CNC-Bearbeitung auf 3, 4 und 5 Achsen – Unterschiede, Vorteile und Beschreibung der Arbeitsweise.
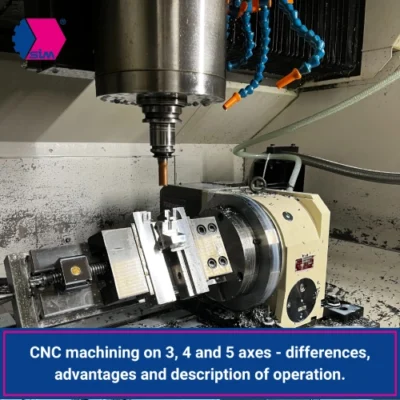
Einführung Die 3-Achsen-CNC-Bearbeitung war lange Zeit der Industriestandard, aber der technologische Fortschritt hat zur Einführung von 4- und 5-Achsen-Maschinen geführt, die viel breitere Möglichkeiten bieten. In diesem Artikel befassen wir uns mit den Unterschieden bei der Bearbeitung von Teilen zwischen der 3-Achsen- und der 4- bzw. 5-Achsen-Bearbeitung. Was ist die 3-Achsen-CNC-Bearbeitung, und wo liegen ihre Grenzen und Anwendungen? Die 3-Achsen-CNC-Bearbeitung gilt als Standard- und Basisverfahren bei der Herstellung von Metall- und Kunststoffteilen. Sie ist durch die Bewegung des Arbeitswerkzeugs in drei Achsen gekennzeichnet: X (horizontal), Y (vertikal) und Z (Tiefe). Dies macht sie zu einem äußerst vielseitigen Verfahren im Bereich der einfachen Teilegeometrien. Grenzen der 3-Achsen-Bearbeitung Bei der 3-Achsen-Bearbeitung kann das Werkstück nicht gedreht werden, was die Möglichkeit einschränkt, Bohrungen oder Fassungen in komplexen Winkeln ohne zusätzliches Einspannen und Ausrichten des Werkstücks durchzuführen, was die Produktionszeit erheblich verlängert. Komplizierte Formen mit Kurven oder solche, die eine präzise Bearbeitung auf mehreren Seiten erfordern, sind mit nur drei Achsen schwer oder gar nicht zu bearbeiten. Anwendungen der 3-Achsen-Bearbeitung Trotz dieser Einschränkungen bleibt die 3-Achsen-Bearbeitung in vielen Anwendungen ein unverzichtbares Werkzeug, insbesondere dort, wo die Teilegeometrie relativ einfach ist und keine komplexe Bearbeitung unter verschiedenen Winkeln erfordert. Sie wird häufig bei der Herstellung von Maschinenteilen, elektronischen Bauteilen und anderen Bereichen eingesetzt, in denen Geschwindigkeit und Produktionskosten ebenso wichtig sind wie die Präzision. 4-Achsen-Fräsen – Vergleich mit der 3-Achsen-CNC-Bearbeitung Beim 4-Achsen-CNC-Fräsen wird eine zusätzliche Achse eingeführt, die die Möglichkeiten der Teilebearbeitung im Vergleich zum zuvor beschriebenen 3-Achsen-Fräsen erheblich erweitert. Beim 4-Achsen-Fräsen wird zusätzlich zu den klassischen Bewegungen in der X-, Y- und Z-Achse die Möglichkeit der Drehung des Werkstücks um die Achsen (X oder Y) eingeführt. Dadurch können die Werkstücke von verschiedenen Seiten bearbeitet werden, ohne dass sie manuell umpositioniert werden müssen, was nicht nur die Bearbeitungspräzision erhöht, sondern auch die Produktionszeit verkürzt. Herausforderungen und Lösungen bei der 4-Achsen-Bearbeitung Das 4-Achsen-Fräsen hat die Hersteller vor neue Herausforderungen gestellt, wie z. B. den Bedarf an spezieller Software zur Programmierung der Werkzeugwege und höhere Anforderungen an die Qualifikation der Bediener. Was ist die 5-Achsen-CNC-Bearbeitung, und welche Vorteile bietet sie? Das 5-Achsen-CNC-Fräsen ist die fortschrittlichste Form der Bearbeitung, bei der die herkömmlichen drei Achsen (X, Y, Z) durch zwei zusätzliche Drehachsen (A und B oder C) ergänzt werden, mit denen das Werkstück gedreht und gekippt werden kann, sodass fast jeder Punkt des Werkstücks von einer einzigen Aufspannung aus zugänglich ist. Dies ermöglicht die Bearbeitung komplexer Formen mit hoher Maßhaltigkeit und Oberflächenqualität. Vorteile des 5-Achsen-Fräsens Obwohl 5-Achsen-Maschinen in der Anschaffung und im Betrieb teurer sind, kann ihre Fähigkeit, komplexe Teile schnell und genau zu bearbeiten, die Produktionskosten pro Einheit erheblich senken. Durch die Möglichkeit, mehrere Bearbeitungsvorgänge in einer einzigen Werkstückposition durchzuführen, wird die Produktionszeit erheblich verkürzt, da die Notwendigkeit mehrerer Ausspannungen und Einrichtungsvorgänge entfällt und eine gleichmäßigere Oberflächenqualität erzielt wird. Zusammenfassung: Welche Vorteile bietet das 4- und 5-Achsen-Fräsen bei der Herstellung mechanischer Komponenten? Bei SIM Gdynia hat uns das 4- und 5-Achsen-Fräsen in die Lage versetzt, die Grenzen der traditionellen Bearbeitung zu überwinden und komplexe Formen und Oberflächen zu produzieren, die zuvor außerhalb unserer Möglichkeiten lagen. Durch den Einsatz von Bearbeitungszentren wie der 4-achsigen RWA 250L G (Tsudakoma) und der 5-achsigen 5A201FA (Nikken) konnten wir erhebliche Vorteile erzielen, wie z. B. die Verringerung der für die Produktionsvorbereitung und -durchführung erforderlichen Zeit, die Steigerung der Prozesseffizienz, die Minimierung des Materialabfalls und die Senkung der Arbeitskosten durch die Automatisierung und Integration von Bearbeitungsvorgängen. Die Möglichkeit der Feinabstimmung des Werkzeugwinkels beim 5-Achsen-Fräsen hat die Oberflächenqualität unserer Produkte erheblich verbessert und gleichzeitig unsere Fertigungsmöglichkeiten für anspruchsvollere Sektoren wie die Militär- und Luftfahrtindustrie geöffnet.
Was ist CAD/CAM-Integration undwie lässt sie sich auf die CNC-Bearbeitungübertragen?

