The latest investment in the HBS‑GQ‑20F laser marking machine – even greater possibilities at SIM Gdynia
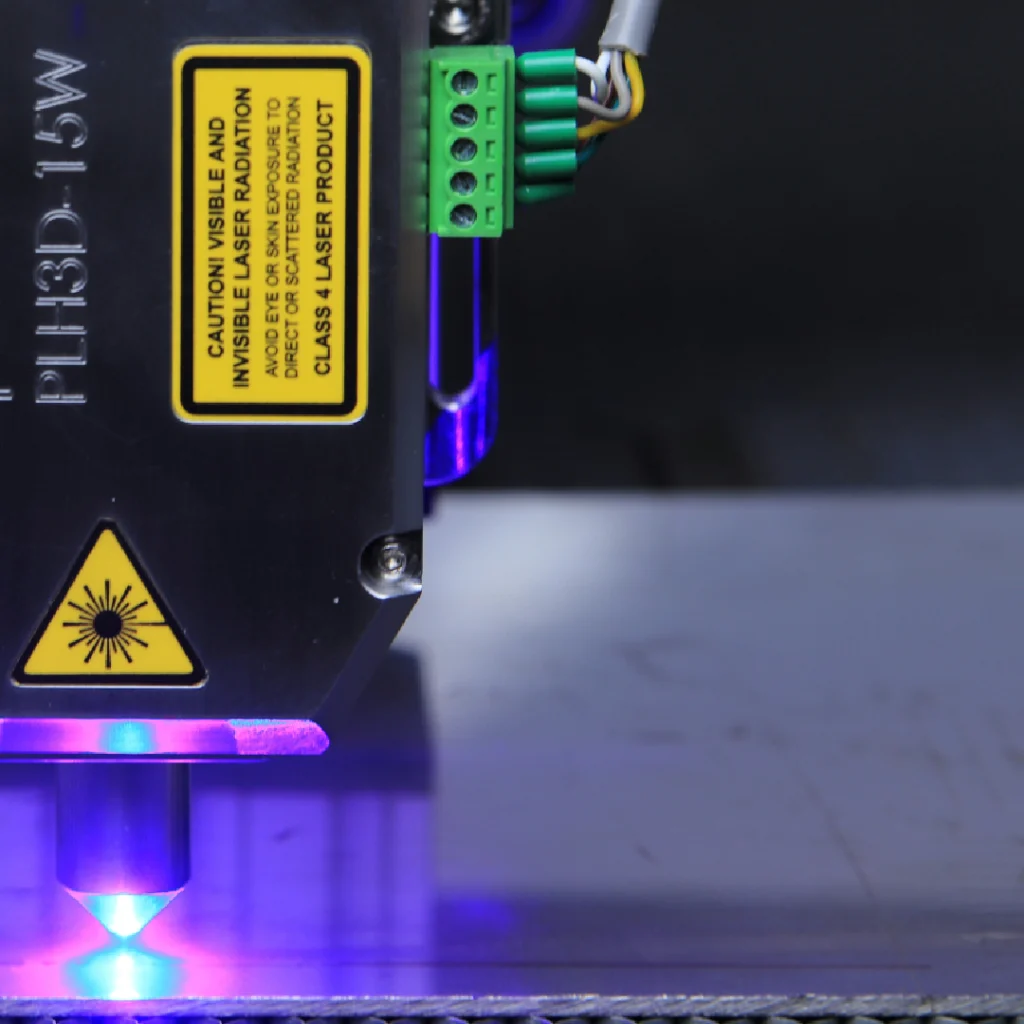
At SIM Gdynia, we are constantly investing in technologies that increase the precision, efficiency, and quality of our services. The latest step in this direction is the purchase of a modern HBS‑GQ‑20F laser marking machine. This device allows us to mark large series of parts even more efficiently, with greater accuracy and in less time. A new quality of marking at SIM Gdynia The HBS‑GQ‑20F laser marking machine is a modern solution dedicated to the precise marking of metals and plastics. Thanks to its closed design, high safety class and advanced automation, this device perfectly fits our production needs. The integrated Windows operating system allows for quick and intuitive process configuration, which significantly speeds up production preparation, especially for large volumes. Key technical data of the HBS-GQ-20F Parameter Value Marking area 110 × 110 mm (optional: 65 × 65 mm, 170 × 170 mm, 220 × 220 mm, 300 × 300 mm) – depending on the lens used Marking depth Up to 1.2 mm – adjustable depending on the material and number of passes Marking speed Up to 12,000 mm/s – very fast marking with high quality Positioning accuracy ± 0.001 mm – extremely precise reproduction in the same place even with large series Laser power 20 W, 30 W, 50 W or 100 W – depending on requirements, from delicate marking to engraving hard materials Laser source operating time Up to 100,000 hours – long service life without frequent replacement of components Power supply/energy consumption 220 V / max. 500 W – low operating costs, connection to a standard industrial socket Cooling Air-cooled – no water or additional cooling systems required Operating conditions Temperature from –10 °C to +60 °C, humidity 5–95% – stable operation even in harsh production environments Supported file formats AI, PLT, DXF, TIFF, JPG and others – compatibility with popular graphics and CAD software A new standard at SIM Gdynia Thanks to this investment, we can mark mechanical components faster, more precisely and more efficiently than ever before. This means benefits for both us and our customers.
