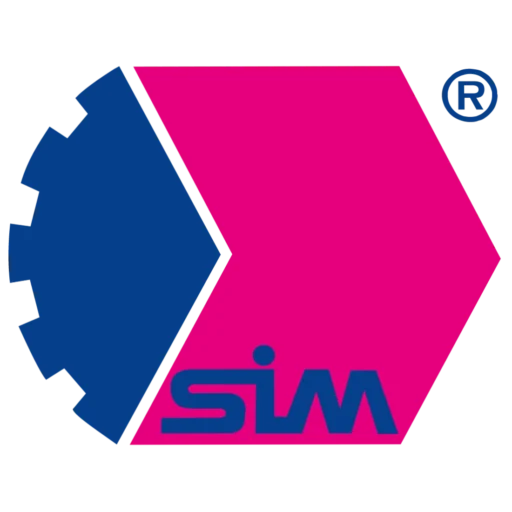
In industries where every micrometer and every second of production counts, CNC machining (Computerized Numerical Control) has become the foundation of modern manufacturing. The two most important cutting methods are turning and CNC milling. Although both techniques are used to precisely shape metal and plastic parts, they differ in their range of applications, tool movement, and geometric capabilities. In this article, we explain how CNC turning differs from milling, when to use each method, and how to choose the right technology. What is CNC turning? In CNC turning, the workpiece is clamped in a chuck and rotates around its own axis, while the cutting tool moves along the X and Z axes. This principle allows for the efficient removal of material from cylindrical and conical surfaces. This technology is used, among other things, for the production of shafts, pins, bushings, rings, and threads. It is ideal for mass production, where dimensional repeatability and process stability are key. What is CNC metal milling? CNC milling is a process in which a tool (milling cutter) rotates while the workpiece remains stationary or moves along the X, Y, and Z axes – and in the case of 4- and 5-axis machines – also around the rotary axes. Milling allows the machining of flat surfaces, holes, pockets, bevels, and 3D structures. It is indispensable in projects where parts require multiple operations in different planes, from injection molds and machine bodies to medical and aerospace components. CNC milling and turning – a comparison of technologies To understand CNC milling and turning, it is worth comparing these processes in terms of key aspects: Movement of elements Workpiece geometry Machining range Milling is a highly versatile process that allows for the creation of very complex shapes. CNC turning, on the other hand, allows for the efficient creation of symmetrical elements while maintaining perfect axial alignment. How to choose the right CNC machining method? The choice between CNC milling and turning depends primarily on the geometry of the detail, the type of material and the production requirements. Geometry Turning is chosen for axially symmetrical components – shafts, sleeves, pins. Milling is used for parts with complex surfaces, spatial openings, and irregular shapes. Material Most metals can be machined using both methods. With plastics, milling provides greater dimensional stability and better process control. Accuracy Turning guarantees high coaxiality precision. Milling allows positioning relative to multiple planes. Production scale In the mass production of simple parts, turning is more effective. Milling is better suited to small-batch production of complex components. At SIM Gdynia, we combine both technologies to tailor the machining process to the customer’s requirements. We analyze each project individually in terms of functional and economic requirements. Summary CNC turning and milling are two different approaches to machining that complement each other in modern production. The choice of technology should be based on a design, tolerance and material analysis. Turning dominates in simple, axial parts where efficiency and repeatability are important. Milling allows for complete freedom in the design of spatial details and precise multi-axis machining. Understanding these differences is the foundation of effective technological cooperation – from design to the finished product.
Iscar technical training at SIM Gdynia – new Quicklogic tool line supports the development of precision CNC machining
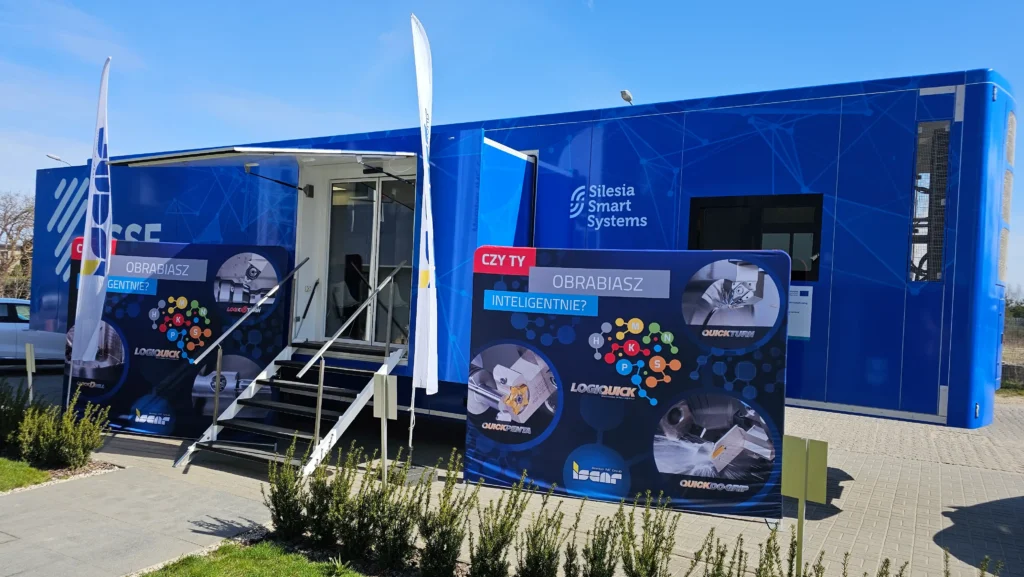
At SIM Gdynia, we prioritize the development of our team’s technical skills and the continuous improvement of our production processes. As part of these activities, in April we had the opportunity to participate in training conducted by Iscar, a global leader in cutting tools, at their mobile training center, which was hosted at our plant. Presentation of Quicklogic tools – innovations in machining During the meeting, we were presented with a new line of Quicklogic tools, designed to increase efficiency and precision in turning, boring, milling, and drilling. These tools are a response to the modern challenges in the production of mechanical components, carried out in short series and to individual customer orders. Iscar engineers presented both the design aspects of the tools and specific examples of their practical application. Particular emphasis was placed on the possibility of shortening the machining cycle time, improving tool life and increasing process repeatability – key parameters in professional CNC machining to order. Benefits for SIM Gdynia and our customers Participation in the training allowed us to become more familiar with modern technological solutions that we plan to implement in our machine park in the near future. Thanks to them, we will be able to even more effectively carry out orders in the field of turning, milling and comprehensive CNC machining, offering our customers even higher quality of workmanship while shortening delivery times. At SIM Gdynia, we constantly invest in development, both through the modernization of our technical infrastructure and specialized training for our team. Such meetings are an important part of building our technological advantage and maintaining the highest production standards. Thanks to the Iscar team We would like to thank Iscar for organizing a professional training course and for the opportunity to learn about the latest solutions in the field of machining tools. The meeting was a valuable source of knowledge and inspiration that we will use to further improve our technological processes.