Einführung in die CAD/CAM-Technologie In einer Welt, in der dynamische Veränderungen und Innovationen in der zerspanendenIndustrie an der Tagesordnung sind, werden CAD- (Computer-Aided Design) undCAM-Technologien (Computer-Aided Manufacturing) zu unverzichtbaren Säulen desSektors. Im Zeitalter der Digitalisierung und Automatisierung erleichtern CAD und CAM nichtnur die Prozesse, sondern revolutionieren auch die Art und Weise, wie Produkte entworfenund realisiert werden. CAD, mit seinem Schwerpunkt auf digitalem Design, ermöglicht dieErstellung komplexer Modelle und Pläne mit einer Präzision, die bisher nicht möglich war.CAM wiederum, als Werkzeug zur Optimierung von Fertigungsprozessen, setzt dieseEntwürfe in fertige Produkte um, wodurch die Produktionszeit verkürzt und die Genauigkeiterhöht wird.Das heutige Fertigungsumfeld verlässt sich zunehmend auf die Synergie von CAD undCAM, um den wachsenden Anforderungen des Marktes an Geschwindigkeit, Flexibilität und individuelle Angebote gerecht zu werden. Das Verständnis der Auswirkungen dieserTechnologien auf die Industrie ist der Schlüssel, um ihre Rolle bei der Gestaltung derZukunft des Fertigungssektors zu verstehen. Was ist CAD? Die CAD-Technologie (Computer-Aided Design) ist das Herzstück des modernen Ingenieurs-und Architekturdesigns. Sie ist ein wichtiges Werkzeug für die Erstellung komplexer und präziser digitaler Modelle und wirkt sich auf alle Aspekte der Fertigung aus. CAD ermöglichteine schnelle Visualisierung, Analyse und Anpassung von Entwürfen, was zu einerVerkürzung der Entwurfszeit und einer Steigerung der Effizienz führt.Der Hauptvorteil ist die Möglichkeit, detaillierte 2D- und 3D-Modelle zu erstellen, die leichtgeändert und angepasst werden können. Diese Flexibilität ermöglicht es denKonstrukteuren, eine Vielzahl von Lösungen zu erforschen und schnell Änderungenvorzunehmen, um auf veränderte Anforderungen oder erhaltenes Feedback zu reagieren.Darüber hinaus unterstützt CAD den Entscheidungsprozess, indem es Simulationen undAnalysen ermöglicht, die die Leistung und Funktionalität eines Projekts vor der Ausführungbewerten. Was ist CAM? Die computergestützte Fertigung (CAM) ist die Technologie, die benötigt wird, umCAD-Konstruktionen in fertige Produkte umzuwandeln. Es handelt sich um einProduktionsmanagement-Tool, das CNC-Maschinen (Computer Numerical Control) undandere Fertigungsanlagen steuert und die Umsetzung digitaler Modelle in physischeKreationen ermöglicht.Der Unterschied zwischen CAM und CAD liegt in ihrer direkten Anwendung: CADkonzentriert sich auf die Erstellung von Modellen, während CAM diese Entwürfe in die Praxisumsetzt. CAM rationalisiert Fertigungsprozesse wie Fräsen, Drehen, Schneiden oder3D-Drucken und ermöglicht so mehr Präzision, Effizienz und eine Minimierung von Fehlern.In einer Zeit, in der Geschwindigkeit und Flexibilität in der Produktion wichtig sind, ermöglichtCAM eine schnelle Anpassung an veränderte Markt- und Designanforderungen. Mit derFähigkeit, Fertigungsprozesse schnell an Änderungen in CAD-Konstruktionen anzupassen,ist CAM besonders wertvoll in Branchen, die kleine Produktionsläufe oderProduktpersonaldosierung erfordern. CAD/CAM-Integration: Definition und Vorteile Die Integration von CAD- (Computer-Aided Design) und CAM-Technologien(Computer-Aided Manufacturing) ist eine wichtige Strategie in modernenFertigungsprozessen. Sie ermöglicht einen nahtlosen Übergang vom Design zurProduktrealisierung. Ein Hauptvorteil dieser Integration ist die Beschleunigung desFertigungsprozesses durch die direkte Kommunikation zwischen den Modulen, die schnelleDesignänderungen und kürzere Vorlaufzeiten ermöglicht.Die CAD/CAM-Integration verringert auch das Risiko von Fehlern bei der Datenübertragung.Ein integriertes System verbessert die Zusammenarbeit zwischen Konstruktions- undProduktionsteams und trägt so zu einem besseren Projektmanagement und einer größerenFlexibilität bei der Anpassung an Kundenanforderungen bei.Darüber hinaus verringert die Verwendung eines einzigen integrierten Systems denSchulungsbedarf und die Kosten für die Softwarepflege. Folglich rationalisiert dieCAD/CAM-Integration nicht nur den Fertigungsprozess, sondern stärkt auch die Produktivitätund Wettbewerbsfähigkeit eines Unternehmens auf dem Markt erheblich. Auswirkungen des MasterCam X22 CAD/CAM-Systems aufdie Fertigung bei SIM Gdynia Ab Januar 2024 verfügen wir bei SIM Gdynia über das CAD/CAM-System MasterCam X22,das eine Schlüsselrolle in unserer maßgeschneiderten Fertigung mechanischerKomponenten für eine Vielzahl von Branchen spielt. Es ist nicht nur unsere wichtigsteKonstruktionssoftware, sondern auch ein Werkzeug, das wir ständig weiterentwickeln, ummit den neuesten Trends Schritt zu halten und die Standards auf höchstem Niveau zuhalten.Mit MasterCam X22 ist unsere Fertigung schneller und genauer geworden, was sich direkt inkürzeren Vorlaufzeiten und einer schnelleren Auslieferung der fertigen Produkte an dieKunden niederschlägt. Die Integration von CAD und CAM in einem einzigen System machtden Arbeitsablauf reibungsloser, verringert das Fehlerrisiko und macht die Zusammenarbeitzwischen den Abteilungen effizienter.Alles in allem ist MasterCam X22 für uns mehr als nur eine Software – es ist der Schlüsselzu effizienterer Arbeit und besserer Anpassung an die Anforderungen unserer Kunden.
Verkaufsautomaten in derCNC-Bearbeitungsindustrie – dasMATRIX-System von Iscar
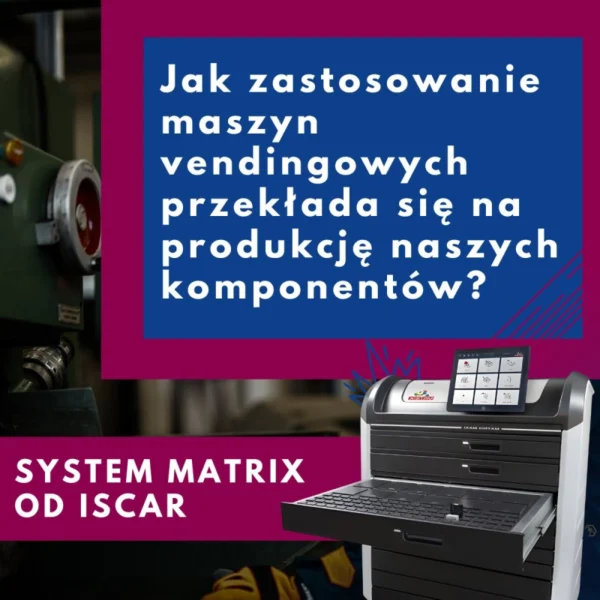