Report from the ITM INDUSTRY EUROPE 2025 trade fair – SIM Gdynia at the center of industrial innovation
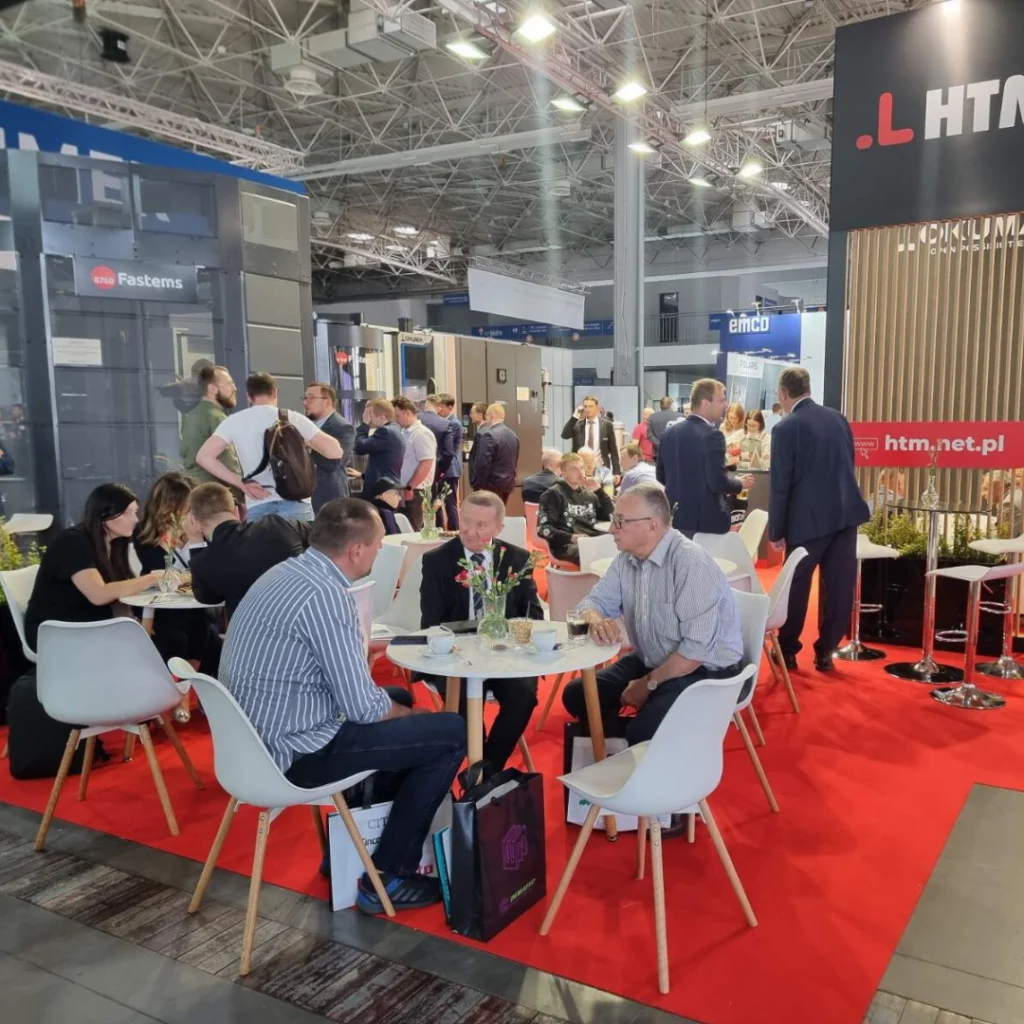
On June 4, 2025, three representatives of our staff took part in the ITM INDUSTRY EUROPE trade fair in Poznań. This event attracts leading representatives of European industry every year, offering a space for knowledge exchange, trend observation, and strategic purchasing decisions. What is ITM INDUSTRY EUROPE? ITM INDUSTRY EUROPE is the largest and most comprehensive industrial event in Central and Eastern Europe. It takes place in Poznań and attracts thousands of professionals from industries related to metalworking, automation, robotics, metrology, and future technologies. Under the common banner of ITM, machine manufacturers, system integrators, engineers, and leaders in digital solutions for industry come together. The main idea of the event focuses on Industry 4.0 – the full integration of production processes with digital analytics, automation, and artificial intelligence. Investments and inspiration During our presence at ITM INDUSTRY EUROPE 2025, we had the opportunity to analyze a number of modern solutions, compare technologies, and hold many valuable discussions with suppliers of production support systems. We are returning from this visit not only with new knowledge, but also with concrete decisions. We have made an investment that will translate into further improvements in our technological and operational processes in the coming months. This is a strategic step for us towards increasing efficiency and maintaining the highest quality standards we offer our customers. Summary Participation in ITM 2025 confirmed that the future of industry belongs to companies that can combine precision, automation, and digitization. Thanks to our presence in Poznań, we better understand the market development trends and the needs of our partners. We would like to thank the event organizers for creating a space that truly supports the development of industry in Poland and Europe.
Investing in your own machine park or CNC outsourcing?