What materials are CNC machined? An overview of the most commonly used raw materials in the production of mechanical components at SIM Gdynia
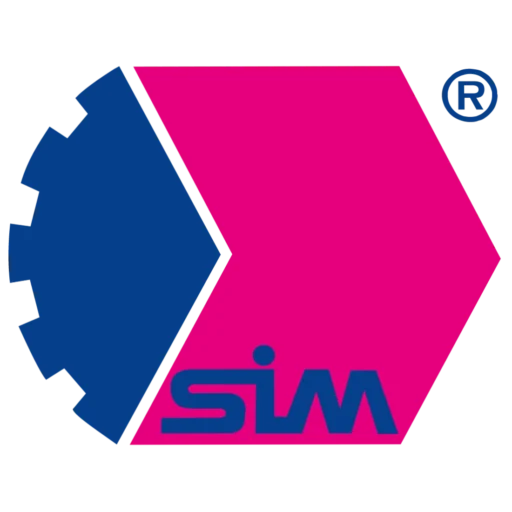
In the precision production of mechanical components, the selection of the right material is a key stage of the process. CNC machining – whether turning, milling or 5-axis machining – requires materials that not only meet strength requirements, but also work well with tools and cutting technology. At SIM Gdynia, we have specialized in CNC services for over 45 years and know how important the quality and type of raw material is. In this article, we present an overview of the materials we use most often in our production. Materials most commonly used in CNC machining Three main material groups dominate our machinery: carbon steel, stainless steel and aluminum. These raw materials form the basis for the production of precision components for industries such as the automotive, energy and mechanical engineering sectors. Carbon steel – versatile and robust Structural steel (e.g. S235JR, S355J2) and quenched and tempered steels such as C45, 42CrMo4, 16MnCr5 are the basic materials from which we produce a wide range of parts. Their availability, the possibility of precise CNC machining and excellent mechanical properties make them a reliable choice for many projects. Stainless steel – corrosion resistance Stainless steel is a material that is used in environments requiring increased chemical resistance. At SIM Gdynia, we often machine austenitic and ferritic steels, which require the appropriate selection of cutting parameters due to their hardness and tendency to harden during machining. Aluminum – lightness and versatility Thanks to its low weight and good conductive properties, aluminum is often used in industries such as aviation, automotive and electronics. In the CNC milling process, it allows for very high accuracy and short cycle times. Less typical, but equally important materials Although the vast majority of parts produced in our hall are made of metals, there is no shortage of projects using plastics and non-ferrous metals. Plastics At SIM Gdynia, we process engineering plastics such as POM, PA and PTFE. These materials are characterized by a low coefficient of friction, good chemical resistance and ease of processing, although they require precise tool alignment and thermal deformation control. Non-ferrous metals: copper, brass, bronze These materials are used less frequently but are still important, especially for the production of electrically conductive or wear-resistant components. They require special tool geometries because they are relatively soft and can stick to the cutting edge. How do the physical properties of materials affect CNC machining? Each material reacts differently to the cutting process. Hardness affects tool wear, ductility determines the type of chip, and thermal conductivity affects dimensional stability during machining. Machinability of materials – a key technological parameter Machinability is a collective term for how easily a material can be processed. Grades such as 11SMn30 (free-cutting steel) have very good machinability and are ideal for mass-produced parts. Stainless steel or copper, on the other hand, require sharper tools, lower feed rates and more efficient cooling. Quality control and material conformity Every material used in our production undergoes a quality control process. The certification of the material and the possibility of verifying its chemical composition are crucial. Thanks to the SPECTROMAXx spectrometer, we are able to quickly and precisely confirm the material’s conformity with the specification – before it even reaches the CNC machine. We work with renowned suppliers who offer a wide range of steel bars (drawn and rolled) in grades such as 11SMn30, C35, ETG88 and 20MnCr5. These grades provide different mechanical properties, such as hardness, machinability or fatigue strength, depending on the final application of the workpiece. Summary Choosing the right material for CNC machining is not just a question of availability – it is a decision that affects the entire production cycle, the service life of the tools, the quality of the finished component and its compliance with technical requirements. At SIM Gdynia, we attach great importance to the quality of raw materials, precise control and matching of machining technology to a specific material.If you are looking for a partner who not only produces custom-made mechanical components but also advises you on the best raw material, please contact us. Our services CNC guarantee quality, experience and technological know-how.