ISCAR – MATRIX Hersteller Unternehmensprofil Als etablierter Hersteller von Zerspanungswerkzeugen konzentriert sich Iscar auf dieEntwicklung und Bereitstellung von Lösungen für spezielle Anwendungen in derMetallbearbeitung. Ihr Portfolio umfasst eine breite Palette von Werkzeugen, von Fräsernund Bohrern bis hin zu fortschrittlichen Drehwerkzeugen.In diesem Artikel konzentrieren wir uns auf einen der interessanteren Aspekte derGeschäftstätigkeit von Iscar – ihre Verkaufsautomaten. Obwohl das Konzept der Automatenin einem industriellen Kontext etwas unkonventionell klingen mag, revolutionieren dieseSysteme die Art und Weise, wie Werkzeuge in einer Fertigungsumgebung verwaltet werden,und bieten einzigartige Lösungen für die Werkzeugverfügbarkeit, die Kontrolle und dieEffizienz der Werkzeugnutzung. Werkzeugverwaltungssystem MATRIX Das von ISCAR entwickelte MATRIX-System ist eine Asset-Management-Plattform, die dieOrganisation und den Zugang zu Werkzeugen in einer Fertigungsumgebung revolutioniert.MATRIX ist viel mehr als ein herkömmliches Lager; es ist ein integriertes System, das dieAutomatisierung nutzt, um Werkzeuge in Echtzeit zu verfolgen, zu verwalten und zu liefern.Seine Implementierung, wie die von SIM Gdynia, trägt zur Rationalisierung vonFertigungsprozessen bei, indem es sofortigen Zugriff auf benötigte Ressourcen ermöglicht.Ein Hauptmerkmal von MATRIX ist die automatische Erfassung des Verbrauchs und dieAnpassung des Angebots, wodurch das Risiko von Ausfallzeiten aufgrund vonWerkzeugmangel minimiert wird. Mit diesem System können Unternehmen die mitÜberbeständen verbundenen Kosten erheblich senken und Einkäufe besser planen, was zueiner höheren betrieblichen Gesamteffizienz führt. Kapazität des MATRIX-Systems Das MATRIX-System von ISCAR zeichnet sich durch eine beeindruckende Flexibilität beider Lagerung von Werkzeugen unterschiedlicher Größe und Form aus, dank derSchubladen mit unterschiedlichen Höhen von 50 mm bis 125 mm. Diese Vielseitigkeit ist derSchlüssel zur Handhabung einer breiten Palette von Teilen, einschließlich Einsätzen, Lehrenund größerem Zubehör. Darüber hinaus ermöglicht die Jumbo-Schubladenoption, eine vonvielen verfügbaren Konfigurationen, die sichere Aufbewahrung von schwereren Werkzeugenmit einer maximalen Last von bis zu 90 kg pro Schublade. Diese Spezifikation ist ein Beweisfür die robuste Konstruktion des Systems, das sich an eine Vielzahl vonLagerungsanforderungen anpassen kann, von leichten Komponenten bis hin zu schwererenWerkzeugen. Spezifikation Das MATRIX-System von ISCAR beinhaltet eine Reihe von technologischen Lösungen, diedie Standards für die Werkzeugverwaltung in einer industriellen Umgebung deutlicherhöhen. Die Benutzeroberfläche ist intuitiv und in zwei Versionen erhältlich: TOUCH undPOD. Die Version TOUCH, die mit einem eigenständigen PC, einem 17-Zoll-Touchscreenund einem fortschrittlichen USV-Schutzsystem ausgestattet ist, bietet Zuverlässigkeit undBenutzerfreundlichkeit. POD-Version, die als zusätzliche Erweiterung konzipiert ist,ermöglicht die Integration in bestehende Systeme.MATRIX ist außerdem mit einem Auto-Lock-Mechanismus ausgestattet, der die Behältersichert, wenn die Schublade geschlossen ist, und so für zusätzliche Sicherheit und Kontrolleder Güter sorgt.Auch Lösungen wie RFID- und Fingerabdruckleser sind erhältlich, die die Sicherheit erhöhenund eine genaue Verfolgung der Werkzeugnutzung ermöglichen.Der Schrankrahmen ist mit verstellbaren Füßen und einer abnehmbaren Frontplatteausgestattet, die den Zugang für Gabelstapler erleichtert. Die Abmessungen des Schranks,die Konstruktionsmaterialien und die Farboptionen sind auf Langlebigkeit und Ästhetikausgelegt, und die gesamte Fertigung erfolgt gemäß den ISO9001-2008-Normen, was einezertifizierte Qualität garantiert. Zusammenfassung – welche Vorteile das MATRIX-System von Iscar für SIM Gdynia gebracht hat Die Implementierung des MATRIX-Systems von ISCAR bei SIM Gdynia hat wesentlich zurVerbesserung des Ressourcenmanagements beigetragen. Die von MATRIX angeboteneAutomatisierung der Werkzeugversorgung hat die Produktionsausfallzeiten durch diekontinuierliche Bereitstellung der benötigten Werkzeuge reduziert. Dies führt direkt zu einerhöheren Betriebseffizienz und geringeren Lagerkosten, da die Lieferungen genau auf denaktuellen Bedarf abgestimmt werden. Die Sicherheitsfunktionen des Systems, wie z. B. der Auto-Lock-Mechanismus und dieIntegration von RFID-Technologie und Fingerabdrucklesern, haben die Kontrolle über dasInventar verbessert und das Risiko eines unbefugten Zugriffs oder Verlusts minimiert. Dieshat es unserer Organisation ermöglicht, Ressourcen besser zu verwalten und dieGesamtkontrolle über die Produktionsprozesse zu verbessern.Die positiven Auswirkungen von MATRIX auf SIM Gdynia zeigten sich auch in einemverbesserten Arbeitsablauf und einer höheren Mitarbeiterzufriedenheit. Der einfache Zugangzu den Werkzeugen und die gestrafften Arbeitsabläufe steigerten die Effizienz des Teams.Dies führte nicht nur zu finanziellen Vorteilen, sondern auch zu einer deutlichenVerbesserung der Arbeitsmoral unserer Mitarbeiter, was für die Aufrechterhaltung einerhohen Produktivität und Qualität der Arbeit wichtig ist.
Enforce Tac 2024 – Konferenz der Verteidigungs- und Sicherheitsindustrie