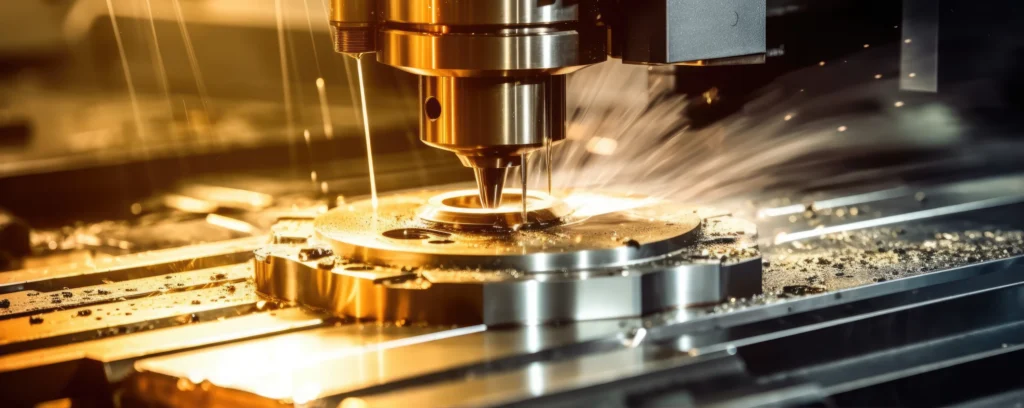
The decision of whether to build your own CNC machine park or use the services of a subcontractor who will manufacture mechanical components on request is one of the most important operational choices in the industrial sector. It is a choice that affects not only the company’s finances, but also the time needed to implement new products, the availability of technology, operational flexibility, and design risk. Not every manufacturing company needs to invest millions of dollars in modern machining centers and build technological facilities from scratch. On the other hand, it is not always worthwhile to outsource processes that are critical to quality, confidentiality, and precision. In this article, we will analyze both approaches: investing in machines and outsourcing CNC machining, based on specific figures, real scenarios, and proven market practices. The costs of investing in a CNC machine park – what do you really need to consider? Buying a machine is just the beginning. Your own CNC machine park generates a number of additional costs that must be taken into account at the investment planning stage: It is worth noting that CAM systems can be offered as perpetual licenses with an annual fee for updates or in a subscription model, where you pay annually. Price differences result from functionality, the number of machine axes, access to simulation and post-processors. For an example 5-axis center, annual operating costs – excluding depreciation – can easily exceed PLN 400,000. This is a real challenge, especially if the machine is not working at full capacity. Source: want.net – CNC Machine Cost Explained Is 2,000 hours the break-even point? In an industrial environment, it is generally accepted that approximately 2,000 machine hours per year is the approximate break-even point for an investment in a CNC machine tool. Where does this figure come from? It is roughly equivalent to the full utilization of a single machine in a single-shift system: 8 hours per day, 5 days per week, 50 weeks per year (with a reserve for service downtime and holidays). Above this threshold, the investment begins to pay for itself – unit production costs decrease and capital efficiency increases. The longer the machine runs, the better the ROI (Return on Investment). But in practice, this threshold can be difficult to achieve. Market data shows that the average utilization of CNC machines in single-shift plants is only 26% of available production time – significantly less than the required 2,000 hours. This is the result of underutilization, downtime, changeovers, and variable orders. Conclusion? 2,000 hours is a realistic but ambitious goal that only pays off with regular, well-planned production volumes. In other cases, outsourcing should be considered as a solution with lower financial risk. Source: https://www.machinemetrics.com/stateoftheindustry2022 When is it worth investing in your own CNC machine park? Having your own CNC machine park is a solution that can bring tangible benefits. This is especially true when: While some of these needs can be met by external contractors, having your own machines gives your company decision-making independence, shorter response times, and the potential to optimize technology in real time. What does CNC machining outsourcing offer? Outsourcing in the production of mechanical components is now much more than just ordering a part. Modern service companies are becoming technology partners, offering access to specialized machines without the need to build infrastructure from scratch. Within a single partnership, you can obtain: Importantly, outsourcing also gives you access to the experience of a team that has been implementing projects for many industries for years. This experience translates into better technological advice, faster implementation, and a lower risk of errors during production. When is outsourcing CNC machining advantageous? Outsourcing CNC machining is worth considering when: More and more companies are using a mixed model – keeping basic production in-house and outsourcing more complex or occasional orders to external partners. Summary The decision on whether to develop your own machine park or outsource CNC machining is not just a matter of calculating the unit cost of production. It is a strategic choice that affects your operating model, cost structure, and project delivery speed. Investing in machines is a good idea when you have a large, stable volume, need full control over the process, and have clearly defined technical competencies within the company. It’s a model that gives you independence, but it requires capital, planning, and high machine utilization to be profitable. Outsourcing CNC machining, on the other hand, is a flexible, scalable and low-risk solution. It works well for companies that operate with variable demand, develop new products or need quick access to technology that is not cost-effective to implement permanently.