Zoller Smile 400 – micrometric precision at theheart of CNC machining
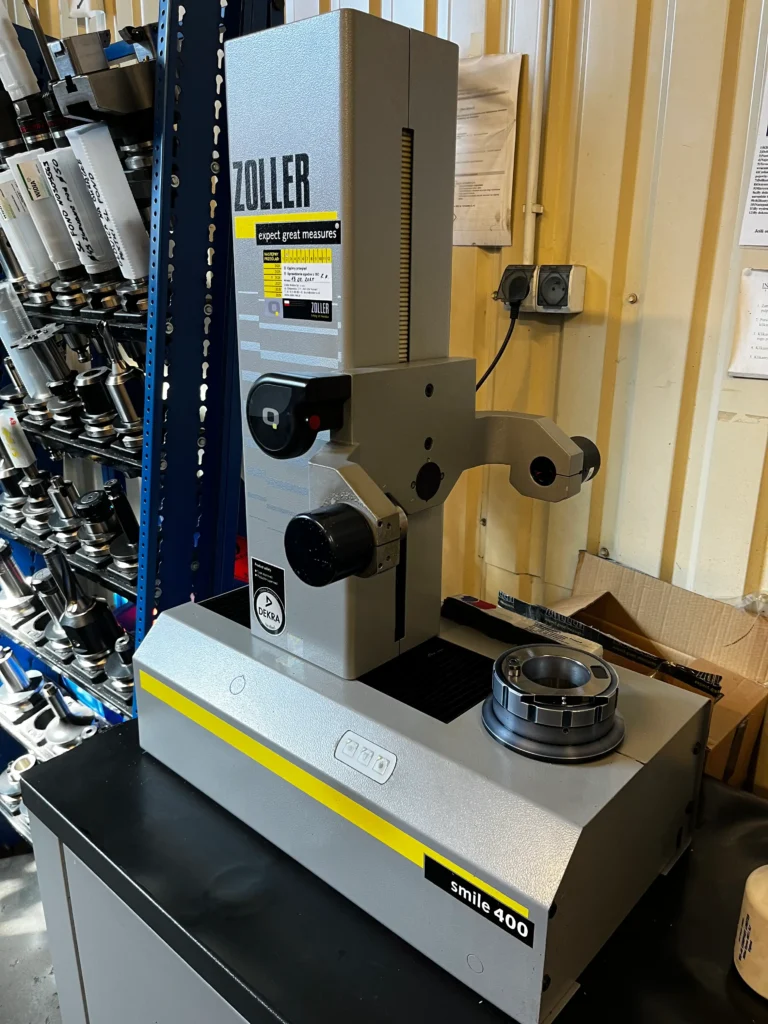
In modern industrial manufacturing, precision is no longer a competitive advantage –it is an absolute standard. In the area of CNC machining, where every hundredth of amillimeter counts, setting tools with high accuracy directly affects part quality,machine efficiency and reduced downtime.That’s where the Zoller Smile 400 comes in – it’s a compact, yet fully professionalsetting and measuring device that ideally meets the needs of manufacturing plantsworking in cutting technology. What is the Zoller Smile 400? The Zoller Smile 400 is an instrument used for setting and measuring tools used inmachining, both in the context of metal milling and other operations. Despite itscompact size, the device offers extensive functionality. Its standard equipment includes: ● Tool measurement in transmitted and reflected light,● The ability to print tool data labels,● Touchscreen electronic panel with intuitive interface,● a function for determining the maximum profile of multi-tools. Measuring ranges of the device: ● Z = 420 / 600 / 800 mm● D = 420 / 620 mm The entire device has been designed and manufactured at ZOLLER’s headquarters,using first-class components. The robust industrial design allows the device to beused both in the tool room and directly at the CNC machine. Using the Zoller Smile 400 in the CNC machining process In a production environment like SIM Gdynia’s, where lathe centers and 5-axis millingmachines are in operation, any error in tool alignment can result in loss of material,the need for corrections or, in extreme cases, damage to the workpiece. With theSmile 400, operators can quickly and accurately set tools before they reach themachine spindle. Advantages of integrating the device into the process:● Reduced preparation time – tools are ready to go before they reach themachine.● Micrometric setting precision – especially important in the production of partswith tight tolerances.● Minimization of errors and repeatability of results between shifts. This is crucial, especially in large batch production, where quality and cyclicality arenon-negotiable. The Smile 400 supports CNC machining of metals at the highestlevel – from milling tool steel to cutting aluminum or plastic parts. Zoller Smile 400 as part of a precision CNC machiningstrategy By implementing a measuring and setting device such as the Zoller Smile 400, amanufacturing plant is taking an important step toward standardizing quality andincreasing productivity. It’s not just an “extra piece of equipment” – it’s a real tool thatinfluences production strategy. Long-term advantages:● Increased operational efficiency – less downtime, better production planning.● Higher output quality of parts – fewer rejects, fewer revisions.● Workplace safety – reduced risk of tool or part damage.● Easier control of multi-tools – important, for example, for precision metalmilling. Summary Zoller Smile 400 is a tool that combines compact size with industrial precision. In therealities of modern CNC machining, where every time saving and every micrometermatters, it’s an investment that pays off quickly – both in quality and in workflow. At SIM Gdynia, we understand perfectly how important it is to control every step ofthe process. That’s why we continually invest in solutions that support our operatorsand engineers in their daily work – including equipment like the Zoller Smile 400. Want to learn more about how we optimize measurement processes at SIM Gdynia?Contact us and let’s talk about how we can support your production.