Was ist die Enforce Tac und wie verlief sie im Jahr 2024? Die Enforce Tac 2024 war ein Meilenstein im internationalen Messekalender und konzentrierte sich auf die neuesten Technologien und Lösungen in der Verteidigungs- und Sicherheitsindustrie. Die Messe, die drei Tage lang im Herzen Europas stattfand, brachte prominente Experten, Innovatoren und Vertreter des Militärs und der öffentlichen Sicherheit aus allen Teilen der Welt zusammen. In einer Atmosphäre, die auf den Austausch von Wissen und Erfahrungen ausgerichtet war, präsentierte die Enforce Tac 2024 die neuesten technologischen Entwicklungen und öffnete den Besuchern die Tür zur Zukunft der Sicherheit auf globaler Ebene. Auf der Messe wurden nicht nur die neuesten Waffensysteme, Spezialfahrzeuge, Überwachungs- und Aufklärungstechnologien vorgestellt, sondern auch eingehende Diskussionen über die Ausrichtung des Sektors, die Herausforderungen, denen sich die Welt heute gegenübersieht, und die Frage, wie neue Technologien angepasst werden können, um mehr Sicherheit auf nationaler und internationaler Ebene zu gewährleisten. Teilnehmerprofil und Atmosphäre auf der Enforce Tac 2024 Mit mehr als 12.000 Fachleuten und Experten aus 86 Ländern bot die Enforce Tac 2024 einen Ort der internationalen Zusammenarbeit und des Ideenaustauschs. Die Messe zog ein breites Spektrum von Teilnehmern an, darunter Vertreter staatlicher Sicherheitsbehörden, der Streitkräfte, von Unternehmen der Rüstungsindustrie, Technologie-Start-ups sowie unabhängige Sicherheitsexperten und -analysten. Die einzigartige, diskrete Atmosphäre der Veranstaltung, kombiniert mit einem Höchstmaß an Professionalität und Exklusivität, schuf ein ideales Umfeld für offene, aber dennoch tiefgreifende Diskussionen. Aussteller und Besucher hatten gleichermaßen die einmalige Gelegenheit, wertvolle Geschäftskontakte zu knüpfen, Erfahrungen auszutauschen und mögliche Entwicklungs- und Kooperationsrichtungen zu diskutieren. Die besondere Atmosphäre der Enforce Tac, die sich auf Innovation, Technologie und die Zukunft der Verteidigung konzentrierte, bestätigte ihren Status nicht nur als Veranstaltungsort für die Präsentation von Errungenschaften, sondern vor allem als Plattform zur Förderung der internationalen Entwicklung und Zusammenarbeit im Sicherheitssektor. Innovationen und vorherrschende Trends auf der Enforce Tac 2024 Waffen und Munition Einer der am stärksten frequentierten Bereiche auf der Enforce Tac 2024 war die Präsentation fortschrittlicher Waffenlösungen, einschließlich moderner Kleinwaffensysteme, Artillerie und Spezialmunition. Zu den ausgestellten Innovationen gehörten unter anderem modulare Systeme, die eine schnelle Anpassung der Waffen an eine Vielzahl von Einsatzaufgaben ermöglichen, sowie Munition mit intelligenten Gefechtsköpfen, die in der Lage sind, Ziele präzise zu treffen und gleichzeitig die Verluste zu minimieren. Fahrzeug-Innovation Der Bereich der unbemannten Fahrzeuge (UxV), der sowohl landgestützte (UGV), luftgestützte (UAV) als auch maritime (USV) Plattformen umfasst, präsentierte die neuesten Entwicklungen in den Bereichen Autonomie, Überlebensfähigkeit und Interoperabilität. Der Schwerpunkt lag auf Fahrzeugen, die in komplexen städtischen Umgebungen und schwierigem Gelände operieren können und Unterstützung bei der Aufklärung, der Logistik und der direkten Kampfunterstützung bieten. Zu den Demonstrationen gehörten auch autonome Systeme, die in der Lage sind, Aufklärungsmissionen und Angriffe auf bestimmte Ziele ohne direkte Überwachung durch den Bediener selbstständig durchzuführen. Sichttechnologien und Optoelektronik Jüngste Entwicklungen im Bereich der Wärmebild-, Nachtsicht- und optoelektronischen Technologien verdeutlichten ihre wachsende Rolle bei der Modernisierung von Zielerfassungs-, Aufklärungs- und Überwachungssystemen. Die Entwicklungen in diesen Technologien ermöglichen den Einsatz bei allen Licht- und Witterungsbedingungen. Zu den Innovationen in diesem Bereich gehören die Miniaturisierung der Systeme, die Erhöhung der Auflösung und der Empfindlichkeit der Detektoren sowie die Integration mit Systemen der künstlichen Intelligenz zur automatischen Identifizierung und Klassifizierung von Zielen. Angebot an Sonderveranstaltungen Die Enforce Tac 2024 zeichnete sich durch eine Vielzahl von Sonderveranstaltungen aus, die den Besuchern einzigartige Erfahrungen und Einblicke in die praktische Anwendung der ausgestellten Technologien boten. Workshops und Seminare befassten sich mit den neuesten Strategien in den Bereichen Verteidigung, Krisenmanagement und Cybersicherheit, während Podiumsdiskussionen mit renommierten Experten die Zukunft der Militärtechnologie, die Herausforderungen bei der Implementierung autonomer Systeme und die ethischen Aspekte des Einsatzes neuer Technologien in bewaffneten Konflikten zum Thema hatten. Das Enforce Tac Village und die BLACKBOX waren Schlüsselbereiche, in denen die Teilnehmer die Möglichkeit hatten, die neuesten Waffensysteme, unbemannten Fahrzeuge und optischen Technologien aus erster Hand zu erleben. Das Enforce Tac Village bot dynamische Vorführungen in realistischen Einsatzszenarien, während die BLACKBOX es ermöglichte, die Ausrüstung unter Bedingungen zu testen, die realen Einsätzen ähneln, einschließlich Low-Light- oder Wärmebildtechnologie, was eine umfassende Bewertung ihrer Funktionalität und Leistung ermöglichte. Die Teilnahme von SIM Gdynia an Enforce Tac 2024 Als Hersteller von Drohnenkomponenten, Schalldämpfern und Gehäusen für elektronische Systeme ist es für die Erhaltung unserer Wettbewerbsfähigkeit auf dem Markt unerlässlich, die neuesten Trends und Technologien im Auge zu behalten. Die Veranstaltung ermöglichte es uns, uns mit den künftigen Anforderungen des Verteidigungs- und Sicherheitssektors zu befassen, was für die Weiterentwicklung und Innovation unserer Produkte von unschätzbarem Wert ist.