Lightweight but Demanding: How to Succeed in Aluminium CNC Machining
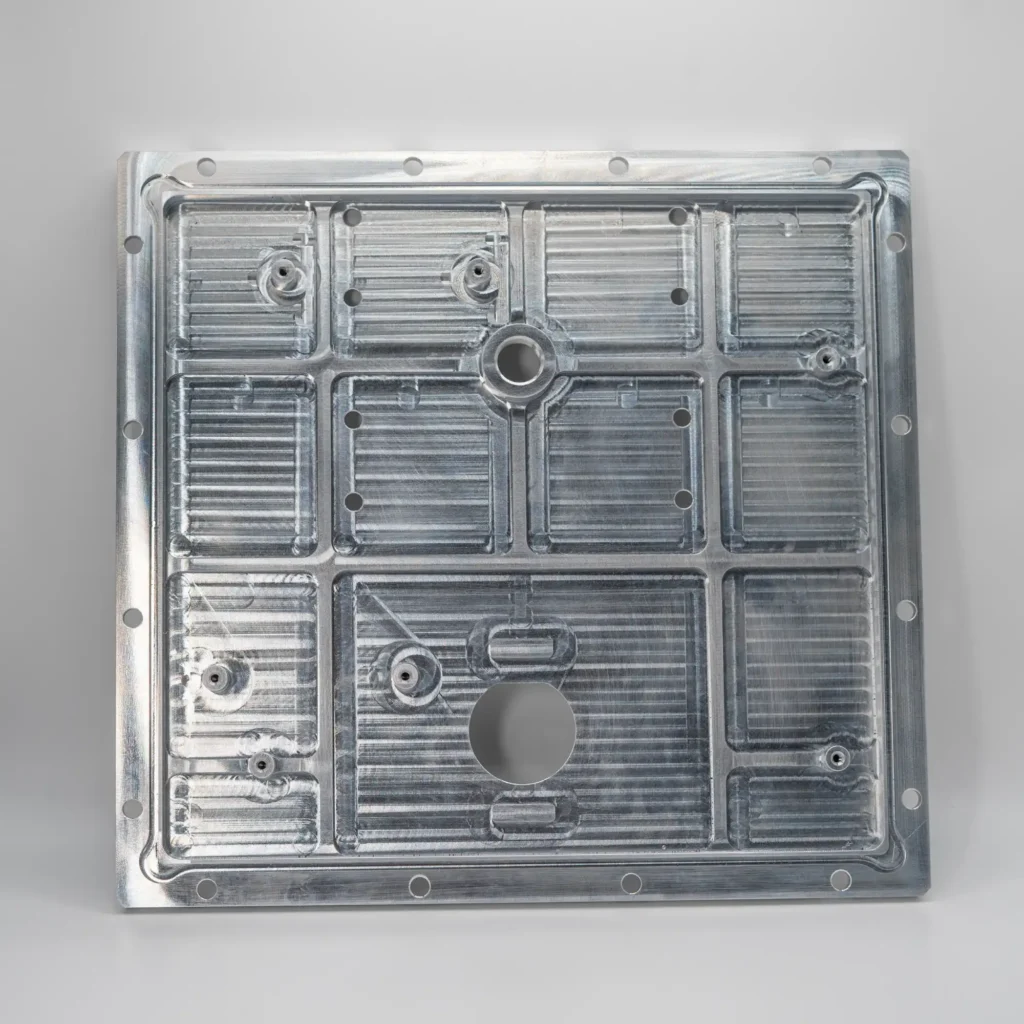
Aluminum is a material widely used in the production of mechanical components. Its light weight, corrosion resistance, and favorable strength-to-weight ratio make it ideal for precision engineering applications. But what makes aluminum such an attractive material also means that its machining requires more than just a standard approach. CNC machining is now the basis of modern production, including when working with aluminum. However, the effectiveness of the entire process depends on many factors. From the selection of tools and coatings, through cutting parameters, to the cooling method. It is these elements that determine the surface quality, repeatability, and durability of the finished part. Drawing on our many years of experience in CNC metalworking, this article describes specific solutions that have proven themselves in production and allow you to achieve stable quality of the finished part. Aluminum – material specifications and problems encountered in CNC machining Before we move on to cutting strategies, it is worth taking a look at the properties of aluminum that directly influence the choice of machining parameters. Understanding these properties is crucial for the stability and repeatability of the entire process. Materialproperties What does this mean in practice? Low density (2.6–2.8 g/cm³) Aluminum is lightweight, which allows for higher rotational speeds and feed rates, and the machine is not as heavily loaded as with steel. High thermal conductivity Heat quickly escapes from the cutting zone, but mainly to the tool. Without efficient cooling, the blades overheat and wear out faster. Low hardness (HV ≈ 25–120) Sharp tools with a large rake angle can be used. Cutting is smooth and the load on the machine tool remains low. Viscosity and adhesion Aluminum tends to stick to the blade. Friction-reducing coatings, polished chip grooves, and properly selected cooling help to prevent this. Although at first glance, turning and milling aluminum seems “easy,” in practice it requires a great deal of attention and technological precision. Aluminum alloys and their machinability with CNC technology Not all aluminum behaves the same when in contact with a tool. Depending on the chemical composition and hardness, different alloys may require completely different cutting parameters—from speed and force to optimal spindle speed, control, and cutting tool. Below are a few examples of popular alloys used in the production of aluminum components: Knowledge of the type of aluminum alloy facilitates the machining of the material. Without it, it is difficult to select the right tools, set the cutting parameters, and predict the behavior of the workpiece during production. Main processes and types of CNC aluminum machining Aluminum can be effectively machined in several different ways, depending on the needs of the project and the expected results. CNC milling It works well for both precision components and large structural blocks. Concurrent milling gives a better surface quality, while counter-rotating milling is suitable where stability is required. For larger volumes of material, full milling is used. Thin-walled parts are machined with minimal allowance and well-chosen cooling. CNC turning Used for axially symmetrical parts: shafts, sleeves, rings. In turning, it is crucial to maintain a stable feed rate and the correct cutting edge radius, especially for thin-walled parts. If the cutting parameters are too low, vibrations and an irregular surface will occur. If they are too aggressive, excessive chip accumulation and the risk of workpiece deformation will occur. Drilling and threading The most common problems are burrs and hole deformation. Drills with a larger point angle and good chip removal are used. Forming taps are suitable for threading — they do not cut, but shape the thread. This eliminates chips and strengthens the connection, especially in thin-walled components. Grinding and surface preparation Surface quality is crucial for anodizing. Any scratches will be visible after oxidation. Therefore, parts are often subjected to additional finishing operations — finishing milling or grinding with emulsions and fine-grained abrasives. CNC tools used for machining aluminum For aluminum, it is essential to use tools that enable efficient chip removal and reduce the risk of material build-up on the cutting edge. The most commonly used types of tools are: The choice of tool depends on the technological operation, workpiece geometry, and quality requirements. Each tool has its own specific characteristics and is best suited for specific applications. Cooling and lubrication of aluminum during the machining process CNC machining of aluminum requires special attention in terms of cooling, as aluminum quickly