Welding service standards in the production of mechanical components – Know-How from SIM Gdynia
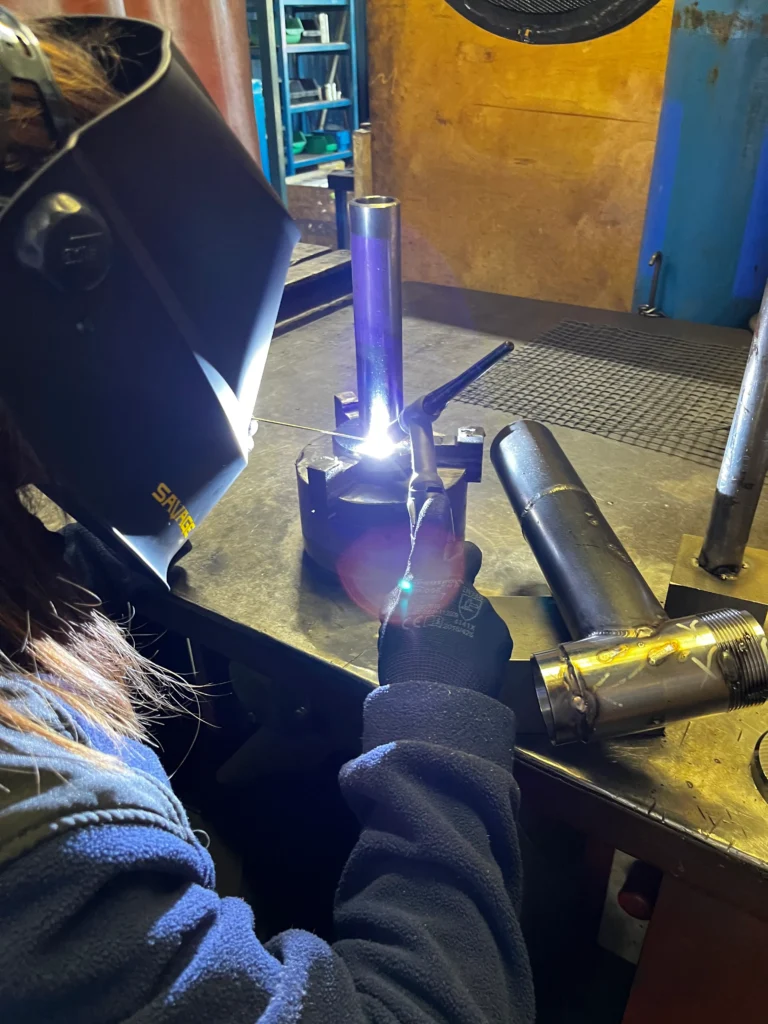
High-quality welding connections are a key element in the production of mechanical components used in a variety of industries – from machinery and energy, to defense, to automotive, construction and many others. The durability and strength of finished components depend not only on the technologies used, but also on the compliance of the welding process with strict standards. At SIM Gdynia, we use proven procedures that produce repeatable and durable joints that meet the highest industry requirements – regardless of the sector in which they are used. Standards governing welding processes In order for welding processes to comply with technical requirements and meet specific strength criteria, it is necessary to apply standards governing metal joining technology, welder qualifications and quality control methods. Of particular importance in the manufacture of mechanical components are: At SIM Gdynia, we attach great importance to adhering to the above standards, which allows us to provide mechanical components with high durability and compliance with customer requirements. Our processes are supervised by certified specialists and are subject to systematic verification to ensure that each weld meets stringent quality standards. Welding technologies used in the production of mechanical components TIG welding (141) – precision and heat control TIG (141) welding produces high-quality and precise welds. By using a tungsten electrode and shielding gas, the process minimizes the effect of heat on the structure of the material. This technology makes it possible to obtain clean and aesthetically pleasing welds, which is crucial for parts with increased corrosion requirements. MIG/MAG welding (135/136) – durability and efficiency MIG/MAG (135/136) welding is used in joining low-alloy steel, where the strength of the joint and resistance to dynamic loads are crucial. This process makes it possible to achieve durable welds while maintaining high production efficiency. Materials used in the welding process In the production of mechanical components, it is crucial to use the right materials, which must meet the requirements for mechanical strength, resistance to external factors and compliance with technical documentation. At SIM Gdynia, we weld both stainless steel, which requires precise control of thermal parameters to avoid overheating and structural changes, and low-alloy steel, used in machine structures and components subjected to intensive mechanical loads. Summary Professional welding services in the production of mechanical components must meet the stringent requirements of EN ISO 15614-1, ISO 9606-1 and EN ISO 9712 to ensure the durability and precision of joints. At SIM Gdynia, we ensure that each process is carried out to the highest standards, allowing us to deliver components that meet the expectations of customers in a wide range of industries. Thanks to the use of certified procedures, we are able to carry out both single projects and larger series. Constant quality control and supervision by an experienced team guarantee that each weld is made with the highest precision and in accordance with the technical documentation.