Was ist TEM-Entgraten und welche Vorteile bringt es der polnischen Industrie?
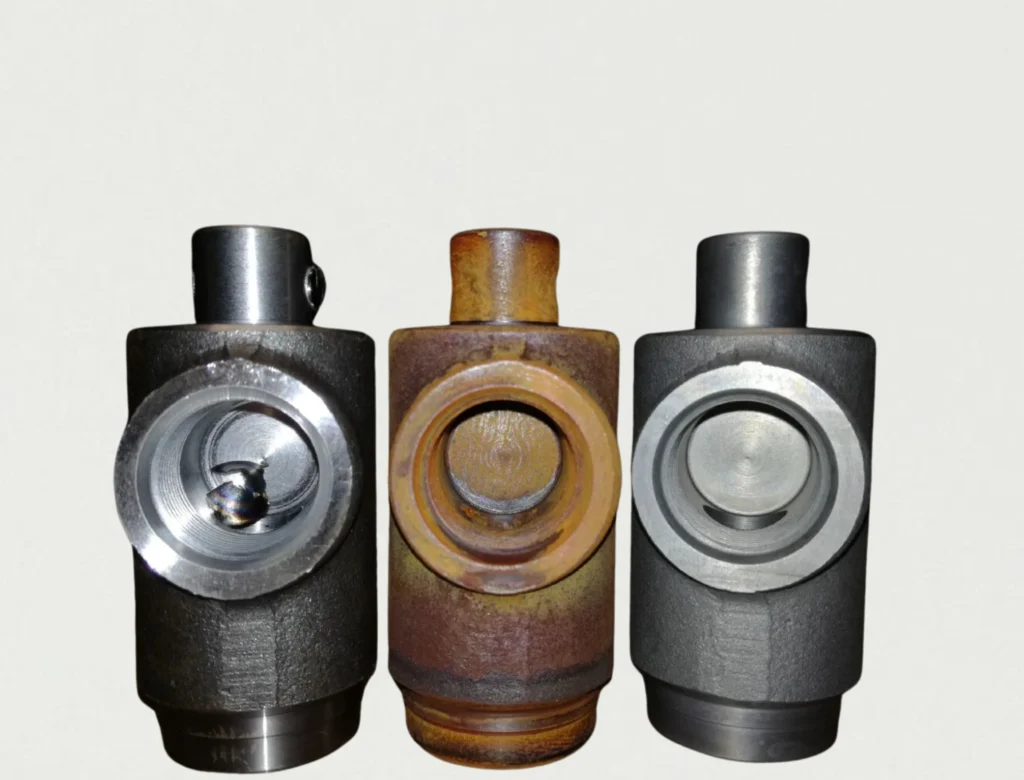
Definition und Bedeutung des TEM-Entgratens Das TEM-Entgraten (Thermal Energy Method) ist eine fortschrittliche Methode zur Entfernung von Graten und zum Entgraten von Metallteilen, die eine Schlüsselrolle bei der Präzisionsbearbeitung spielt. Bei diesem Verfahren wird das Werkstück in eine hermetisch abgeschlossene Kammer gelegt, in die ein Gemisch aus brennbaren Gasen (z. B. Methan, Wasserstoff) und Sauerstoff eingeleitet wird. Die Zündung dieses Gemischs bewirkt einen raschen Temperaturanstieg auf etwa 3.500 °C, was zu einer effektiven Verbrennung und Entgratung führt. Der Schlüsselaspekt ist die genaue Steuerung der Wärmeausbreitung, um eine gleichmäßige Entfernung unerwünschter Elemente ohne Beschädigung des Werkstücks zu gewährleisten. Das Verfahren wird wissenschaftlich als „thermo-chemisches Entgraten“ bezeichnet und ist nach DIN 8590 der Verfahrensuntergruppe „Chemisches Abtragen“ zugeordnet. TEM-Entgraten bei SIM Gdynia: technologischer Vorsprung Bei SIM Gdynia wird das TEM-Entgraten eingesetzt, um eine außergewöhnliche Präzision bei der Herstellung von Bauteilen zu erreichen. Dank dieser Technik können wir die kompliziertesten und schwer zugänglichen Stellen effektiv entgraten, wo mechanische Mittel versagen würden. Mit diesem Verfahren lassen sich glatte und gleichmäßige Oberflächen erzielen, die für fortschrittliche Anwendungen wie Bauteile in Hydraulik- und Pneumatiksystemen oder Komponenten in der Luft- und Raumfahrt- und Verteidigungsindustrie unerlässlich sind. Als Ergebnis bieten wir Produkte von höchster Qualität und Präzision an und stehen damit an der Spitze der Innovation in der metallverarbeitenden Industrie. Vorteile des TEM-Entgratens für die Industrie Das TEM-Entgraten ist ein „thermochemisches“ Verfahren, das der Industrie einzigartige Vorteile bietet. Das Verfahren ermöglicht die gleichzeitige Entfernung von Außen- und Innengraten in einem einzigen Bearbeitungszyklus, wodurch die Zuverlässigkeit des Prozesses gewährleistet wird. Es beeinträchtigt nicht die Oberflächenstruktur, was für Kunststoffteile wichtig ist. Das Verfahren bietet unvergleichliche Sauberkeit und Zyklusgeschwindigkeiten für hohe Produktionsvolumina bei gleichzeitig niedrigen Energiekosten. Das TEM-Entgraten ist besonders nützlich für Guss- und Drehteile und Verteilerblöcke sowie für die Herstellung von Komponenten für Hydraulik- und Pneumatikventile. Materialbeschränkungen beim TEM-Entgraten Obwohl das TEM-Entgraten für viele Werkstoffe geeignet ist, gibt es einige Einschränkungen bei seiner Anwendung. In erster Linie wird das Verfahren nicht für Metalle wie Magnesium empfohlen, da es zu unkontrolliertem Brennen neigt und einen niedrigen Flamm- und Schmelzpunkt hat. Auch Titan ist aufgrund seines sehr hohen Siedepunkts (3535 °C) für das Verfahren nicht geeignet. Darüber hinaus sind hochtemperaturbeständige Werkstoffe, die häufig in der Luft- und Raumfahrtindustrie verwendet werden, wie z. B. Zirkonium, für die TEM-Entgratung ebenfalls nicht geeignet. Aufgrund dieser Materialbeschränkungen müssen die Hersteller für diese speziellen Werkstoffe andere Bearbeitungsmethoden anwenden. Gasförmige Brennstoffquellen beim TEM-Entgraten Beim TEM-Entgraten werden verschiedene Arten von gasförmigen Brennstoffen verwendet. Die wichtigsten Brenngase, die in diesen Maschinen verwendet werden, sind Methan, Erdgas oder Wasserstoff. Es gibt drei Möglichkeiten, diese Gase in die Maschine zu leiten: ein Gas- und Sauerstoffbündel, ein Erdgaskompressor in Kombination mit einem Sauerstoffbündel und ein Erdgaskompressor mit einem Sauerstofftank. Die Wahl der geeigneten Brennstoffquelle hängt von den Maschinenspezifikationen und Prozessanforderungen ab. Post-Gratification-Prozess bei SIM Gdynia: Waschen und Korrosionsschutzbeschichtung Bei SIM Gdynia umfasst der Nachentgratungsprozess ein gründliches Waschen der Bauteile, um Eisenoxidablagerungen nach dem TEM-Entgratungsprozess zu entfernen. Die Reinigungstechnik wird an die Art des Materials angepasst – für Stahl und Gusseisen verwenden wir eine pH-neutrale Reinigung mit Ultraschallunterstützung, für Aluminium und Zink andere Methoden. Nach dem Reinigungsprozess tragen wir Korrosionsschutzbeschichtungen auf, um einen langfristigen Schutz zu gewährleisten und die Materialeigenschaften der Bauteile zu erhalten. Diese besondere Sorgfalt gewährleistet, dass unsere Produkte höchsten Ansprüchen an Qualität und Langlebigkeit gerecht werden. Zusammenfassung Zusammenfassend lässt sich sagen, dass die TEM-Entgrattechnologie, obwohl sie in der polnischen Industrie relativ selten ist, einen bedeutenden Fortschritt in der Präzisionsbearbeitung darstellt. Sie ermöglicht das effektive Entgraten einer Vielzahl von Werkstoffen, wobei die Auswirkungen auf deren Eigenschaften minimiert werden. Nur wenige Unternehmen in Polen verfügen über fortschrittliche TEM-Entgratungsmaschinen, was diese Technologie für diejenigen, die darauf angewiesen sind, besonders wertvoll macht. Es handelt sich um eine Richtung, die mit Sicherheit an Bedeutung gewinnen wird und die Zukunft der Innovation und der Spitzenleistungen in der Fertigung darstellt.
SPECTROMAXx-Spektrometer: Was ist es und wie revolutioniert es die Metallchemie?
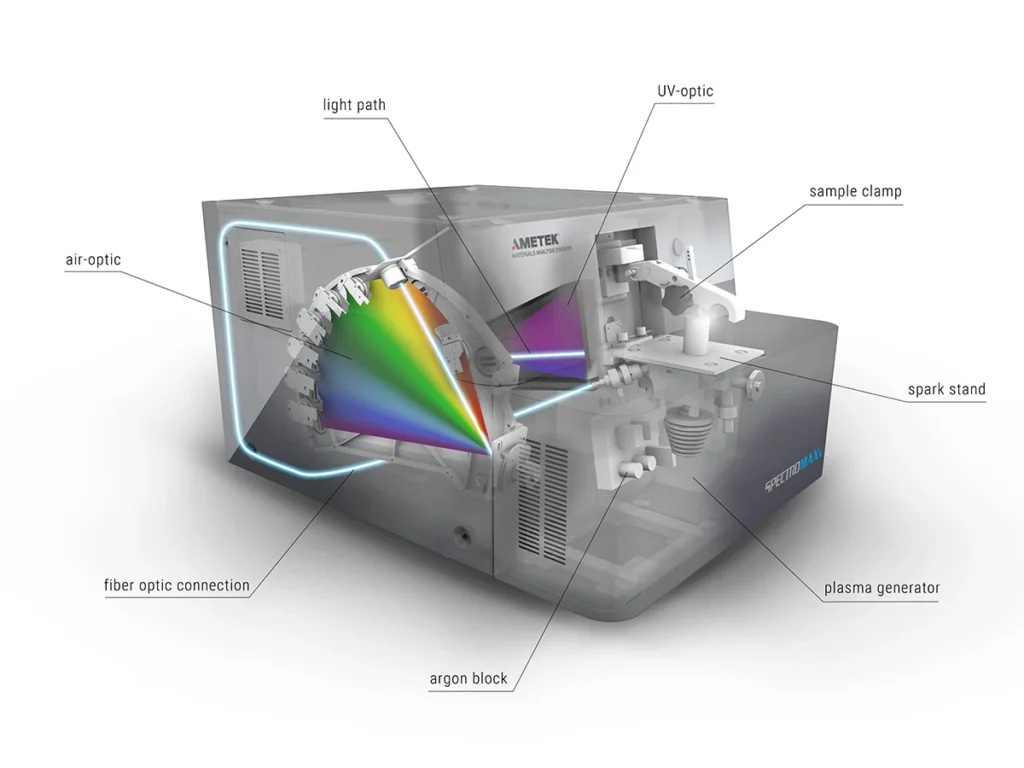