transfers heat to the tools. Lack of effective cooling quickly leads to a deterioration in the surface quality of the parts, accelerates tool wear, and can also cause thermal deformation of the workpiece. The most commonly used cooling and lubrication methods are: Modern aluminum cutting strategies One of the most popular approaches is HPC (High Performance Cutting) – a deep cutting technique with a narrow blade width. It allows for a significant increase in feed rate without the risk of tool overload or deterioration of workpiece parameters. HSC (High Speed Cutting) is ideal for thin-walled aluminum components. Thanks to very high rotational speeds and low cutting forces, this method ensures precise milling without deformation, even of delicate structures. Trochoidal milling is also becoming increasingly popular – a strategy that involves guiding the tool along a curved, dynamic path. This ensures even blade wear, better cooling, and minimizes mechanical and thermal loads. Summary – aluminum rewards precision Aluminum is a material with great potential, but also with complex technological characteristics. To achieve repeatable quality and high performance in CNC machining, a good machine is not enough. You need well-chosen tools, well-thought-out cutting strategies, effective cooling, and knowledge of the properties of the specific alloy. It is precisely this approach — based on practice and experience — that allows you to fully exploit the potential of aluminum and avoid typical production problems.
CNC metal working – the foundation of precision industrial manufacturing
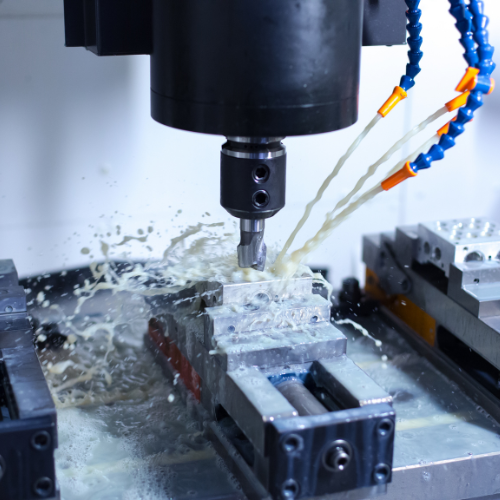
Metals have been the basis of industrial construction for centuries. Their strength, conductivity, and workability make them indispensable in many applications. In the manufacturing industry, “good quality” is no longer enough—today, micrometric precision, repeatability in every series, and flexibility in design changes are what count. Under these conditions, traditional machining methods become a barrier to development. They are being replaced by solutions that combine automation with reliability, led by CNC machining, which we explain in detail in the article “What is CNC machining?” Process flow – what does metal machining on CNC machines look like? The process begins with the preparation of technical documentation in CAD (Computer-Aided Design) format, which is then converted into CAM (Computer-Aided Manufacturing) code. This code contains instructions for the CNC machine regarding the tool trajectory, rotational speed, feed rate, and other parameters. The accuracy of this data is crucial to achieving the desired end result. At this stage, the actual metalworking on CNC machines takes place. The selection of tools, cutting parameters, and machining strategies depends on the geometry of the part, the material, and the type of technological operation. Modern CNC centers are often equipped with automatic tool changers, cooling systems, and measuring sensors, which allow for high repeatability, shorter production times, and minimized risk of errors. After the main cutting operations, the surface finishing stage follows, which may include: Quality control at this stage is crucial to ensure compliance with technical requirements. Challenges in CNC metalworking Each material reacts differently to machining. What works for steel may be completely wrong for aluminum or brass. The right choice of tools and strategies is the key to quality, repeatability, and process durability. Structural steel (e.g., S235, S355) This is one of the simpler groups of materials in terms of machining. Both HSS (High-Speed Steel) and carbide tools can be used. Structural steel can be machined quickly and without major restrictions, but for longer operations it is advisable to check the wear of the tool edges regularly. Stainless steel (e.g. AISI 304, 316) Requires a more thoughtful approach. It is hard and at the same time “stretchy” – it tends to stick to the cutting edge. This causes problems with chip removal and accelerated tool wear. Blades with friction-reducing coatings, such as AlTiN (titanium and aluminum nitride), are usually recommended for machining this material. Hardened steel (>45 HRC) Hardened steel requires solid carbide tools (VHM – from German Vollhartmetall) and appropriate coatings, e.g. TiSiN (titanium and silicon nitride), which increase wear and temperature resistance. The process must be stable – rigid clamping, short strokes, precise path. The parameters must be selected sensibly, depending on the tool diameter, geometry, and machine capabilities. Aluminum Aluminum is a machinable material, but due to its ductility and low hardness, it requires a specific approach. During machining, it produces long chips that easily clog the cutting space, and when working with thin-walled parts, there is a risk of vibration and deformation. The best results are achieved with solid carbide (VHM) milling cutters with a large rake angle (approx. 