SIM Gdynia winner of OTIF95 Supplier Performance Award from KION Group
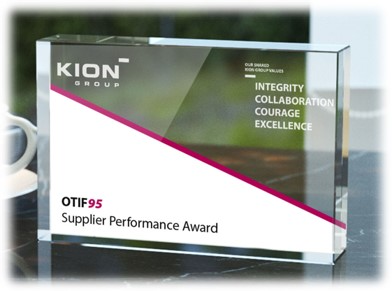
We are proud to announce that SIM Gdynia has been awarded the OTIF95 Supplier Performance Award from KION Group for on-time and complete deliveries in 2024. The OTIF95 award is given to suppliers who consistently deliver on schedule and in full quantity. Earning this title is the result of our efficient organization of production processes, precise logistics planning and the SIM Gdynia team’s commitment to maintaining the highest quality of service. SIM Gdynia’s cooperation with KION Group KION Group is a world leader in logistics automation, integrating modern transportation, warehousing and goods flow control software systems. As part of our cooperation, we supply high-quality mechanical components that are a key element of the systems used in modern distribution centers. Precision in manufacturing, timeliness and flexibility in order fulfillment make our solutions fully responsive to the requirements of the intralogistics industry. Achieving top performer status in the OTIF95 program confirms that our processes meet the highest standards for delivery reliability, which translates into stability for the KION Group’s supply chain and their customers around the world. Acknowledgements and commitment for the future We would like to thank the KION Group team for the award and our employees for their commitment and consistency in the pursuit of operational excellence. It is thanks to their collective efforts that SIM Gdynia has been ranked among KION’s top suppliers. For us, the OTIF95 award is not only a source of pride, but also a commitment to continue improving our processes to maintain the highest level of service and meet the expectations of our partners. We are not slowing down – we continue to work to maintain and further improve our delivery standards.
CNC machining of rims, gears and other large-size and complex parts.
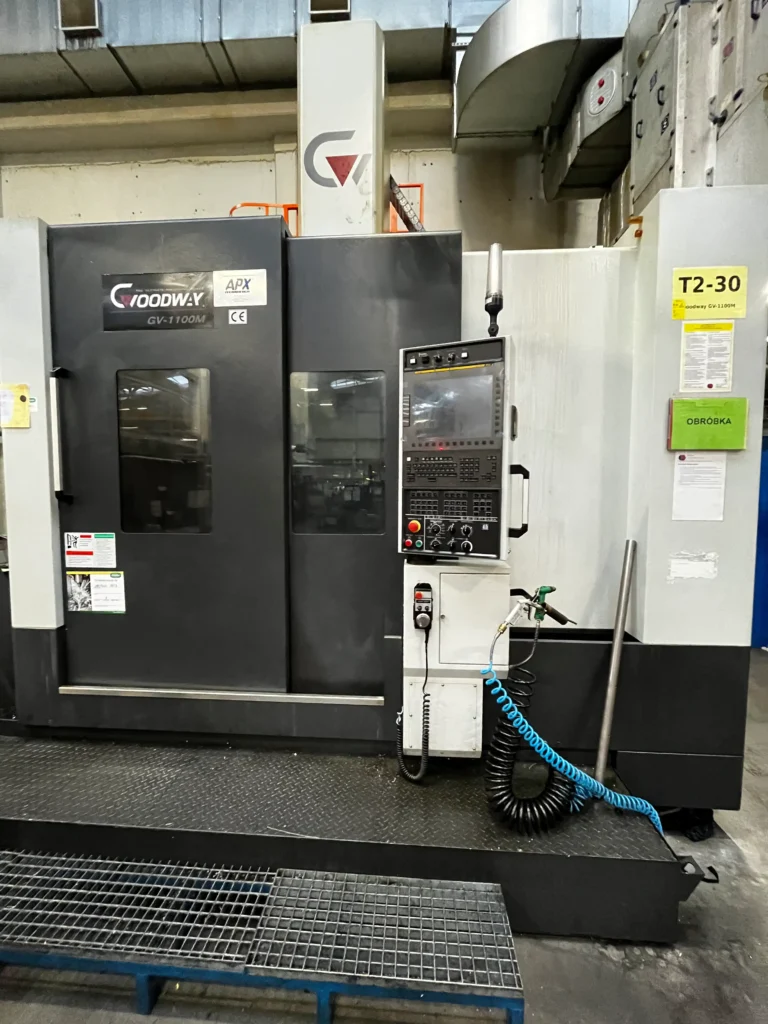
Large-sized workpieces such as large rims, discs or gears place special demands on technologists and machine operators. Cutting large surfaces with relatively small widths is sometimes problematic due to stresses that can lead to undesirable deformations and difficulties in achieving part stability. However, proper cnc machining with the right machine tool can optimize the process, guarantee high dimensional repeatability and minimize the risk of errors. Challenges in CNC machining of large-sized parts. Hoops with large diameters yet small widths require precise clamping and balancing to avoid vibration during operation. Machining with suitable CNC lathes allows these tasks to be carried out efficiently, while maintaining stable parameters over the course of successive production runs. CNC lathe for large-size parts – the genesis of SIM Gdynia’s investment. In 2021, we decided to expand the technological capabilities of our company by purchasing a CNC lathe that would meet the requirements of large-format machining. The machine tool was to make it possible to cut parts with a diameter of more than 1 meter and weighing several tons. Such parameters turned out to be indispensable in the production of large-format components used in hydraulic, mining and other heavy industry sectors. Characteristics and specifications of the GV-1100 CNC machine tool. The purchased lathe model GV-1100 is equipped with a table with a diameter of 900 mm, which allows the machining of parts with a maximum diameter of up to 1,100 mm. The machine tool is capable of handling workpieces weighing up to 4,000kg, which is completely sufficient for machining parts of considerable dimensions. At the heart of the machine is a spindle with two gears, offering speeds from 1 to 500 rpm and a torque of up to 10,170 Nm. The 37 kW (continued) / 45 kW (30 min) main drive guarantees smooth operation, even during intensive material removal. An additional advantage is the presence of the C-axis (motor output 3 kW), with which more complex operations can be performed, such as milling outlines on the workpiece. The lathe has an X axis that allows travel of up to 1,300 mm (in the range -100 ~ 1,200 mm) and a Z axis with a stroke of 900 mm. Depending on your needs, it is also possible to use the W axis, which has a stroke of up to 600 mm. Servo motors of 7 kW (X-axis) and 9 kW (Z-axis) provide adequate dynamics and precision of movements, and the feed rate reaches 12 m/min in the X-axis and 10 m/min in the Z-axis. The machine is equipped with a tool magazine with a capacity of 12 pieces (taper BT-50), which makes it easier to carry out machining processes without frequent manual tool changes. The maximum tool weight reaches 50 kg, which allows the use of robust cutting heads. The whole machine is controlled by a FANUC Oi-TF Plus system, ensuring high repeatability and positioning accuracy, which for the X and Z axes is ±0.007 mm per 500 mm. Machining process – stages of operation. Preparing a workpiece for cnc machining first requires proper clamping and fixing the base. Then the operator selects the optimal cutting parameters, taking into account the dimensions, shape and material of the workpiece and the planned number of cycles. Due to the large size of the workpiece, it is sometimes necessary to gradually increase the spindle speed or feed rate so as to reduce the risk of vibration. At the final stage, quality control is carried out, including verification of dimensions, shape tolerances and surface evaluation. Summary. Cutting large-size parts requires specialized machines that provide power, stability and an adequate working range. The GV-1100 lathe purchased in 2021 allows machining parts with diameters of up to 1,100 mm and payloads of up to 4,000 kg, which has greatly expanded SIM Gdynia’s machining capabilities. All this makes the machining process for the most demanding large parts run smoothly and allows to achieve the desired quality parameters, regardless of the industry in which the workpieces are finally used.