Was ist das SPECTROMAXx-Spektrometer? Das SPECTROMAXx-Spektrometer ist ein hochmodernes Analyseinstrument, das bei der präzisen Analyse der chemischen Zusammensetzung von Metallen eine Schlüsselrolle spielt. Als ARC/SPARK OES (Optical Emission Spectrometry)-Gerät nutzt das SPECTROMAXxx-Spektrometer die Technik der optischen Emissionsfunken-Spektrometrie. Dabei wird durch einen Funken, der zwischen einer Probe und einer Elektrode erzeugt wird, Licht verschiedener Wellenlängen emittiert, das dann vom Spektrometersystem analysiert wird. Diese Analyse ermöglicht die Identifizierung und Quantifizierung der in der Probe vorhandenen Elemente. Die Bedeutung des SPECTROMAXx-Spektrometers in der Industrie ist immens. Es ist von unschätzbarem Wert für die Qualitätskontrolle von Materialien, die Identifizierung unbekannter Metalle und die Forschung und Entwicklung neuer Legierungen. Die Einsatzmöglichkeiten sind vielfältig und reichen von Eisen- und Nichteisenmetallgießereien über metallverarbeitende Betriebe bis hin zu modernen Forschungslabors. Das Gerät liefert schnelle, genaue und zuverlässige Ergebnisse, was für die Aufrechterhaltung hoher Produktqualitäts- und Sicherheitsstandards entscheidend ist. Einführung in das SPECTROMAXx Als Innovation in der Materialanalyse ist das Spektrometer SPECTROMAXx ein unverzichtbares Werkzeug in modernen Industrielabors. Mit der zehnten Generation dieses Geräts wurde eine Reihe bedeutender Verbesserungen eingeführt, die die Standards für die Genauigkeit und Präzision der Analyse erhöhen. Neue Werkskalibrierungen, erweiterte Elementauswahlbereiche und optimierte Quellenanregungsparameter verbessern die Nachweisgrenzen (LODs) erheblich. Diese Verbesserungen machen das SPECTROMAXx noch vielseitiger und effektiver für die Untersuchung eines breiten Spektrums von Materialien. Die Modernität und Innovation des SPECTROMAXxx zeigt sich nicht nur in seinen analytischen Fähigkeiten, sondern auch in seiner Benutzerfreundlichkeit und Zuverlässigkeit. Die Verbesserungen der zehnten Generation des Spektrometers spiegeln die wachsenden Anforderungen der metallurgischen Industrie und den Bedarf an schnelleren und effizienteren Prüfgeräten wider. Das SPECTROMAXx erfüllt nicht nur diese Anforderungen, sondern setzt auch neue Maßstäbe bei der Analyse der chemischen Zusammensetzung von Metallen und ist damit ein wichtiges Werkzeug für Metallurgie- und Werkstoffwissenschaftler, Ingenieure und Techniker. Technische Spezifikationen und Merkmale Als Ergebnis fortschrittlicher Forschung und Entwicklung bietet das SPECTROMAXx-Spektrometer eine Reihe beeindruckender technischer Daten und Funktionen, die seine Position als eines der führenden Geräte für die Analyse der chemischen Zusammensetzung von Metallen untermauern. Neue Funktionen der zehnten Generation Die zehnte Generation des SPECTROMAXx zeichnet sich durch völlig neue Werkskalibrierungen aus, die auf die neuesten Industriestandards und -anforderungen zugeschnitten sind. Die erweiterten Kalibrierbereiche ermöglichen eine noch genauere Analyse eines größeren Spektrums von Elementen, was besonders in Branchen wichtig ist, in denen hohe Präzision gefordert ist, wie etwa in der Luft- und Raumfahrt oder der Medizin. Optimierte Anregungsparameter der Quelle, die in der Funkenspektrometrie von zentraler Bedeutung sind, tragen zu verbesserten Nachweisgrenzen (LODs) bei und ermöglichen die Identifizierung und Quantifizierung selbst kleinster Elementspuren. Diese Verbesserungen machen SPECTROMAXx präziser und zuverlässiger als je zuvor. Optik und Sensorik In der Basisversion des SPECTROMAXx kommt eine innovative Single-Air-Optik zum Einsatz, die in Kombination mit CCD-Sensoren eine hohe Auflösung und präzise Spektralanalyse ermöglicht. Diese Sensortechnologie hat sich bewährt und wird wegen ihrer außergewöhnlichen Widerstandsfähigkeit gegenüber Schwankungen der Umgebungstemperatur geschätzt, was der Schlüssel zu stabilen Messbedingungen und zuverlässigen Ergebnissen ist. Das Spektrometer deckt den Wellenlängenbereich von 233 nm bis 670 nm ab und ermöglicht so die Analyse eines breiten Spektrums von Elementen. Die neue Version des SPECTROMAXx Advanced hingegen verfügt über eine neue UV-Optik, die mit vier hochauflösenden CMOS-Detektoren ausgestattet ist und eine noch genauere Spektralanalyse ermöglicht, insbesondere im kurzwelligen Bereich, der für die Identifizierung bestimmter Elemente und ihrer Isotope wichtig ist. iCAL 2.0 ARC/SPARK OES-Analysator Das neue SPECTROMAXx mit iCAL 2.0 ARC/SPARK OES-Analysator stellt die technologische Spitze auf dem Gebiet der optischen Emissionsfunken-Spektrometrie dar. Er zeichnet sich vor allem durch seine bewährte Genauigkeit und außergewöhnliche Schnelligkeit aus, die in industriellen Umgebungen, in denen Zeit und Präzision eine große Rolle spielen, entscheidend sind. Durch die schnelle Standardisierung des Geräts wird die Vorbereitungszeit für die Analysen minimiert, was sich erheblich auf die Gesamtproduktivität des Labors auswirkt. Darüber hinaus machen der geringe Gasverbrauch und die niedrigen Wartungskosten das SPECTROMAXx für viele Unternehmen zu einer wirtschaftlichen und umweltfreundlichen Wahl. Diese Kombination von Merkmalen macht das SPECTROMAXx mit iCAL 2.0 nicht nur zu einem technologisch fortschrittlichen Gerät, sondern auch zu einer praktischen und kostengünstigen Lösung für die Metallindustrie. Anwendungen in der Metallindustrie und in Gießereien Das SPECTROMAXx-Spektrometer kommt in einer Reihe von kritischen Bereichen der Metall- und Gießereiindustrie zum Einsatz und spielt eine grundlegende Rolle bei der Qualitätssicherung und der Einhaltung von Industriestandards. In der Metallproduktion, wo eine präzise Analyse der