45°) and a polished chip surface. Brass and copper These materials are very easy to machine and are often considered “easy” for CNC machining. An overly aggressive rake angle or a rough cutting surface can lead to material tearing, local overheating of the cutting edge, and accelerated wear. This is because the heat generated during machining is very quickly transferred to the workpiece, which in thin-walled components can result in deformation or dimensional changes. For CNC machining of brass or copper, solid carbide (VHM) cutters with very sharp, precisely ground edges and a maximally smooth surface are recommended. Understanding the physical and chemical properties of the material being machined and precisely adjusting the cutting strategy has a direct impact on the final quality of the component, the service life of the tools, and the efficiency of the entire cutting process. What can go wrong with CNC metal machining – and how can it be prevented? Three main problems can occur during CNC metal machining: 1. Chatter This leads to an uneven surface, poorer accuracy, and faster wear of the cutting surfaces. The most common causes are excessive tool projection, lack of rigidity in the clamping, or incorrect cutting parameters. 2. Incorrect cutting parameters Excessive speed, feed rate, or cutting depth can lead to blade overheating, tool breakage, and poor surface quality. 3. Tool wear Every milling cutter, drill, and tap has a limited service life – if not checked regularly, it can damage the workpiece or cause errors in the entire series. When is it worth outsourcing CNC metalworking to an experienced company? For series production, complex geometries or high quality requirements, working with an experienced contractor helps to avoid errors and delays. Not only is a precise machine park crucial, but also practical knowledge of different alloys, their behavior during processing, and possible design limitations. Summary of CNC metalworking CNC metalworking is more than just removing excess material. It is a complex technological process in which precision tools work together with computer control, and each stage is based on engineering knowledge and familiarity with the properties of materials. Thanks to this technology, it is possible to manufacture components with complex geometries, high quality, and repeatability in a fast, safe, and economical manner. Behind the efficient CNC process is a team of specialists. The designer creates a model of the part, the programmer prepares the machining code, and the operator supervises the production process on the machine. It is the combination of human competence and the capabilities of modern machine tools that allows us to achieve a level of precision that cannot be guaranteed by traditional methods.
Training in Shrink Fit technology and spindle clamping force control at SIM Gdynia

At SIM Gdynia, we are constantly training, testing, and implementing solutions that have a real impact on the quality of CNC machining. In May 2025, our headquarters hosted a specialized technical training course organized by experts from Hahn+Kolb and Diebold, leaders in the field of tools and clamping systems. The meeting focused on shrink fit technology and spindle clamping force control systems – key solutions for precision, repeatability, and process safety. A practical approach to innovation The training was attended by our technologists, setters, and foremen – practitioners who are responsible for the reliability of production at SIM Gdynia on a daily basis. The meeting was practical in nature. Specific cases were discussed, the application of Shrink Fit technology was tested on real components, and the impact of spindle clamping force on the stability and durability of machining was analyzed. Shrink Fit is a tool clamping technology that utilizes the phenomenon of thermal expansion – after cooling, the holder clamps the tool tightly, ensuring extreme rigidity, minimal runout, and high process repeatability. The spindle clamping force measurement system, on the other hand, allows the clamping parameters in the CNC machine to be controlled, which has a direct impact on the machining quality and service life of both the tools and the spindle itself. Building an advantage with knowledge We would like to thank the representatives of Hahn+Kolb and Diebold for the inspiring training and for sharing their expert knowledge. Initiatives like this are extremely important to us – they help develop the competence of our team and directly translate into production efficiency. At SIM Gdynia, we build our competitive advantage not with words, but with action. This is another step towards even higher precision and reliability of our CNC services.
What is CNC machining?