CNC machining of shafts and workpieces – the role of grinders in achieving perfect concentricity.
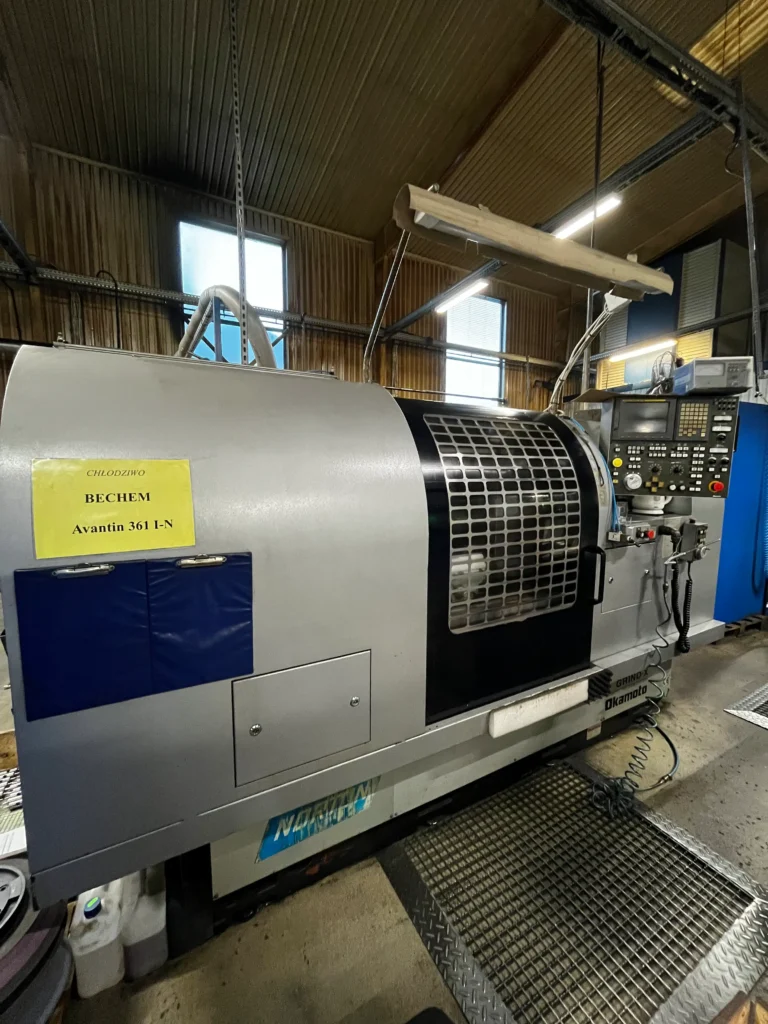
CNC machining of shafts and workpieces requires high dimensional accuracy and appropriate geometric tolerances. Particularly important is concentricity, on which the smooth and trouble-free operation of rotating components depends. Metal grinding plays a key role in achieving the desired results, thanks to which perfectly smooth surfaces can be achieved and radial and overall runout can be reduced. The importance of concentricity in CNC machining. Coaxiality is a parameter that determines whether the axis of rotation of the workpiece coincides with the axis of the reference system along its entire length. Even slight deviations can lead to increased vibration, faster bearing wear, trouble during assembly or interference with the entire system. For shafts used for power transmission or serving as bearing elements, it is important to keep radial runout and total runout within strict limits. Precision metal grinding makes it possible to control this aspect with accuracy even to hundredths or thousandths of a millimeter. The role of metal grinding in achieving perfect tolerances. Metal grinding in the CNC machining process performs a finishing function, ensuring proper surface properties and shape. As a result, roughness is reduced, and the machining itself takes less time compared to traditional methods, since numerical control enables repetitive, tightly controlled tool movements. Okamoto 300 series grinder (model 350) – characteristics of our CNC machine tool. As an example of a machine that proves itself in precision machining, we can cite Okamoto’s 300 series grinder in the 350 model, which allows the machining of workpieces with diameters up to 350 mm. The machine’s design allows it to hold a workpiece of up to about 1,300 mm between the claws, giving it a wide range of applications. Thanks to a spindle with a speed range of 10 to 500 rpm, it is possible to adapt the working parameters to the type of material and the intended machining purpose – from precise finishing to efficient removal of overfeeds. A minimum set feed rate of 0.001 mm ensures high control over roughness and compliance with required tolerances. The robust design reduces vibration, resulting in better process stability. It also reduces radial runout and total runout and enables perfect concentricity. Efficient cooling and contamination separation systems help sustain consistent conditions during machining, so results remain repeatable. Conclusion. In CNC machining of shafts and other rotating components, it is important to strive for tight tolerances and concentricity. Metal grinding, especially grinding of metal surfaces with CNC machines, guarantees precision that is crucial in industries where even micrometer deviations can carry serious consequences. Grinding machines such as the Okamoto 350 make it possible to work with a wide range of workpieces while ensuring a high level of process control, stable conditions and low surface roughness. As a result, the finished products have excellent performance qualities: they are resistant to vibration, wear more slowly and require less frequent service intervention. At SIM Gdynia, the above-discussed approach influences the satisfaction of our customers and long-term cooperation based on quality and trust.If you are looking for a trusted mechanical components contractor, we warmly invite you to fill out our contact form: https://www.simgdynia.eu/kontakt/