chemischen Zusammensetzung für die Erhaltung der Materialeigenschaften unerlässlich ist, ist das SPECTROMAXxx ein wichtiges Werkzeug. Das Gerät wird zur Bestimmung aller in der Metallindustrie verwendeten Elemente eingesetzt, einschließlich der detaillierten Spurenanalyse von Elementen wie Kohlenstoff, Phosphor, Schwefel und Stickstoff, die für die mechanischen Eigenschaften und die Korrosionsbeständigkeit von Metallen entscheidend sind. In Gießereien für Eisen- und Nichteisenmetalle, in denen eine hohe Präzision bei der Bestimmung der Legierungszusammensetzung erforderlich ist, ermöglicht SPECTROMAXx eine schnelle und genaue Analyse, die sicherstellt, dass jede Gusscharge den festgelegten Spezifikationen entspricht. Mit seiner Fähigkeit, ein breites Spektrum von Komponenten schnell zu scannen, ist dieses Spektrometer von unschätzbarem Wert für die Qualitätskontrolle, da es die sofortige Erkennung und Korrektur von Unstimmigkeiten in der chemischen Zusammensetzung ermöglicht. Seine Anwendung erstreckt sich auch auf metallverarbeitende Betriebe, wo die Analyse der Zusammensetzung entscheidend ist, um die Einhaltung der technischen Anforderungen und die Sicherheit der Endprodukte zu gewährleisten. Leistung und Effizienz Die neue Generation des SPECTROMAXx-Spektrometers zeichnet sich durch hohe Leistungsfähigkeit und Effizienz aus und hat sich damit in der Branche einen Namen gemacht. Die in der neuesten Version des Geräts eingeführte Funkenparameter-Optimierung ermöglicht eine Reduzierung der Messzeit um 12 Prozent, was in der schnelllebigen Umgebung moderner Labore von entscheidender Bedeutung ist. Diese Funktion ist besonders wichtig in Situationen, in denen sich die Reaktionszeiten direkt auf die Produktionsprozesse auswirken, da sie eine schnellere Analyse und geringere Ausfallzeiten ermöglicht. Der geringere Verbrauch von Verbrauchsmaterialien führt zu niedrigeren Betriebskosten und einer geringeren Umweltbelastung – ein wichtiger Aspekt in der heutigen Zeit, in der Nachhaltigkeit immer wichtiger wird. Das SPECTROMAXx-Spektrometer zeichnet sich außerdem durch eine hohe Wiederholbarkeit, Reproduzierbarkeit und Zuverlässigkeit der Ergebnisse aus. Die Fähigkeit, jedes Mal konsistente und zuverlässige Ergebnisse zu liefern, ist von unschätzbarem Wert in Branchen, in denen jeder Inhaltsstoff entscheidend für die Sicherheit und Leistungsfähigkeit des Endprodukts
Besuch von SIM Gdynia auf der Messe Interlift 2022 in Augsburg
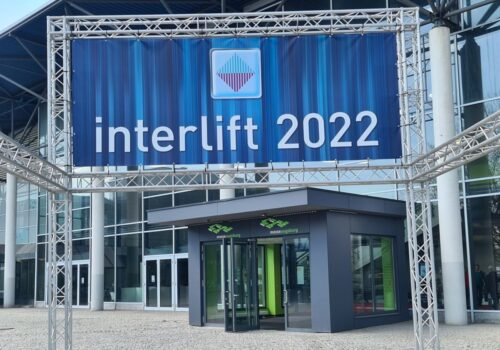
Neue Horizonte Unsere Reise nach Deutschland im April 2022 eröffnete uns neue Horizonte. Es war nicht nur eine Gelegenheit, unsere Kunden zu treffen, sondern auch eine großartige Chance, die führende Fachmesse für die Kranindustrie zu besuchen – die Interlift 2022 in Augsburg. Als führende Veranstaltung der Branche bringt die Interlift Hersteller und Lieferanten von Aufzügen, Komponenten und Zubehör zusammen und bietet uns eine einzigartige Gelegenheit, die Aktivitäten anderer Unternehmen kennenzulernen und neue Möglichkeiten zu erschließen. Neues Aussehen Der Besuch der Interlift 2022 war im Zusammenhang mit unserer jüngsten Investition in SIM Gdynia von besonderer Bedeutung. Vor einigen Monaten wurde unser Maschinenpark durch eine neue Karusselldrehmaschine erweitert, wie wir im Abschnitt „Veranstaltungen“ auf unserer Website berichtet haben. Durch diese bedeutende Aufrüstung konnten wir unsere Kapazitäten für die Bearbeitung großer Werkstücke erweitern. Wir haben diese Informationen mit Begeisterung mit potenziellen neuen Kunden auf der Messe geteilt und unsere Produktionskapazität und Expansionspläne hervorgehoben. Interlift 2022 Die Messe Interlift 2022 bot uns eine Plattform zum Erfahrungsaustausch, zum Kennenlernen der neuesten Trends und Technologien in der Kranbranche und zum Knüpfen neuer Geschäftsbeziehungen. Für uns bei SIM Gdynia ist die aktive Teilnahme an solchen Veranstaltungen nicht nur eine Gelegenheit, unsere Leistungen zu präsentieren, sondern auch eine wertvolle Chance, unser Leistungsspektrum weiterzuentwickeln und auszubauen.
Investitionen in moderne, kosteneffiziente und umweltfreundliche Lösungen
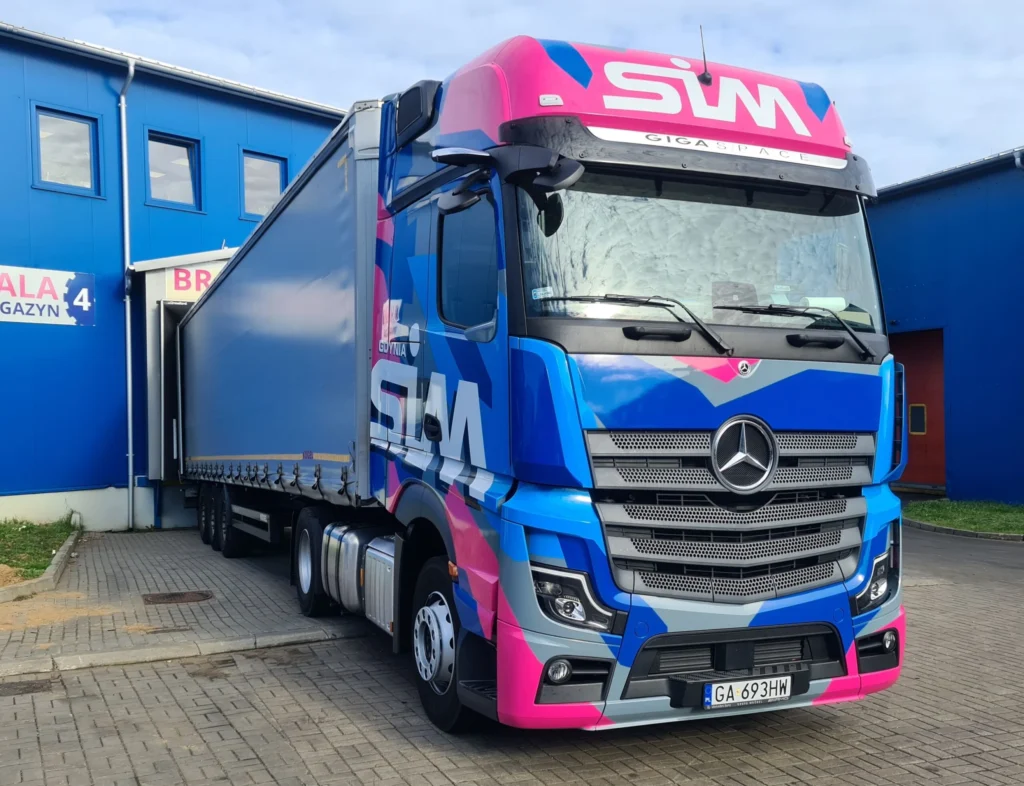
Neuer Mercedes-Benz Traktor Wir engagieren uns sehr für eine nachhaltige Entwicklung, die alle Aspekte unserer Geschäftstätigkeit umfasst. Im Einklang mit dieser Philosophie haben wir Investitionen getätigt, die über moderne Werkzeugmaschinen und Werkzeuge hinausgehen und auch unsere Transportmittel umfassen. Mit großem Stolz präsentieren wir unsere jüngste Anschaffung, die Sattelzugmaschine Actros L 1848 von Mercedes-Benz, die einen wichtigen Schritt zur Erfüllung unserer ökologischen und wirtschaftlichen Verpflichtungen darstellt. Hohe Ansprüche mit Actros L 1848 Der Kauf des Actros L 1848 zeigt unser Engagement für die Aufrechterhaltung eines hohen technologischen Standards in Übereinstimmung mit den Erwartungen unserer Kunden und unseren Verträgen und Vereinbarungen. Diese Investition unterstreicht nicht nur unser Engagement für Arbeitskomfort und Sicherheit, sondern auch für umweltfreundliche Technologien. Aus wirtschaftlicher Sicht ist der Actros L 1848 ein wichtiger Schritt zur Senkung der Betriebskosten und bietet die für unseren Fuhrpark wichtige Kraftstoffeffizienz und Zuverlässigkeit. Eleganz in Firmenfarben Unser neues Fahrzeug erfüllt nicht nur hohe funktionale und ökologische Standards, sondern ist durch sein eindrucksvolles Erscheinungsbild in den Firmenfarben auch ein hervorragendes Aushängeschild für unser Unternehmen.