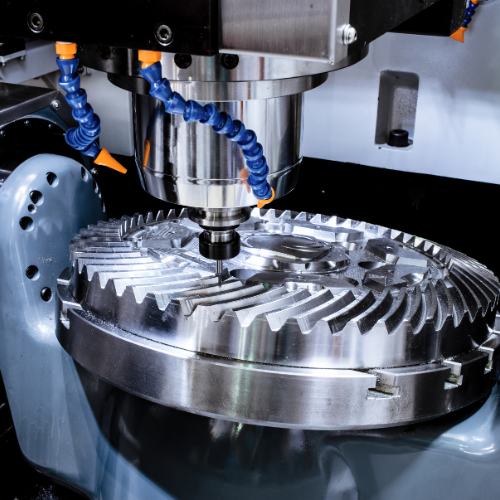
CNC machining (Computer Numerical Control) is a technological process involving the shaping of materials using numerically controlled machine tools, i.e. machines that perform tasks according to pre-programmed computer instructions. A technical design – usually prepared in a CAD (Computer-Aided Design) program, i.e. a tool for computer-aided engineering – is converted into code that directs the machine’s work. CNC milling machines, lathes, and grinders perform precise movements, removing material from the workpiece and creating a part with specific shapes and dimensions. This can be compared to the opposite of 3D printing – instead of adding material, CNC machining involves its controlled removal until the desired shape is achieved. Types of machining There are several main types of machining, each of which is used to achieve different effects: The variety of machining methods offers a wide range of possibilities for shaping components – from rough removal of material to precise surface finishing. The use of machining in industry This technology is used both in mass production and in the manufacture of unique, specialized components. Below are the key industries in which CNC machining is particularly important: Machining plays a key role wherever precision, repeatability, and the ability to work with a wide variety of materials are important. What materials can be machined with CNC? Thanks to its versatility, CNC machining can be used for both easily machinable materials and those requiring specialised tools. The most commonly machined materials include: The choice of material always depends on the intended use of the component, expectations regarding durability, geometry, production costs and possible finishing operations. Advantages of CNC machining The advantage of CNC machining is full control over the process, which makes it possible to achieve repeatable results even with very complex designs. Other key benefits include: CNC machining is ideal wherever quality, repeatability, and efficient production management are important. Summary – what is CNC machining? CNC machining is a modern manufacturing method that combines precise computer control with a wide range of technological possibilities. It allows for the efficient and economical production of parts of varying complexity – from metals, plastics, composites, and special materials. This technology is used in almost every branch of modern industry and allows for both serial and single-piece production. Its main advantages are repeatability, flexibility, reduced lead times, and reduced material waste. All this makes CNC an indispensable tool in the design and production of modern components.
SIM Gdynia supports local sport – partnership with Chwaszczyno Sports Club
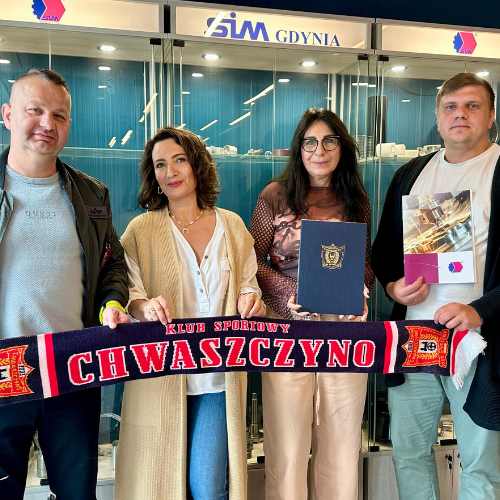
At SIM Gdynia, we believe that the true strength of industry lies not only in technology, but also in the people and communities we support. That is why we are proud to announce that on May 13, 2025, we signed an official partnership agreement with Chwaszczyno Sports Club. This is the beginning of a collaboration that we hope will bring long-term benefits to young athletes and the local community. A shared vision for development The agreement was signed by Anna Szczypek, President of SIM Gdynia, and Janusz Płocki, President of Chwaszczyno Sports Club. The meeting not only confirmed the formal commitment, but also emphasized our shared values of development, passion, and commitment to local initiatives. SIM Gdynia has become the club’s main sponsor. We believe that thanks to this cooperation, young players will gain even better conditions for development, training, and achieving their sporting goals, both small and large. Young people are the future, not only in sports The partnership with KS Chwaszczyno is more than just sponsorship. It is a real investment in young people who, thanks to technical and organizational support, can spread their wings. As a manufacturing company, we understand the value of systematic work, discipline, and teamwork – and it is sport that teaches these attitudes from an early age. Our support is aimed at improving the training infrastructure, developing the training program, and enabling participation in more competitions. We want every child training at KS Chwaszczyno to have the opportunity to pursue their sporting dreams. We look to the future with hope We hope that this partnership will be the beginning of many joint projects – tournaments, campaigns promoting physical activity, and family events. Our support is not just a logo on jerseys – it is a real presence in the lives of young athletes and their families. We can’t wait for the first successes of the KS Chwaszczyno players, whom we already strongly support. We are with you – on and off the pitch!
Family Picnic on Children’s Day–join us for a celebration on June 15!