Christmas wishes and summary of the year 2024
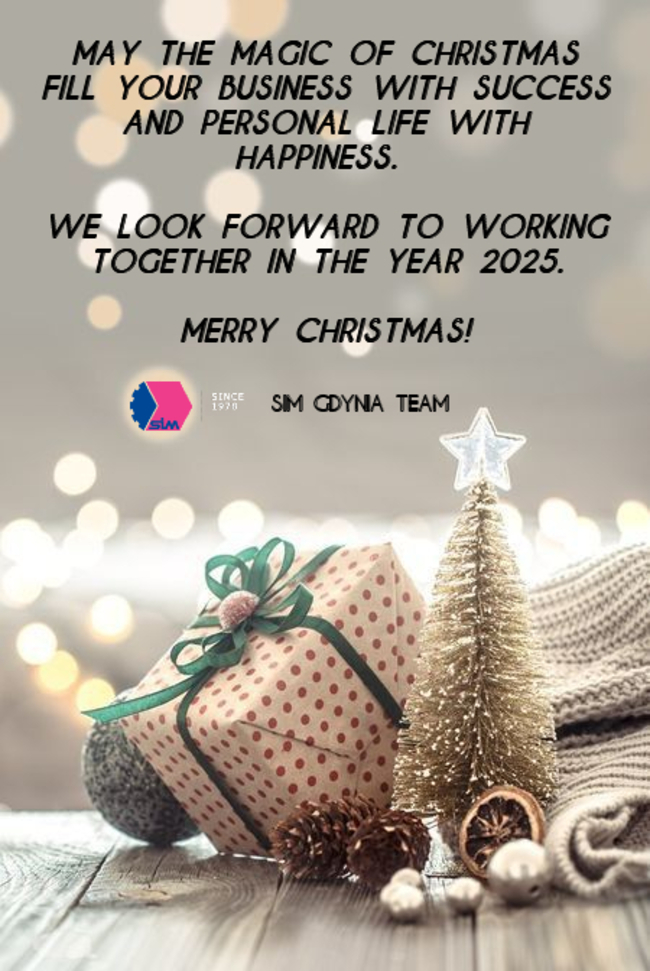
On the occasion of the upcoming Christmas and New Year, we would like to sincerely thank our employees, business partners, colleagues and customers for their support, trust and fruitful cooperation in the past year. 2024 was a period of intensive development for SIM Gdynia, especially in the defense sector, where we not only expanded our operations, but also established key strategic partnerships. SIM Gdynia’s most important events in 2024 MSPO 2024 Our presence at the International Defense Industry Exhibition (MSPO) 2024 was one of the highlights of the year. This trade fair provided an excellent opportunity to showcase our capabilities in manufacturing precision mechanical components for the defense sector. Through numerous meetings and discussions, we had the chance to establish new business contacts and consider potential projects using our technologies in advanced defense systems. Enforce Tac 2024 Enforce Tac 2024 is another important event on our calendar. The fair brought together more than 12,000 experts from around the world, creating a unique platform for sharing knowledge and experience. It showcased the latest defense-related technologies, including vision systems, autonomous vehicles and weapons solutions. SIM Gdynia’s participation allowed us to better understand the future needs of the industry, as well as showcase our solutions in areas such as the production of components for drones, weapons systems, and shielding and housing for electronic devices. Forbes Forum of Family Businesses honorable mention We were honored to be included in the prestigious Forbes Forum of Family Companies 2024. This honor is extremely valuable to us, as it highlights our financial stability, consistent growth and contribution to the regional economy. This achievement would not have been possible without the commitment of our team and the trust placed in us by our partners and customers. The award motivates us to further improve our processes and introduce new technologies to strengthen the company’s position in domestic and foreign markets. Thanks and good wishes from the SIM Gdynia team On the occasion of Christmas, we wish you many joyful moments with your loved ones, filled with peace and warmth. May the New Year 2025 bring health, success and the realization of professional and personal dreams. Thank you for your trust and cooperation so far. We look forward to the next year with hope, hoping to continue joint projects and further develop our relationship. Merry Christmas and prosperity in the New Year wishes the SIM Gdynia team!