Fachmesse SUBCONTRACTING 2023 in Poznań
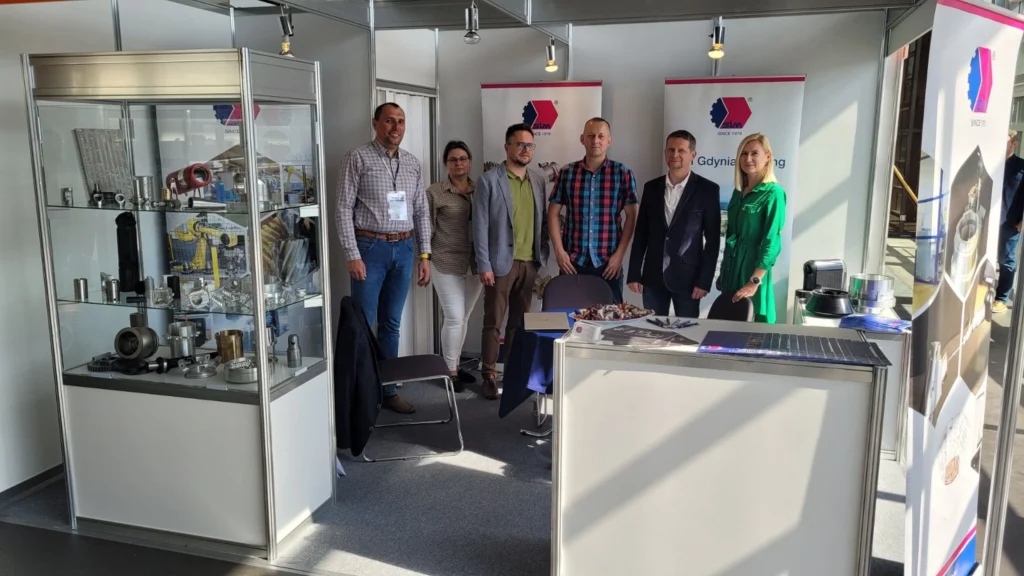
Zurück zur SUBCONTRACTING-Messe Nach einer zweijährigen Pause aufgrund weltweiter Ereignisse waren wir erfreut, zur Messe für industrielle Zusammenarbeit SUBCONTRACTING nach Poznań zurückzukehren. Diese Veranstaltung, die am 2. Juni 2023 stattfand, war eine fantastische Gelegenheit für uns, unsere neuesten Produktions- und Technologiefähigkeiten zu präsentieren. Größerer Stand, mehr Möglichkeiten In diesem Jahr war unsere Präsenz auf der Messe besonders groß – wir stellten in einer größeren Gruppe als je zuvor aus. Unser Team, das sich aus Vertretern verschiedener Abteilungen von SIM Gdynia zusammensetzte, ermöglichte es den Besuchern unseres Standes, ein tieferes Verständnis für unser Angebot zu gewinnen. Durch den direkten Dialog mit potenziellen Kunden konnten wir unsere Kompetenzen, Spezialisierungen und die neuesten Entwicklungen in der CNC-Bearbeitung und anderen fortschrittlichen Technologien genau vorstellen. Treffen mit Geschäftspartnern Die Messe war auch eine hervorragende Gelegenheit, mit unseren bestehenden Geschäftspartnern zusammenzutreffen. Wir schätzen langfristige Beziehungen, und Veranstaltungen wie die SUBCONTRACTING-Messe geben uns die Möglichkeit, diese Beziehungen zu pflegen und zu stärken. Wir haben uns sehr gefreut, dass wir uns wieder persönlich treffen und unsere Zusammenarbeit und Zukunftspläne besprechen konnten.
Zeit für Veränderung
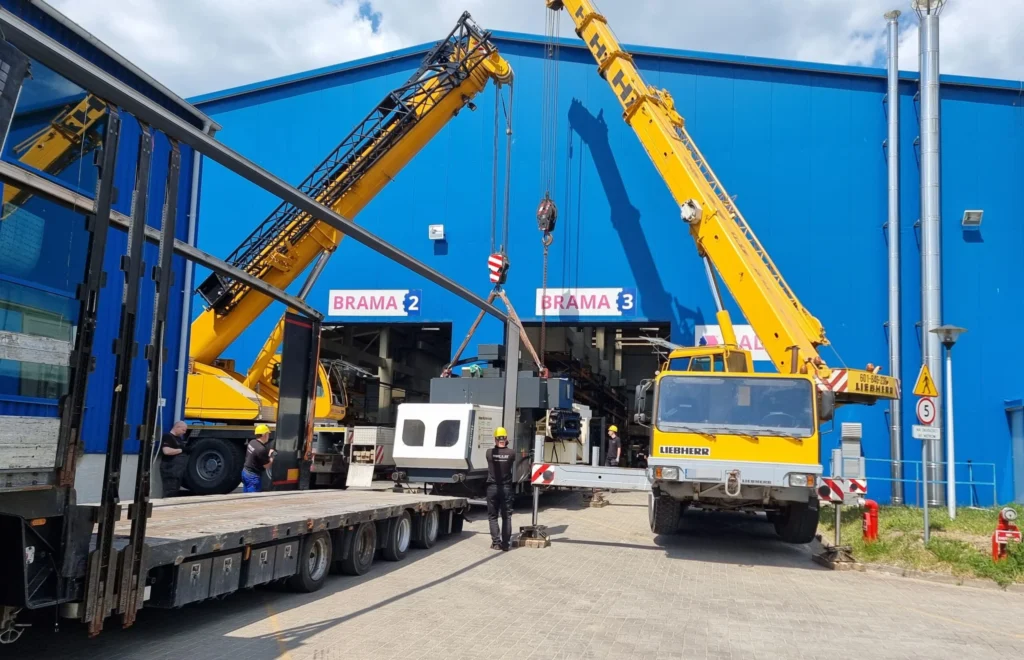
Entscheidungen in der Produktion Wir bei SIM Gdynia sind uns bewusst, dass Fortschritt und Innovation der Schlüssel zum Erhalt unserer Wettbewerbsfähigkeit auf dem Markt sind. Aus diesem Grund haben wir uns entschlossen, erhebliche Veränderungen in unserer Produktionsstätte vorzunehmen. Neue Maschinen, neue Möglichkeiten Im Rahmen dieser Veränderungen wurden zwei ältere Werkzeugmaschinen aus unserer Produktionshalle entfernt. Diese Maschinen haben im Laufe der Jahre eine wichtige Rolle in unserem Produktionsprozess gespielt, aber angesichts des sich schnell verändernden Marktes und der steigenden Anforderungen unserer Kunden haben wir beschlossen, dass es an der Zeit ist, sie durch modernere Einheiten zu ersetzen. Die neuen Maschinen werden nicht nur unseren Maschinenpark bereichern, sondern auch die Produktivität, die Präzision und die Qualität der von uns hergestellten Komponenten erhöhen. Willkommen im neuen Maschinenpark! Wir möchten alle Interessenten, einschließlich unserer Kunden und Partner, dazu auffordern, sich mit der Liste und den technischen Daten der neuen Werkzeugmaschinen vertraut zu machen. Diese Informationen werden regelmäßig unter der Registerkarte „Maschinenpark“ aktualisiert. Die verfügbare Liste enthält detaillierte Informationen über die Fähigkeiten und Spezifikationen der neuen Maschinen.