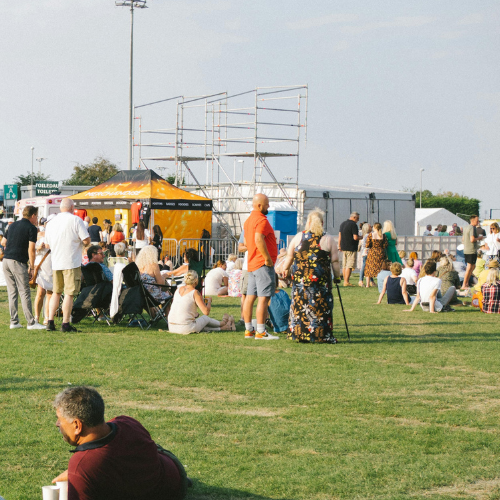
At SIM Gdynia, we believe that the strength of a company lies not only in technology and precision, but also in relationships – both professional and family. That is why we are delighted to invite SIM Gdynia employees and their loved ones to a Family Picnic on Children’s Day, which will take place on June 15, 2025 at the Toyota Arena Stadium in Chwaszczyno. The event is scheduled to start at 1:00 p.m. Why is it worth participating? The Family Picnic is a great opportunity to spend time together in a relaxed atmosphere – away from everyday responsibilities, surrounded by nature, with plenty of attractions for children and adults. The event combines physical activity, educational elements, and relaxation in the fresh air. All in a friendly, safe, and well-organized space. The program includes, among other things: Prize lottery A raffle will be held among the participants of the event, with prizes including: SIM Gdynia zone – for registered employees only For SIM Gdynia employees who register to participate in the event, we have prepared a separate tent area with free refreshments. Registration is internal. Only registered participants will be able to use this zone during the picnic. See you on June 15 in Chwaszczyno! We encourage you to participate in the event with your families – a day full of joy, integration, and shared moments that will remain in your memory for a long time awaits you.
SIM Gdynia received the OTIF95 award from the KION Group
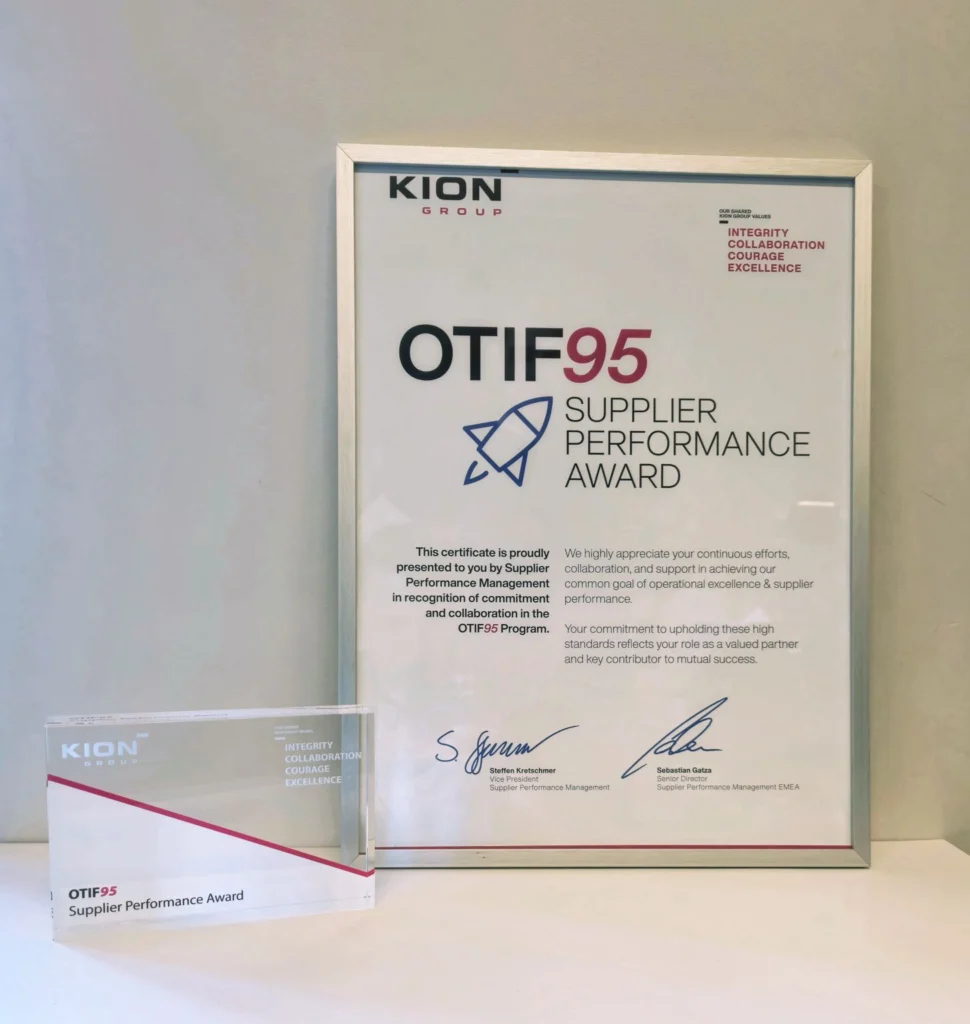
In February, we announced that SIM Gdynia had won the OTIF95 Supplier Performance Award presented by the KION Group. Today, we are pleased to announce that we officially received this award on 03.04.2025. The award confirms our reliability in delivery and the efficiency of our operational processes. You can read more about the OTIF95 program and our cooperation with the KION Group in our previous article: SIM Gdynia wins OTIF95 Supplier Performance Award from the KION Group We would like to thank the KION Group for their trust and recognition – it is a strong motivation for us to continue improving.