How to measure workpieces in CNC machining? Measurement methods and their applications
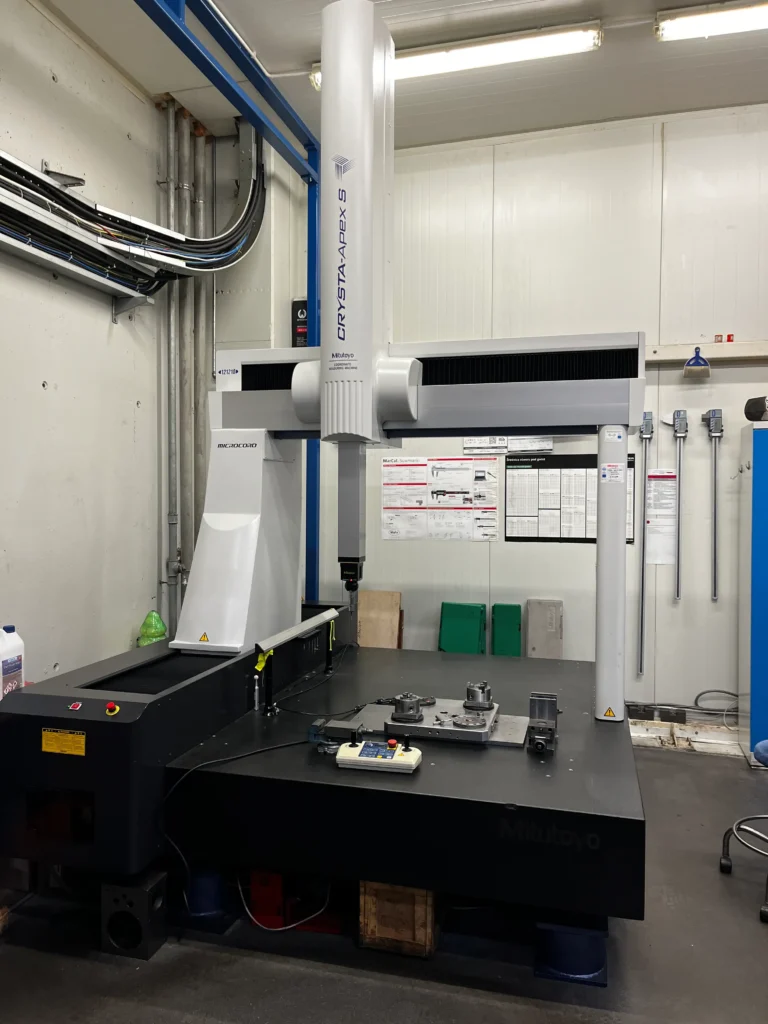
Precise measurements play a key role in CNC machining processes such as milling, turning and drilling. The main goal is to ensure that the dimensions of the workpieces conform to technical requirements and maintain high production quality. Dimensional accuracy directly affects the functionality and durability of final products, so it is essential to constantly control machining parameters, especially in serial production, where repeatability is a priority. Measurements also make it possible to quickly detect and correct deviations, which minimizes material losses. In advanced manufacturing processes such as those used at SIM Gdynia, measurements are an integral part of quality assurance. Traditional measurement methods Traditional measuring tools, such as calipers and micrometers, have been the cornerstone of dimensional control in CNC machining for decades. Calipers can measure lengths, diameters and depths to an accuracy of about 0.02 mm, making them versatile tools. Micrometers, on the other hand, offer an accuracy of up to 0.001 mm, making them suitable for measuring workpieces that require greater precision, such as shafts and bushings. Despite their versatility, traditional tools have limitations. Measuring complex shapes or workpieces with complex geometries can be time-consuming and subject to greater risk of error. In such cases, it becomes necessary to use more advanced technologies that automate the measurement process and achieve greater accuracy. Modern solutions – coordinate measuring machines Coordinate measuring machines (CMMs) represent a state-of-the-art approach to dimensional control in CNC machining. They enable precise measurement of workpieces in three axes (X, Y, Z) using contact or non-contact probes. Measuring machines such as Mitutoyo’s offer the ability to measure complex geometries with accuracy down to microns. The machine works on the principle of collecting points from the surface of the workpiece, moving along pre-programmed trajectories. The measurement program for each workpiece is created once, which guarantees repeatability and standardization of the process for subsequent measurements. At SIM Gdynia, we use such solutions to obtain detailed dimensional analysis of parts with complex shapes, which allows us to maintain high quality standards. The design of the measuring machine makes it possible to measure parts with large dimensions, such as machine parts or components used in aviation. By automating the measurement process, the impact of human error can be minimized and the speed of dimensional analysis can be increased. 3D scanners and laser sensors in CNC measurement Today, industry is increasingly using non-contact technologies such as 3D scanners and laser sensors. Scanners allow comprehensive mapping of the geometry of a workpiece, which is particularly useful for parts with irregular shapes. The technology enables the creation of 3D models that can be used for comparison with CAD data and for further analysis. Optical and laser sensors offer precision and speed, making them ideal for real-time measurements, especially in mass production. Their use minimizes the risk of damage to the workpiece, which is important for delicate or deformation-prone materials. How to choose the right measuring methods? Choosing the right measuring tool depends on several factors, such as dimensional tolerances, workpiece geometry and surface quality requirements. For simple workpieces with less stringent tolerances, traditional tools such as calipers or micrometers may be sufficient. However, for more complex workpieces that require analysis in multiple planes, coordinate measuring machines or 3D scanners are the best solution. At SIM Gdynia, we take a diverse approach to measurement, adapting methods to the specifics of the project. As a result, we are able to ensure precision in both unit and batch production. Summary Measurement in CNC machining is the foundation of precise and efficient production. From traditional tools such as calipers and micrometers to advanced CMMs and 3D scanners, each technology has its place depending on the specifics of the project. At SIM Gdynia, we are constantly developing our measurement capabilities, using the latest technologies to deliver products that meet the most stringent technical standards. This allows us to offer our customers reliability, repeatability and the highest quality at every stage of order fulfillment.